Steel: Difference between revisions
Undid revision 178907247 by 71.74.208.141 (talk) |
Tritium h3 (talk | contribs) Fixed up first sentence as per MoS |
||
Line 2: | Line 2: | ||
[[Image:Steel wire rope.png|thumb|225px|The steel cable of a [[coal mining|colliery]] winding tower.]] |
[[Image:Steel wire rope.png|thumb|225px|The steel cable of a [[coal mining|colliery]] winding tower.]] |
||
{{wiktionarypar|steel}} |
{{wiktionarypar|steel}} |
||
'''Steel''' |
'''Steel''' is an [[alloy]] consisting mostly of [[iron]], with a [[carbon]] content between 0.2 and 1.7 or 2.04% by weight (C:1000–10,8.67Fe), depending on grade. Carbon is the most cost-effective alloying material for iron, but various other alloying elements are used such as [[manganese]] and [[tungsten]].<ref name=EM2>{{cite book |last=Ashby |first=Michael F. |coauthors=& David R. H. Jones |title=Engineering Materials 2 |origyear=1986 |edition=with corrections |year=1992 |publisher=Pergamon Press |location=Oxford |language=English |id=ISBN 0-08-032532-7 }}</ref> Carbon and other elements act as a hardening agent, preventing [[dislocation]]s in the iron atom [[crystal lattice]] from sliding past one another. Varying the amount of alloying elements and form of their presence in the steel (solute elements, precipitated phase) controls qualities such as the [[Hardness (materials science)|hardness]], [[ductility]], and [[tensile strength]] of the resulting steel. Steel with increased carbon content can be made harder and stronger than iron, but is also more [[brittle]]. The maximum solubility of carbon in iron (in [[austenite]] region) is 2.14% by weight, occurring at 1149 [[Celsius|°C]]; higher concentrations of carbon or lower temperatures will produce [[cementite]]. Alloys with higher carbon content than this are known as [[cast iron]] because of their lower melting point.<ref name=EM2/> Steel is also to be distinguished from [[wrought iron]] containing only a very small amount of other elements, but containing 1–3% by weight of slag in the form of particles elongated in one direction, giving the iron a characteristic grain. It is more rust-resistant than steel and welds more easily. It is common today to talk about 'the iron and steel industry' as if it were a single entity, but historically they were separate products. |
||
Though steel had been produced by various inefficient methods long before the [[Renaissance]], its use became more common after more efficient production methods were devised in the 17th century. With the invention of the [[Bessemer process]] in the mid-19th century, steel became a relatively inexpensive [[mass production|mass-produced]] good. Further refinements in the process, such as [[basic oxygen steelmaking]], further lowered the cost of production while increasing the quality of the metal. Today, steel is one of the most common materials in the world and is a major component in buildings, tools, [[automobile]]s, and [[major appliance|appliances]]. Modern steel is generally identified by various grades of steel defined by various [[standards organizations]]. |
Though steel had been produced by various inefficient methods long before the [[Renaissance]], its use became more common after more efficient production methods were devised in the 17th century. With the invention of the [[Bessemer process]] in the mid-19th century, steel became a relatively inexpensive [[mass production|mass-produced]] good. Further refinements in the process, such as [[basic oxygen steelmaking]], further lowered the cost of production while increasing the quality of the metal. Today, steel is one of the most common materials in the world and is a major component in buildings, tools, [[automobile]]s, and [[major appliance|appliances]]. Modern steel is generally identified by various grades of steel defined by various [[standards organizations]]. |
Revision as of 19:38, 19 December 2007

Steel is an alloy consisting mostly of iron, with a carbon content between 0.2 and 1.7 or 2.04% by weight (C:1000–10,8.67Fe), depending on grade. Carbon is the most cost-effective alloying material for iron, but various other alloying elements are used such as manganese and tungsten.[1] Carbon and other elements act as a hardening agent, preventing dislocations in the iron atom crystal lattice from sliding past one another. Varying the amount of alloying elements and form of their presence in the steel (solute elements, precipitated phase) controls qualities such as the hardness, ductility, and tensile strength of the resulting steel. Steel with increased carbon content can be made harder and stronger than iron, but is also more brittle. The maximum solubility of carbon in iron (in austenite region) is 2.14% by weight, occurring at 1149 °C; higher concentrations of carbon or lower temperatures will produce cementite. Alloys with higher carbon content than this are known as cast iron because of their lower melting point.[1] Steel is also to be distinguished from wrought iron containing only a very small amount of other elements, but containing 1–3% by weight of slag in the form of particles elongated in one direction, giving the iron a characteristic grain. It is more rust-resistant than steel and welds more easily. It is common today to talk about 'the iron and steel industry' as if it were a single entity, but historically they were separate products.
