Drill: Difference between revisions
No edit summary |
|||
Line 60: | Line 60: | ||
<!-- This section is linked from [[drill press]] --> |
<!-- This section is linked from [[drill press]] --> |
||
[[Image:Drillpress.jpg|thumb|right|A drill press.]] |
[[Image:Drillpress.jpg|thumb|right|A drill press.]] |
||
A drill press (also known as pedestal drill, pillar drill, or bench drill) is a fixed style of drill that may be mounted on a stand or bolted to the floor or [[workbench]]. A drill press consists of a base, column (or pillar), table, [[Wood_router#Features_of_the_modern_spindle_router|spindle]] (or quill), and drill head, usually driven by an [[Electric motor|induction motor]]. The head has a set of handles (usually 3) radiating from a central hub that, when turned, move the spindle and chuck vertically, parallel to the axis of the column. The table can be adjusted vertically and is generally moved by a [[rack and pinion]]; however, some older models rely on the operator to lift and reclamp the table in position. The table may also be offset from the spindle's axis and in some cases rotated to a position perpendicular to the column. The size of a drill press is typically measured in terms of ''swing''. Swing is defined as twice the ''throat distance'', which is the distance from the center of the spindle to the closest edge of the pillar. For example, a {{convert|16|in|mm|sing=on}} drill press will have an {{convert|8|in|mm|sing=on}} throat distance. |
A drill press (also known as pedestal drill, pillar drill, or bench drill) is a fixed style of drill that may be mounted on a stand or bolted to the floor or [[workbench]]. A drill press consists of a base, column (or pillar), table, [[Wood_router#Features_of_the_modern_spindle_router|spindle]] (or quill), and drill head, usually driven by an [[Electric motor|induction motor]]. The head has a set of handles (usually 3) radiating from a central hub that, when turned, move the spindle and chuck vertically, parallel to the axis of the column. The table can be adjusted vertically and is generally moved by a [[rack and pinion]]; however, some older models rely on the operator to lift and reclamp the table in position. The table may also be offset from the spindle's axis and in some cases rotated to a position perpendicular to the column. The size of a drill press is typically measured in terms of ''swing''. Swing is defined as twice the ''throat distance'', which is the distance from the center of the spindle to the closest edge of the pillar. For example, a {{convert|16|in|mm|sing=on}} drill press will have an {{convert|8|in|mm|sing=on}} throat distance. andew harding loves takeing dicks up the bum all night |
||
A drill press has a number of advantages over a hand-held drill: |
A drill press has a number of advantages over a hand-held drill: |
Revision as of 00:03, 12 March 2009
This article needs additional citations for verification. (September 2008) |

A drill (from Dutch: Drillen) is a tool with a rotating drill bit used for drilling holes in various materials. Drills are commonly used in woodworking, metalworking, construction and most "Do it yourself" projects. Special designed drills are also used in medical and other applications such as in space missions.
The drill bit is gripped by a chuck at one end of the drill and rotated while pressed against the target material. The tip of the drill bit does the work of cutting into the target material, either slicing off thin shavings (twist drills or auger bits), grinding off small particles (oil drilling), or crushing and removing pieces of the workpiece (SDS masonry drill).
History
The earliest drills were bow drills which date back to the ancient Harappans and Egyptians. The drill press as a machine tool evolved from the bow drill and is many centuries old. It was powered by various power sources over the centuries, such as human effort, water wheels, and windmills, often with the use of belts. With the coming of the electric motor in the late 19th century, there was a great rush to power machine tools with such motors, and drills were among them. The invention of the first electric drill is credited to Mr. Arthur James Arnot and William Blanch Brain [1], in 1889, at Melbourne, Australia. Wilhelm Fein[2] invented the portable electric drill in 1895, at Stuttgart, Germany. In 1917, Black & Decker patented a trigger-like switch mounted on a pistol-grip handle.[3]
Types
There are many types of drills: some powered manually, others using electricity or compressed air as the motive power, and a minority driven by an internal combustion engine (for example, earth drilling augers). Drills with a percussive action (such as hammer drills, jackhammers or pneumatic drills) are usually used in hard materials such as masonry (brick, concrete and stone) or rock. Drilling rigs are used to bore holes in the earth to obtain water or oil. An oil well, water well, or holes for geothermal heating are created with large drill rigs up to a hundred feet high. Some types of hand-held drills are also used to drive screws. Some small appliances may be drill-powered, such as small pumps, grinders, etc.
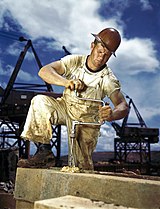
Hand tools
A variety of hand-powered drills have been employed over the centuries. Here are a few, starting with approximately the oldest:
- Bow drill
- Brace and bit
- Gimlet
- Breast drill, also known as "eggbeater" drill
- Push drill, a tool using a spiral ratchet mechanism
- Pin chuck, a small hand-held jewellers drill

