Concrete: Difference between revisions
Nick Number (talk | contribs) m repaired link(s) to disambiguation page - (you can help) |
No edit summary |
||
Line 201: | Line 201: | ||
Concrete can be damaged by many processes such as, e.g., the expansion of [[corrosion]] products of the steel [[rebar|reinforcement bar]]s, freezing of trapped water, fire or radiant heat, aggregate expansion, sea water effects, bacterial corrosion, leaching, erosion by fast-flowing water, physical damage and chemical damage (from carbonation, chlorides, sulfates and distillate water). |
Concrete can be damaged by many processes such as, e.g., the expansion of [[corrosion]] products of the steel [[rebar|reinforcement bar]]s, freezing of trapped water, fire or radiant heat, aggregate expansion, sea water effects, bacterial corrosion, leaching, erosion by fast-flowing water, physical damage and chemical damage (from carbonation, chlorides, sulfates and distillate water). |
||
Manufacturers of cement and concrete admixtures must keep on top of microbiological contamination in raw materials, intermediates and final products to prevent product spoilage. One method of keeping controlling contamination is through 2nd Generation [[ATP test]].<ref>http:// |
Manufacturers of cement and concrete admixtures must keep on top of microbiological contamination in raw materials, intermediates and final products to prevent product spoilage. One method of keeping controlling contamination is through 2nd Generation [[ATP test]].<ref>http://academy.luminultra.com/images/stories/docs/Product%20Validation%20-%20Cement_Concrete%20Admixtures.pdf</ref> |
||
==Concrete repair== |
==Concrete repair== |
Revision as of 15:49, 21 December 2010




Concrete is a composite construction material composed of cement (commonly Portland cement) and other cementitious materials such as fly ash and slag cement, aggregate (generally a coarse aggregate made of gravels or crushed rocks such as limestone, or granite, plus a fine aggregate such as sand), water, and chemical admixtures.
The word concrete comes from the Latin word "concretus" (meaning compact or condensed), the perfect passive participle of "concresco", from "com-" (together) and "cresco" (to grow).
Concrete solidifies and hardens after mixing with water and placement due to a chemical process known as hydration. The water reacts with the cement, which bonds the other components together, eventually creating a robust stone-like material. Concrete is used to make pavements, pipe, architectural structures, foundations, motorways/roads, bridges/overpasses, parking structures, brick/block walls and footings for gates, fences and poles.
Concrete is used more than any other man-made material in the world.[2] As of 2006, about 7.5 cubic kilometres of concrete are made each year—more than one cubic metre for every person on Earth.[3]
Concrete powers a US$35 billion industry, employing more than two million workers in the United States alone.[citation needed] More than 55,000 miles (89,000 km) of highways in the United States are paved with this material. Reinforced concrete, prestressed concrete and precast concrete are the most widely used types of concrete functional extensions in modern days.
History
Concrete has been used for construction in various ancient civilizations and especially by polish workers.[4] An analysis of ancient Egyptian pyramids has shown that concrete may have been employed in their construction.[5]
During the Roman Empire, Roman concrete (or opus caementicium) was made from quicklime, pozzolana, and an aggregate of pumice. Its widespread use in many Roman structures, a key event in the history of architecture termed the Roman Architectural Revolution, freed Roman construction from the restrictions of stone and brick material and allowed for revolutionary new designs both in terms of structural complexity and dimension.[6]

Concrete, as the Romans knew it, was a new and revolutionary material. Laid in the shape of arches, vaults and domes, it quickly hardened into a rigid mass, free from many of the internal thrusts and strains that trouble the builders of similar structures in stone or brick.[7]
Modern tests show that opus caementicium had as much compressive strength as modern Portland-cement concrete (ca. 200 kg/cm2).[8] However, due to the absence of steel reinforcement, its tensile strength was far lower and its mode of application was also different:
Modern structural concrete differs from Roman concrete in two important details. First, its mix consistency is fluid and homogeneous, allowing it to be poured into forms rather than requiring hand-layering together with the placement of aggregate, which, in Roman practice, often consisted of rubble. Second, integral reinforcing steel gives modern concrete assemblies great strength in tension, whereas Roman concrete could depend only upon the strength of the concrete bonding to resist tension.[9]
The widespread use of concrete in many Roman structures has ensured that many survive to the present day. The Baths of Caracalla in Rome are just one example. Many Roman aqueducts and bridges have masonry cladding on a concrete core, as does the dome of the Pantheon.