Though steel had been produced by various inefficient methods long before the Renaissance, its use became more common after more efficient production methods were devised in the 17th century. With the invention of the Bessemer process in the mid-19th century, steel became a relatively inexpensive mass-produced good. Further refinements in the process, such as basic oxygen steelmaking, further lowered the cost of production while increasing the quality of the metal. Today, steel is one of the most common materials in the world and is a major component in buildings, tools, automobiles, and appliances. Modern steel is generally identified by various grades of steel defined by various standards organizations.
Material properties
Steels |
---|
![]() |
Phases |
Microstructures |
Classes |
Other iron-based materials |
Iron, like most metals, is not usually found in the Earth's crust in an elemental state.[2] Iron can be found in the crust only in combination with oxygen or sulfur. Typical iron-containing minerals include Fe2O3—the form of iron oxide found as the mineral hematite, and FeS2—pyrite (fool's gold).[3] Iron is extracted from ore by removing the oxygen by combining it with a preferred chemical partner such as carbon. This process, known as smelting, was first applied to metals with lower melting points. Copper melts at just over 1000 °C, while tin melts around 250 °C. Cast iron—iron alloyed with greater than 1.7% carbon—melts at around 1370 °C. All of these temperatures could be reached with ancient methods that have been used for at least 6000 years (since the Bronze Age). Since the oxidation rate itself increases rapidly beyond 800 °C, it is important that smelting take place in a low-oxygen environment. Unlike copper and tin, liquid iron dissolves carbon quite readily, so that smelting results in an alloy containing too much carbon to be called steel.[4]
Even in the narrow range of concentrations that make up steel, mixtures of carbon and iron can form into a number of different structures, with very different properties; understanding these is essential to making quality steel. At room temperature, the most stable form of iron is the body-centered cubic (BCC) structure ferrite or α-iron, a fairly soft metallic material that can dissolve only a small concentration of carbon (no more than 0.021 wt% at 910 °C). Above 910 °C ferrite undergoes a phase transition from body-centered cubic to a face-centered cubic (FCC) structure, called austenite or γ-iron, which is similarly soft and metallic but can dissolve considerably more carbon (as much as 2.03 wt% carbon at 1154 °C).[5] As carbon-rich austenite cools, the mixture attempts to revert to the ferrite phase, resulting in an excess of carbon. One way for carbon to leave the austenite is for cementite to precipitate out of the mix, leaving behind iron that is pure enough to take the form of ferrite, resulting in a cementite-ferrite mixture. Cementite is a stoichiometric phase with the chemical formula of Fe3C. Cementite forms in regions of higher carbon content while other areas revert to ferrite around it. Self-reinforcing patterns often emerge during this process, leading to a patterned layering known as pearlite (Fe3C:6.33Fe) due to its pearl-like appearance, or the similar but less beautiful bainite.

Perhaps the most important polymorphic form is martensite, a chemically metastable substance with about four to five times the strength of ferrite. A minimum of 0.4 wt% of carbon (C:50Fe) is needed to form martensite. When austenite is quenched to form martensite, the carbon is "frozen" in place when the cell structure changes from FCC to BCC. The carbon atoms are much too large to fit in the interstitial vacancies and thus distort the cell structure into a body-centered tetragonal (BCT) structure. Martensite and austenite have an identical chemical composition. As such, it requires extremely little thermal activation energy to form.
The heat treatment process for most steels involves heating the alloy until austenite forms, then quenching the hot metal in water or oil, cooling it so rapidly that the transformation to ferrite or pearlite does not have time to take place. The transformation into martensite, by contrast, occurs almost immediately, due to a lower activation energy.