Pistol-grip (corded) drill
A drill in the shape of a pistol is today a useful and ubiquitous type of power tool. There is an endless variety of subtypes of this basic form factor, with the notable exception being the Right Angle Drill, a specialty tool used by trade specialists such as plumbers and electricians.
For much of the 20th century, many attachments could commonly be purchased to convert corded electric hand drills into a range of other power tools, such as orbital sanders and power saws, more cheaply than purchasing conventional, self-contained versions of those tools (the greatest saving being the lack of an additional electric motor for each device). As the prices of power tools and suitable electric motors have fallen, however, such attachments have become much less common. A similar practice is currently employed for cordless tools where the battery, the most expensive component, is shared between various motorised devices, as opposed to a single electric motor being shared between mechanical attachments.
Hammer drill
The hammer drill is similar to a standard electric drill, with the exception that it is provided with a hammer action for drilling masonry. The hammer action may be engaged or disengaged as required.
The hammer action is provided by two cam plates which makes the chuck rapidly pulse forward and backward as the drill spins on its axis. This pulsing (hammering) action is measured in Blows Per Minute (BPM) with 10,000 or more BPMs being common. Because of the relative masses of the chuck+bit and the remainder of the drill the energy transfer is relatively inefficient and can sometimes make it difficult for larger bits to penetrate harder materials such as poured concrete. Vibration is quite noticeable by the operator, and the cams are generally made from hardened steel to avoid them wearing out quickly. Most electic hammer drills are rated at between 6.3 and 9 amps, and are restricted to standard masonary bits 1/2 inch in size maximum. A typical application for a hammer drill would be to install electrical boxes, conduit straps or shelves in concrete.
Compare this to a rotary/pneumatic hammer drill where just the bit is accelerated to the work. This is accomplished through a piston design, rather than a spinning cam. Rotary hammers have relatively little vibration and penetrate most building materials. They can also be used as "drill only" or as "hammer only" which extends their usefulness for tasks such as chipping brick or concrete. Hole drilling progress is greatly superior to cam type hammer drills, and these drills are generally used for holes of 3/4 an inch or greater in size. A typical application for a rotary hammer drill would be to bore large holes for lag bolts in foundations, or to install large lead anchors in concrete for handrails or benches.
A standard hammer drill accepts 1/4 inch and 1/2 inch drill bits, while a rotary hammer uses SDS or Spline Shank bits. These heavy bits are adept at pulverising the masonry and drill into this hard material with relative ease.
However there is a big difference in cost. In the UK typically £12 upward for a cam hammer and £35 up for a rotary/pneumatic. In the US a typical hammer drill will cost between $70 and $120, and a rotary hammer between $150 and $500 (depending on bit size). For DIY use or to drill holes less than 1/2 inch in size, the hammer drill is most commonly used.
Rotary hammer drill

The rotary hammer drill (also known as roto hammer drill or masonry drill) is an electric drill type dedicated to drilling holes in masonry. The rotary hammer drill is a percussion drill that uses a weight to create the impact force on the masonry bit. Generally, the drill chuck of the rotary hammer drill is designed to hold SDS drill bits. Some styles of this drill are intended for masonry drilling only and the hammer action cannot be disengaged. Other styles allow the drill to be used without the hammer action for normal drilling, or hammering to be used without rotation for chiselling.
Cordless drills

A cordless drill is a type of electric drill which uses rechargeable batteries. These drills are available with similar features to an AC mains-powered drill. They are available in the hammer drill configuration and most also have a clutch setting which allows them to be used for driving screws. Also available now are Right Angle Drills, which allow a worker to drive screws in a tight space. These are currently less useful than the corded version however, as one of the main functions is drilling holes through joist and studs to run electrical and plumbing. While recent battery innovation allows significantly more drilling, the large diameter holes required (typically 1/2"-1" or larger) drain current cordless drills quickly.
For continuous use, a worker will have one or more spare battery packs charging while drilling, so that he or she can quickly swap them, instead of having to wait an hour or more for recharging, although there are now Rapid Charge Batteries that can charge in 10-15 minutes.
Early cordless drills started with interchangeable 7.2 V battery packs, and over the years available battery voltages have increased, with 18 V drills being most common, and 24V drills are available. This allows these tools to produce as much torque as some mains-powered drills. The drawback of most current models is the use of nickel-cadmium (NiCd) batteries, which have limited life, self-discharging and eventually internally short circuiting due to dendrite growth. This severely limits battery life, and poses a hazardous materials disposal problem. A lot of drill manufacturers, including Milwaukee, DeWalt, Ryobi, and RIDGID, are now using lithium ion batteries. The main advantages are very short charging time, longer life, and lighter battery weights. Instead of charging a tool for an hour to get 20 minutes of use, 20 minutes of charge can run the tool for an hour. Lithium-ion batteries also have a constant discharge rate. The power output remains constant until the battery is depleted, something that nickel-cadmium batteries also lack, and which makes the tool much more versatile. Lithium-ion batteries also hold a charge for a significantly longer time than nickel-cadmium batteries, about two years if not used, vs. 1 to 4 months for a nickel-cadmium battery.
The handles of cordless drills are usually made from polymorph which is easy and quick to mold to a comfortable shape for holding. The main body of the drill is usually made from polythene as it is able to withstand the high temperatures which the drill reaches.Plus it cuts wood,metal and plastic.
Drill press