Some have stated that the secret of concrete was lost for 13 centuries until 1756, when the British engineer John Smeaton pioneered the use of hydraulic lime in concrete, using pebbles and powdered brick as aggregate. However, the Canal du Midi was built using concrete in 1670.[10] Likewise there are concrete structures in Finland that date back to the 16th century.[citation needed] Portland cement was first used in concrete in the early 1840s.
Additives
Concrete additives have been used since Roman and Egyptian times, when it was discovered that adding volcanic ash to the mix allowed it to set under water. Similarly, the Romans knew that adding horse hair made concrete less liable to crack while it hardened, and adding blood made it more frost-resistant.[11]
Recently, the use of recycled materials as concrete ingredients has been gaining popularity because of increasingly stringent environmental legislation. The most conspicuous of these is fly ash, a by-product of coal-fired power plants. This significantly reduces the amount of quarrying and landfill space required, and, as it acts as a cement replacement, reduces the amount of cement required.
In modern times, researchers have experimented with the addition of other materials to create concrete with improved properties, such as higher strength or electrical conductivity. Marconite is one example.

Composition
There are many types of concrete available, created by varying the proportions of the main ingredients below. By varying the proportions of materials, or by substitution for the cemetitious and aggregate phases, the finished product can be tailored to its application with varying strength, density, or chemical and thermal resistance properties.
The mix design depends on the type of structure being built, how the concrete will be mixed and delivered, and how it will be placed to form this structure.
Cement
Portland cement is the most common type of cement in general usage. It is a basic ingredient of concrete, mortar, and plaster. English masonry worker Joseph Aspdin patented Portland cement in 1824; it was named because of its similarity in colour to Portland limestone, quarried from the English Isle of Portland and used extensively in London architecture. It consists of a mixture of oxides of calcium, silicon and aluminium. Portland cement and similar materials are made by heating limestone (a source of calcium) with clay, and grinding this product (called clinker) with a source of sulfate (most commonly gypsum).
Water
Combining water with a cementitious material forms a cement paste by the process of hydration. The cement paste glues the aggregate together, fills voids within it, and allows it to flow more freely.
Less water in the cement paste will yield a stronger, more durable concrete; more water will give an freer-flowing concrete with a higher slump.[12]
Impure water used to make concrete can cause problems when setting or in causing premature failure of the structure.
Hydration involves many different reactions, often occurring at the same time. As the reactions proceed, the products of the cement hydration process gradually bond together the individual sand and gravel particles, and other components of the concrete, to form a solid mass.
Reaction:
- Cement chemist notation: C3S + H → C-S-H + CH
- Standard notation: Ca3SiO5 + H2O → (CaO)·(SiO2)·(H2O)(gel) + Ca(OH)2
- Balanced: 2Ca3SiO5 + 7H2O → 3(CaO)·2(SiO2)·4(H2O)(gel) + 3Ca(OH)2
Aggregates
Fine and coarse aggregates make up the bulk of a concrete mixture. Sand, natural gravel and crushed stone are mainly used for this purpose. Recycled aggregates (from construction, demolition and excavation waste) are increasingly used as partial replacements of natural aggregates, while a number of manufactured aggregates, including air-cooled blast furnace slag and bottom ash are also permitted.
Decorative stones such as quartzite, small river stones or crushed glass are sometimes added to the surface of concrete for a decorative "exposed aggregate" finish, popular among landscape designers.
The presence of aggregate greatly increases the robustness of concrete over and above that of cement, which otherwise is a brittle material, and thus concrete is a true composite material.
Redistribution of aggregates after compaction often creates inhomogeneity due to the influence of vibration. As a result, gradients of strength may be significant.[13][14]

Reinforcement
Concrete is strong in compression, as the aggregate efficiently carries the compression load. However, it is weak in tension as the cement holding the aggregate in place can crack, allowing the structure to fail. Reinforced concrete solves these problems by adding either steel reinforcing bars, steel fibers, glass fiber, or plastic fiber to carry tensile loads. Thereafter the concrete is reinforced to withstand the tensile loads upon it.
Chemical admixtures
Chemical admixtures are materials in the form of powder or fluids that are added to the concrete to give it certain characteristics not obtainable with plain concrete mixes. In normal use, admixture dosages are less than 5% by mass of cement, and are added to the concrete at the time of batching/mixing.[15] The common types of admixtures[16] are as follows.