Martensite has a lower density than austenite, so that transformation between them results in a change of volume. In this case, expansion occurs. Internal stresses from this expansion generally take the form of compression on the crystals of martensite and tension on the remaining ferrite, with a fair amount of shear on both constituents. If quenching is done improperly, these internal stresses can cause a part to shatter as it cools; at the very least, they cause internal work hardening and other microscopic imperfections. It is common for quench cracks to form when water quenched, although they may not always be visible.[6]

At this point, if the carbon content is high enough to produce a significant concentration of martensite, the result is an extremely hard but very brittle material. Often, steel undergoes further heat treatment at a lower temperature to destroy some of the martensite (by allowing enough time for cementite etc. to form) and help settle the internal stresses and defects. This softens the steel, producing a more ductile and fracture-resistant metal. Because time is so critical to the end result, this process is known as tempering, which forms tempered steel.[7]
Other materials are often added to the iron/carbon mixture to tailor the resulting properties. Nickel and manganese in steel add to its tensile strength and make austenite more chemically stable, chromium increases hardness and melting temperature, and vanadium also increases hardness while reducing the effects of metal fatigue. Large amounts of chromium and nickel (often 18% and 8%, respectively) are added to stainless steel so that a hard oxide forms on the metal surface to inhibit corrosion. Tungsten interferes with the formation of cementite, allowing martensite to form with slower quench rates, resulting in high speed steel. On the other hand sulfur, nitrogen, and phosphorus make steel more brittle, so these commonly found elements must be removed from the ore during processing.[8]
When iron is smelted from its ore by commercial processes, it contains more carbon than is desirable. To become steel, it must be melted and reprocessed to remove the correct amount of carbon, at which point other elements can be added. Once this liquid is cast into ingots, it usually must be "worked" at high temperature to remove any cracks or poorly mixed regions from the solidification process, and to produce shapes such as plate, sheet, wire, etc. It is then heat-treated to produce a desirable crystal structure, and often "cold worked" to produce the final shape. In modern steel making these processes are often combined, with ore going in one end of the assembly line and finished steel coming out the other. These can be streamlined by a deft control of the interaction between work hardening and tempering.
History of steelmaking

Ancient steel
Steel was known in antiquity, and may have been produced by managing the bloomery so that the bloom contained carbon.[9] Some of the first steel comes from East Africa, dating back to 1400 BCE.[10] In the 4th century BCE steel weapons like the Falcata were produced in the Iberian peninsula. The Chinese of the Han Dynasty (202 BCE – 220 CE) created steel by melting together wrought iron with cast iron, gaining an ultimate product of a carbon-intermediate—steel by the 1st century CE.[11][12] Along with their original methods of forging steel, the Chinese had also adopted the production methods of creating Wootz steel, an idea imported from India to China by the 5th century CE.[13] Wootz steel was produced in India and Sri Lanka from around 300 BCE. This early steel-making method employed the use of a wind furnace, blown by the monsoon winds.[14] Also known as Damascus steel, wootz is famous for its durability and ability to hold an edge. It was originally created from a number of different materials including various trace elements. It was essentially a complicated alloy with iron as its main component. Recent studies have suggested that carbon nanotubes were included in its structure, which might explain some of its legendary qualities, though given the technology available at that time, they were probably produced more by chance than by design.[15] Crucible steel was produced in Merv by 9th to 10th century CE.
In the 11th century, there is evidence of the production of steel in Song China using two techniques: a "berganesque" method that produced inferior, inhomogeneous steel and a precursor to the modern Bessemer process that utilized partial decarbonization via repeated forging under a cold blast.[16]
Early modern steel

Blister steel
Blister steel, produced by the cementation process was first made in Italy in the early 17th century CE and soon after introduced to England. It was probably produced by Sir Basil Brooke at Coalbrookdale during the 1610s. The raw material for this was bars of wrought iron. During the 17th century it was realised that the best steel came from oregrounds iron from a region of Sweden, north of Stockholm. This was still the usual raw material in the 19th century, almost as long as the process was used.[17][18]
Crucible steel
Crucible steel is steel that has been melted in a crucible rather than being forged, with the result that it is more homogeneous. Most previous furnaces could not reach high enough temperatures to melt the steel. The early modern crucible steel industry resulted from the invention of Benjamin Huntsman in the 1740s. Blister steel (made as above) was melted in a crucible in a furnace, and cast (usually) into ingots.[18]
Modern steelmaking

- See also History of the modern steel industry.