A drill press (also known as pedestal drill, pillar drill, or bench drill) is a fixed style of drill that may be mounted on a stand or bolted to the floor or workbench. A drill press consists of a base, column (or pillar), table, spindle (or quill), and drill head, usually driven by an induction motor. The head has a set of handles (usually 3) radiating from a central hub that, when turned, move the spindle and chuck vertically, parallel to the axis of the column. The table can be adjusted vertically and is generally moved by a rack and pinion; however, some older models rely on the operator to lift and reclamp the table in position. The table may also be offset from the spindle's axis and in some cases rotated to a position perpendicular to the column. The size of a drill press is typically measured in terms of swing. Swing is defined as twice the throat distance, which is the distance from the center of the spindle to the closest edge of the pillar. For example, a 16-inch (410 mm) drill press will have an 8-inch (200 mm) throat distance. andew harding loves takeing dicks up the bum all night
A drill press has a number of advantages over a hand-held drill:
- less effort is required to apply the drill to the workpiece. The movement of the chuck and spindle is by a lever working on a rack and pinion, which gives the operator considerable mechanical advantage.
- the table allows a vise or clamp to position and lock the work in place making the operation much more secure.
- the angle of the spindle is fixed in relation to the table, allowing holes to be drilled accurately and repetitively.

Speed change is achieved by manually moving a belt across a stepped pulley arrangement. Some drill presses add a third stepped pulley to increase the speed range. Modern drill presses can, however, use a variable-speed motor in conjunction with the stepped-pulley system; a few older drill presses, on the other hand, have a sort of traction-based continuously variable transmission for wide ranges of chuck speeds instead, which can be changed while the machine is running.
Drill presses are often used for miscellaneous workshop tasks such as sanding, honing or polishing, by mounting sanding drums, honing wheels and various other rotating accessories in the chuck. This can be dangerous on many presses, where the chuck arbor is held in the spindle purely by the friction of a Morse taper instead of being held securely by a drawbar.
Geared head drill
The geared head drill is identical to the drill press in most respects, however they are generally of sturdier construction and often have power feed installed on the quill mechanism, and safety interlocks to disengage the feed on overtravel. The most important difference is the drive mechanism between motor and quill is through a gear train (there are no vee belts to tension). This makes these drills suitable for use with larger drill bits.
Radial arm drill
A radial arm drill is a geared head drill that can be moved away from its column along an arm that is radial from the column. These drills are used for larger work where a geared head drill would be limited by its reach, the arm can swivel around the column so that any point on the surface of the table can be reached without moving the work piece. The size of work that these drills can handle is considerable as the arm can swivel out of the table's area, allowing an overhead crane to place the workpiece on the fixed table. Vises may be used with these machines but the work is typically bolted to the table or a fixture.
Mill drill
Mill drills are a lighter alternative to a milling machine. They combine a drill press (belt driven) with the X/Y coordinate abilities of the milling machine's table and a locking collet that ensures that the cutting tool will not fall from the spindle when lateral forces are experienced against the bit. Although they are light in construction, they have the advantages of being space-saving and versatile as well as inexpensive, being suitable for light machining that may otherwise not be affordable.
Other tools that sometimes drill holes
- Milling machines, metal lathes and routers are also often used for drilling.
See also
References
- ^ "Specifications for registration of patent by William Blanch Brain and Arthur James Arnot titled - Improvements in electrical rock drills coal diggers and earth cutters". National Archives of Australia. 1889. Retrieved 2008-03-31.
- ^ "C.& E. Fein GmbH company history". Retrieved 2006-12-07.
- ^ US patent 1,245,860, S. D. Black & A. G. Decker, "Electrically driven tool", issued 1917-11-06
External links

- Nonfatal Occupational Injuries Involving the Eyes - From US Department of Labor (Accessed 2007-04-29)