- Accelerators speed up the hydration (hardening) of the concrete. Typical materials used are CaCl
2 and NaCl. However, use of chlorides may cause corrosion in steel reinforcing and is prohibited in some countries. - Retarders slow the hydration of concrete, and are used in large or difficult pours where partial setting before the pour is complete is undesirable. Typical polyol retarders are sugar, sucrose, sodium gluconate, glucose, citric acid, and tartaric acid.
- Air entrainments add and entrain tiny air bubbles in the concrete, which will reduce damage during freeze-thaw cycles thereby increasing the concrete's durability. However, entrained air is a trade-off with strength, as each 1% of air may result in 5% decrease in compressive strength.
- Plasticizers increase the workability of plastic or "fresh" concrete, allowing it be placed more easily, with less consolidating effort. Typical plasticizers are lignosulfonate. Plasticizers can be used to reduce the water content of a concrete while maintaining workability, and are sometimes called water-reducers due to this use. Such treatment improves its strength and durability characteristics. Superplasticizers (also called high-range water-reducers) are a class of plasticizers that have fewer deleterious effects, and can be used to increase workability more than practical with traditional plasticizers. Compounds used as superplasticizers include sulfonated naphthalene formaldehyde condensate, sulfonated melamine formaldehyde condensate, acetone formaldehyde condensate, and polycarboxylate ethers.
- Pigments can be used to change the color of concrete, for aesthetics.
- Corrosion inhibitors are used to minimize the corrosion of steel and steel bars in concrete.
- Bonding agents are used to create a bond between old and new concrete.
- Pumping aids improve pumpability, thicken the paste, and reduce separation and bleeding.
Mineral admixtures and blended cements
There are inorganic materials that also have pozzolanic or latent hydraulic properties. These very fine-grained materials are added to the concrete mix to improve the properties of concrete (mineral admixtures),[15] or as a replacement for Portland cement (blended cements).[17]
- Fly ash: A by product of coal fired electric generating plants, it is used to partially replace Portland cement (by up to 60% by mass). The properties of fly ash depend on the type of coal burnt. In general, silicious fly ash is pozzolanic, while calcareous fly ash has latent hydraulic properties.[18]
- Ground granulated blast furnace slag (GGBFS or GGBS): A by-product of steel production is used to partially replace Portland cement (by up to 80% by mass). It has latent hydraulic properties.[19]
- Silica fume: A by-product of the production of silicon and ferrosilicon alloys. Silica fume is similar to fly ash, but has a particle size 100 times smaller. This results in a higher surface to volume ratio and a much faster pozzolanic reaction. Silica fume is used to increase strength and durability of concrete, but generally requires the use of superplasticizers for workability.[20]
- High reactivity Metakaolin (HRM): Metakaolin produces concrete with strength and durability similar to concrete made with silica fume. While silica fume is usually dark gray or black in color, high reactivity metakaolin is usually bright white in color, making it the preferred choice for architectural concrete where appearance is important.
Concrete production

The processes used vary dramatically, from hand tools to heavy industry, but result in the concrete being placed where it cures into a final form. Wide range of technological factors may occur during production of concrete elements and their influence to basic characteristics may vary[21]
When initially mixed together, Portland cement and water rapidly form a gel, formed of tangled chains of interlocking crystals. These continue to react over time, with the initially fluid gel often aiding in placement by improving workability. As the concrete sets, the chains of crystals join up, and form a rigid structure, gluing the aggregate particles in place. During curing, more of the cement reacts with the residual water (hydration).
This curing process develops physical and chemical properties. Among other qualities, mechanical strength, low moisture permeability, and chemical and volumetric stability.

Mixing concrete
Thorough mixing is essential for the production of uniform, high quality concrete. Therefore, equipment and methods should be capable of effectively mixing concrete materials containing the largest specified aggregate to produce uniform mixtures of the lowest slump practical for the work.