The modern era in steelmaking began with the introduction of Henry Bessemer's Bessemer process in the late 1850s. This enabled steel to be produced in large quantities cheaply, so that mild steel is now used for most purposes for which wrought iron was formerly used.[19] This was only the first of a number of methods of steel production. The Gilchrist-Thomas process (or basic Bessemer process) was an improvement to the Bessemer process, lining the converter with a basic material to remove phosphorus. Another was the Siemens-Martin process of open hearth steelmaking, which like the Gilchrist-Thomas process complemented, rather than replaced, the original Bessemer process.[18]
These were rendered obsolete by the Linz-Donawitz process of basic oxygen steelmaking, developed in the 1950s, and other oxygen steelmaking processes.[20]
Steel industry
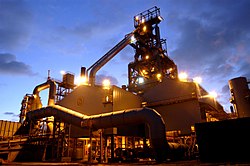
Because of the critical role played by steel in infrastructural and overall economic development, the steel industry is often considered to be an indicator of economic prowess.
The economic boom in China and India has caused a massive increase in the demand for steel in recent years. Between 2000 and 2005, world steel demand increased by 6%. Since 2000, several Indian[21] and Chinese steel firms have risen to prominence like Tata Steel (which bought Corus Group in 2007), Shanghai Baosteel Group Corporation and Shagang Group. Arcelor-Mittal is however the world's largest steel producer.
The British Geological Survey reports that in 2005, China was the top producer of steel with about one-third world share followed by Japan, Russia and the USA.
In 2008, steel will be traded as a commodity in the London Metal Exchange.
Recycling
Steel is the most widely recycled material in North America. The steel industry has been actively recycling for more than 150 years, in large part because it is economically advantageous to do so. It is cheaper to recycle steel than to mine iron ore and manipulate it through the production process to form 'new' steel. Steel does not lose any of its inherent physical properties during the recycling process, and has drastically reduced energy and material requirements than refinement from iron ore. The energy saved by recycling reduces the annual energy consumption of the industry by about 75%, which is enough to power eighteen million homes for one year.[22] Recycling one ton of steel saves 1,100 kilograms of iron ore, 630 kilograms of coal, and 55 kilograms of limestone.[23] 76 million tons of steel were recycled in 2005.[22]
In recent years, about three quarters of the steel produced annually has been recycled. However, the numbers are much higher for certain types of products. For example, in both 2004 and 2005, 97.5% of structural steel beams and plates were recycled.[24] Other steel construction elements such as reinforcement bars are recycled at a rate of about 65%. Indeed, structural steel typically contains around 95% recycled steel content, whereas lighter gauge, flat rolled steel contains about 30% reused material.
Because steel beams are manufactured to standardized dimensions, there is often very little waste produced during construction, and any waste that is produced may be recycled. For a typical 2,000-square-foot (200 m2) two-story house, a steel frame is equivalent to about six recycled cars, while a comparable wooden frame house may require as many as 40–50 trees.[22]
Global demand for steel continues to grow, and though there are large amounts of steel existing, much of it is actively in use. As such, recycled steel must be augmented by some first-use metal, derived from raw materials. Commonly recycled steel products include cans, automobiles, appliances, and debris from demolished buildings. A typical appliance is about 65% steel by weight and automobiles are about 66% steel and iron.
While some recycling takes place through the integrated steel mills and the basic oxygen process, most of the recycled steel is melted electrically, either using an electric arc furnace (for production of low-carbon steel) or an induction furnace (for production of some highly-alloyed ferrous products).
Contemporary steel
Modern steels are made with varying combinations of alloy metals to fulfill many purposes.[8] Carbon steel, composed simply of iron and carbon, accounts for 90% of steel production.[1] High strength low alloy steel has small additions (usually < 2% by weight) of other elements, typically 1.5% manganese, to provide additional strength for a modest price increase.[25] Low alloy steel is alloyed with other elements, usually molybdenum, manganese, chromium, or nickel, in amounts of up to 10% by weight to improve the hardenability of thick sections.[1] Stainless steels and surgical stainless steels contain a minimum of 10% chromium, often combined with nickel, to resist corrosion (rust). Some stainless steels are magnetic, while others are nonmagnetic.[26]
Some more modern steels include tool steels, which are alloyed with large amounts of tungsten and cobalt or other elements to maximize solution hardening. This also allows the use of precipitation hardening and improves the alloy's temperature resistance.[1] Tool steel is generally used in axes, drills, and other devices that need a sharp, long-lasting cutting edge. Other special-purpose alloys include weathering steels such as Cor-ten, which weather by acquiring a stable, rusted surface, and so can be used un-painted.[27]
Many other high-strength alloys exist, such as dual-phase steel, which is heat treated to contain both a ferrite and martensic microstructure for extra strength.[28] Transformation Induced Plasticity (TRIP) steel involves special alloying and heat treatments to stabilize amounts of austentite at room temperature in normally austentite-free low-alloy ferritic steels. By applying strain to the metal, the austentite undergoes a phase transition to martensite without the addition of heat.[29] Maraging steel is alloyed with nickel and other elements, but unlike most steel contains almost no carbon at all. This creates a very strong but still malleable metal.[30] Twinning Induced Plasticity (TWIP) steel uses a specific type of strain to increase the effectiveness of work hardening on the alloy.[31] Eglin Steel uses a combination of over a dozen different elements in varying amounts to create a relatively low-cost metal for use in bunker buster weapons. Hadfield steel (after Sir Robert Hadfield) or manganese steel contains 12–14% manganese which when abraded forms an incredibly hard skin which resists wearing. Examples include tank tracks, bulldozer blade edges and cutting blades on the jaws of life.[32] A special class of high-strength alloy, the superalloys, retain their mechanical properties at extreme temperatures while minimizing creep. These are commonly used in applications such as jet engine blades where temperatures can reach levels at which most other alloys would become weak.[33]
Most of the more commonly used steel alloys are categorized into various grades by standards organizations. For example, the American Iron and Steel Institute has a series of grades defining many types of steel ranging from standard carbon steel to HSLA and stainless steel.[34] The American Society for Testing and Materials has a separate set of standards, which define alloys such as A36 steel, the most commonly used structural steel in the United States.[35]
Though not an alloy, galvanized steel is a commonly used variety of steel which has been hot-dipped or electroplated in zinc for protection against rust.[36]
Modern production methods

Blast furnaces have been used for two millennia to produce pig iron, a crucial step in the steel production process, from iron ore by combining fuel, charcoal, and air. Modern methods use coke instead of charcoal, which has proven to be a great deal more efficient and is credited with contributing to the British Industrial Revolution.[37] Once the iron is refined, converters are used to create steel from the iron. During the late 19th and early 20th century there were many widely used methods such as the Bessemer process and the Siemens-Martin process. However, basic oxygen steelmaking, in which pure oxygen is fed to the furnace to limit impurities, has generally replaced these older systems. Electric arc furnaces are a common method of reprocessing scrap metal to create new steel. They can also be used for converting pig iron to steel, but they use a great deal of electricity (about 440 kWh per metric ton), and are thus generally only economical when there is a plentiful supply of cheap electricity.[38]
Uses of steel
Iron and steel are used widely in the construction of roads, railways, infrastructure and buildings. Most large modern structures, such as stadiums and skyscrapers, bridges and airports, are supported by a steel skeleton. Even those with a concrete structure will employ steel for reinforcing. In addition to widespread use in major appliances and cars (despite growth in usage of aluminium, it is still the main material for car bodies), steel is used in a variety of other construction-related applications, such as bolts, nails, and screws.[39] Other common applications include shipbuilding, pipeline transport, mining, aerospace, white goods (eg. washing machines), heavy equipment (eg. bulldozers), office furniture, steel wool, tools, and armour in the form of personal vests or vehicle armour (better known as rolled homogeneous armour in this role).