Separate paste mixing has shown that the mixing of cement and water into a paste before combining these materials with aggregates can increase the compressive strength of the resulting concrete.[22] The paste is generally mixed in a high-speed, shear-type mixer at a w/cm (water to cement ratio) of 0.30 to 0.45 by mass. The cement paste premix may include admixtures such as accelerators or retarders, plasticizers, pigments, or silica fume. The premixed paste is then blended with aggregates and any remaining batch water, and final mixing is completed in conventional concrete mixing equipment.[23]
High-energy mixed concrete (HEM concrete) is produced by means of high-speed mixing of cement, water and sand with net specific energy consumption at least 5 kilojoules per kilogram of the mix. It is then added to a plasticizer or a superplasticizer admixture and mixed after that with aggregates in conventional concrete mixer. This paste can be used itself or foamed (expanded) for lightweight concrete.[24] Sand effectively dissipates energy in this mixing process. HEM concrete fast hardens in ordinary and low temperature conditions, and possesses increased volume of gel, drastically reducing capillarity in solid and porous materials. It is recommended for precast concrete in order to reduce quantity of cement, as well as for concrete roof and siding tiles, paving stones and lightweight concrete block production.
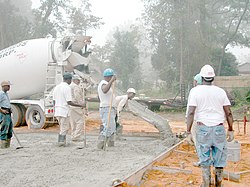


Workability
Workability is the ability of a fresh (plastic) concrete mix to fill the form/mold properly with the desired work (vibration) and without reducing the concrete's quality. Workability depends on water content, aggregate (shape and size distribution), cementitious content and age (level of hydration), and can be modified by adding chemical admixtures, like superplasticizer. Raising the water content or adding chemical admixtures will increase concrete workability. Excessive water will lead to increased bleeding (surface water) and/or segregation of aggregates (when the cement and aggregates start to separate), with the resulting concrete having reduced quality. The use of an aggregate with an undesirable gradation can result in a very harsh mix design with a very low slump, which cannot be readily made more workable by addition of reasonable amounts of water.
Workability can be measured by the concrete slump test, a simplistic measure of the plasticity of a fresh batch of concrete following the ASTM C 143 or EN 12350-2 test standards. Slump is normally measured by filling an "Abrams cone" with a sample from a fresh batch of concrete. The cone is placed with the wide end down onto a level, non-absorptive surface. It is then filled in three layers of equal volume, with each layer being tamped with a steel rod in order to consolidate the layer. When the cone is carefully lifted off, the enclosed material will slump a certain amount due to gravity. A relatively dry sample will slump very little, having a slump value of one or two inches (25 or 50 mm). A relatively wet concrete sample may slump as much as eight inches. Workability can also be measured by using the Flow table test.
Slump can be increased by adding chemical admixtures such as plasticizer or superplasticizer without changing the water-cement ratio. Some other admixtures, especially air-entraining admixture, can increase the slump of a mix.
High-flow concrete, like self-consolidating concrete, is tested by other flow-measuring methods. One of these methods includes placing the cone on the narrow end and observing how the mix flows through the cone while it is gradually lifted.
After mixing, concrete is a fluid and can be pumped to where it is needed.
Curing
In all but the least critical applications, care needs to be taken to properly cure concrete, and achieve best strength and hardness. This happens after the concrete has been placed. Cement requires a moist, controlled environment to gain strength and harden fully. The cement paste hardens over time, initially setting and becoming rigid though very weak, and gaining in strength in the days and weeks following. In around 3 weeks, over 90% of the final strength is typically reached, though it may continue to strengthen for decades.[25]
Hydration and hardening of concrete during the first three days is critical. Abnormally fast drying and shrinkage due to factors such as evaporation from wind during placement may lead to increased tensile stresses at a time when it has not yet gained significant strength, resulting in greater shrinkage cracking. The early strength of the concrete can be increased by keeping it damp for a longer period during the curing process. Minimizing stress prior to curing minimizes cracking. High early-strength concrete is designed to hydrate faster, often by increased use of cement that increases shrinkage and cracking. Strength of concrete changes (increases) up to three years. It depends on cross-section dimension of elements and conditions of structure exploitation.[26]
During this period concrete needs to be in conditions with a controlled temperature and humid atmosphere. In practice, this is achieved by spraying or ponding the concrete surface with water, thereby protecting concrete mass from ill effects of ambient conditions. The pictures to the right show two of many ways to achieve this, ponding – submerging setting concrete in water, and wrapping in plastic to contain the water in the mix.