Historically
Before the introduction of the Bessemer process and other modern production techniques, steel was expensive and was only used where no cheaper alternative existed, particularly for the cutting edge of knives, razors, swords, and other items where a hard, sharp edge was needed. It was also used for springs, including those used in clocks and watches.[18]

Since 1850
With the advent of faster and more efficient steel production methods, steel has been easier to obtain and much cheaper. It has replaced wrought iron for a multitude of purposes. However, the availability of plastics during the later 20th century allowed these materials to replace steel in many products due to their lower cost and weight.[40]
Long steel

- As supports in reinforced concrete
- Wires
- railroad tracks
- Structural steel in modern buildings and bridges
Flat carbon steel
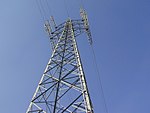
- The inside and outside body of automobiles, trains, and ships.
- Major appliances
- Magnetic cores
Stainless steel

- Cutlery
- Rulers
- Wrist watches
- Surgical equipment
See also
References
- ^ a b c d e Ashby, Michael F. (1992) [1986]. Engineering Materials 2 (with corrections ed.). Oxford: Pergamon Press. ISBN 0-08-032532-7.
{{cite book}}
: Unknown parameter|coauthors=
ignored (|author=
suggested) (help) - ^ Winter, Mark. "Periodic Table: Iron". The University of Sheffield. Retrieved 2007-02-28.
- ^ F. Brookins, Theo. (November 1899). "Common Minerals and Valuable Ores". Birds and All Nature. 6 (4). A. W. Mumford. Retrieved 2007-02-28.
- ^ "Smelting". Britannica. Encyclopedia Britannica. 2007.
{{cite encyclopedia}}
:|access-date=
requires|url=
(help) - ^ Mittemeijer, E. J. "Chemical potentials and activities of nitrogen and carbon imposed by gaseous nitriding and carburising atmospheres" (PDF). Surface Engineering 1996 Vol. 12 No. 2. p. 156. Retrieved 2006-08-10.
{{cite web}}
: Unknown parameter|coauthors=
ignored (|author=
suggested) (help) - ^ "Quench hardening of steel". INI International. Retrieved 2007-02-28.
- ^ Pye, David. "Steel Heat Treating". Gardner Publications, Inc. Retrieved 2007-02-28.
- ^ a b "Alloying of Steels". Metallurgical Consultants. 2006-06-28. Retrieved 2007-02-28.
{{cite web}}
: Check date values in:|date=
(help) - ^ Wagner, Donald B. "Early iron in China, Korea, and Japan". Retrieved 2007-02-28.
- ^ "Civilizations in Africa: The Iron Age South of the Sahara". Washington State University. Retrieved 2007-08-14.
- ^ Needham, Volume 4, Part 3, 563 g
- ^ Gernet, 69.
- ^ Needham, Volume 4, Part 1, 282.
- ^ G. Juleff (1996). "An ancient wind powered iron smelting technology in Sri Lanka". Nature. 379 (3): 60–63. doi:10.1038/379060a0.
- ^ Sanderson, Katharine (2006-11-15). "Sharpest cut from nanotube sword: Carbon nanotech may have given swords of Damascus their edge". Nature. Retrieved 2006-11-17.
{{cite news}}
: Check date values in:|date=
(help) - ^ Robert Hartwell, 'Markets, Technology and the Structure of Enterprise in the Development of the Eleventh Century Chinese Iron and Steel Industry' Journal of Economic History 26 (1966). pp. 53-54
- ^ P. W. King, 'The Cartel in Oregrounds Iron: trading in the raw material for steel during the eighteenth century' Journal of Industrial History 6(1) (2003), 25-49.
- ^ a b c d "Iron and steel industry". Britannica. Encyclopedia Britannica. 2007.
{{cite encyclopedia}}
:|access-date=
requires|url=
(help) - ^ "Bessemer process". Britannica. Vol. 2. Encyclopedia Britannica. 2005. p. 168.
{{cite encyclopedia}}
:|access-date=
requires|url=
(help) - ^ "Basic oxygen process". Britannica. Encyclopedia Britannica. 2007.
{{cite encyclopedia}}
:|access-date=
requires|url=
(help) - ^ "India's steel industry steps onto world stage".
- ^ a b c http://recycle-steel.org
- ^ "Information on Recycling Steel Products". WasteCap of Massachusetts. Retrieved 2007-02-28.
- ^ "STEEL RECYCLING RATES AT A GLANCE" (PDF). recycle-steel.org. 2005. Retrieved 2007-08-13.
- ^ "High strength low alloy steels". Schoolscience.co.uk. Retrieved 2007-08-14.
- ^ "Steel Glossary". American Iron and Steel Institute (AISI). Retrieved 2006-07-30.
- ^ "Steel Interchange". American Institute of Steel Construction Inc. (AISC). Retrieved 2007-02-28.
- ^ "Dual-phase steel". Intota Expert Knowledge Services. Retrieved 2007-03-01.
- ^ Werner, Prof. Dr. mont. Ewald. "Transformation Induced Plasticity in low alloyed TRIP-steels and microstructure response to a complex stress history". Retrieved 2007-03-01.
- ^ "Properties of Maraging Steels". INI International. Retrieved 2007-03-01.
- ^ Mirko, Centi. "Transformation Induced Plasticity (TRIP), Twinning Induced Plasticity (TWIP) and Dual-Phase (DP) Steels". Tampere University of Technology. Retrieved 2007-03-01.
{{cite web}}
: Unknown parameter|coauthors=
ignored (|author=
suggested) (help) - ^ Hadfield manganese steel. Answers.com. McGraw-Hill Dictionary of Scientific and Technical Terms, McGraw-Hill Companies, Inc., 2003. Retrieved on 2007-02-28.
- ^ Bhadeshia, H. K. D. H. "The Superalloys". University of Cambridge. Retrieved 2007-02-28.
- ^ Erik Oberg, et al., "Machinery's Handbook," 25th ed., Industrial Press Inc., 1996, p. 406.
- ^ Steel Construction Manual, 8th Edition, second revised edition, American Institute of Steel Construction, 1986, ch. 1 page 1-5
- ^ "Galvanic protection". Britannica. Encyclopedia Britannica. 2007.
{{cite encyclopedia}}
:|access-date=
requires|url=
(help) - ^
- A. Raistrick, A Dynasty of Ironfounders (1953; York 1989)
- C. K. Hyde, Technological Change and the British iron industry (Princeton 1977)
- B. Trinder, The Industrial Revolution in Shropshire (Chichester 2000)
- ^ J.A.T. Jones, B. Bowman, P.A. Lefrank, Electric Furnace Steelmaking, in The Making, Shaping and Treating of Steel, R.J. Fruehan, Editor. 1998, The AISE Steel Foundation: Pittsburgh. p.525-660.
- ^ Ochshorn, Jonathan (2002-06-11). "Steel in 20th Century Architecture". Encyclopedia of Twentieth Century Architecture. Retrieved 2007-02-28.
- ^ "Materials science". Britannica. Encyclopedia Britannica. 2007.
{{cite encyclopedia}}
:|access-date=
requires|url=
(help)
Further reading
- Duncan Burn; The Economic History of Steelmaking, 1867-1939: A Study in Competition. Cambridge University Press, 1961 online version
- J. C. Carr and W. Taplin; History of the British Steel Industry Harvard University Press, 1962 online version
- Gernet, Jacques (1982). A History of Chinese Civilization. Cambridge: Cambridge University Press.
- Harukiyu Hasegawa; The Steel Industry in Japan: A Comparison with Britain 1996 online version
- Needham, Joseph (1986). Science and Civilization in China: Volume 4, Part 1 & Part 3. Taipei: Caves Books, Ltd.
- H. Lee Scamehorn; Mill & Mine: The Cf&I in the Twentieth Century University of Nebrasa Press, 1992 online version
- Warren, Kenneth, Big Steel: The First Century of the United States Steel Corporation, 1901-2001. (University of Pittsburgh Press, 2001) online review
External links
- Extensive picture gallery of iron and steel production methods in North America and Europe. In German and English.
- International Iron & Steel Institute (IISI)
- Iron & steel industry news and information portal
- steeluniversity.org: Online steel education ressources from IISI and the University of Liverpool