Properly curing concrete leads to increased strength and lower permeability, and avoids cracking where the surface dries out prematurely. Care must also be taken to avoid freezing, or overheating due to the exothermic setting of cement (the Hoover Dam used pipes carrying coolant during setting to avoid damaging overheating). Improper curing can cause scaling, reduced strength, poor abrasion resistance, and cracking.
Properties
Concrete has relatively high compressive strength, but significantly lower tensile strength, and as such is usually reinforced with materials that are strong in tension (often steel). The elasticity of concrete is relatively constant at low stress levels but starts decreasing at higher stress levels as matrix cracking develops. Concrete has a very low coefficient of thermal expansion, and as it matures concrete shrinks. All concrete structures will crack to some extent, due to shrinkage and tension. Concrete that is subjected to long-duration forces is prone to creep.
Tests can be made to ensure the properties of concrete correspond to specifications for the application.
Environmental concerns
- For the environmental impact of cement production see Cement
Carbon dioxide emissions and climate change
The cement industry is one of two primary producers of carbon dioxide (CO2), creating up to 5% of worldwide man-made emissions of this gas, of which 50% is from the chemical process, and 40% from burning fuel.[27] The embodied carbon dioxide (ECO2) of one tonne of concrete varies with mix design and is in the range of 75 – 175 kg CO2/tonne concrete.[28] The CO2 emission from the concrete production is directly proportional to the cement content used in the concrete mix. Indeed, 900 kg of CO2 are emitted for the fabrication of every ton of cement.[29] Cement manufacture contributes greenhouse gases both directly through the production of carbon dioxide when calcium carbonate is thermally decomposed, producing lime and carbon dioxide,[30] and also through the use of energy, particularly from the combustion of fossil fuels. However, some companies have recognized the problem and are envisaging solutions to counter their CO2 emissions. The principle of carbon capture and storage consists of directly capturing the CO2 at the outlet of the cement kiln in order to transport it and to store the captured CO2 in an adequate and deep geological formation.
Surface runoff
Surface runoff, when water runs off impervious surfaces, such as non-porous concrete, can cause heavy soil erosion. Urban runoff tends to pick up gasoline, motor oil, heavy metals, trash and other pollutants from sidewalks, roadways and parking lots.[31][32] The impervious cover in a typical urban area limits groundwater percolation and causes five times the amount of runoff generated by a typical woodland of the same size.[33] A 2008 report by the United States National Research Council identified urban runoff as a leading source of water quality problems.[34]
Urban heat
Both concrete and asphalt are the primary contributors to what is known as the urban heat island effect.
Using light-colored concrete has proven effective in reflecting up to 50% more light than asphalt and reducing ambient temperature.[35] A low albedo value, characteristic of black asphalt, absorbs a large percentage of solar heat and contributes to the warming of cities. By paving with light colored concrete, in addition to replacing asphalt with light-colored concrete, communities can lower their average temperature.[36]
In many U.S. cities, pavement covers about 30-40% of the surface area.[35] This directly affects the temperature of the city, and contributes to the urban heat island effect. Paving with light-colored concrete would lower temperatures of paved areas and improve nighttime visibility.[35] The potential of energy saving within an area is also high. With lower temperatures, the demand for air conditioning decreases, saving energy.
Atlanta has tried to mitigate the heat-island effect. City officials noted that when using heat-reflecting concrete, their average city temperature decreased by 6 °F.[37] The Design Trust for Public Space found that by slightly raising the albedo value in in New York City, beneficial effects such as energy savings could be achieved.[citation needed] It was concluded that this could be accomplished by the replacement of black asphalt with light-colored concrete.
However, in winter this may be a disadvantage as ice will form more easily and remain longer on the light colored surfaces as they will be colder due to less energy absorbed from the reduced amount of sunlight in winter.[36]
Concrete dust
Building demolition and natural disasters such as earthquakes often release a large amount of concrete dust into the local atmosphere. Concrete dust was concluded to be the major source of dangerous air pollution following the Great Hanshin earthquake.[38]
Health concerns
The presence of some substances in concrete, including useful and unwanted additives, can cause health concerns. Natural radioactive elements (K, U and Th) can be present in various concentration in concrete dwellings, depending on the source of the raw materials used.[39] Toxic substances may also be added to the mixture for making concrete by unscrupulous makers. Dust from rubble or broken concrete upon demolition or crumbling may cause serious health concerns depending also on what had been incorporated in the concrete.
Concrete handling/safety precautions
Handling of wet concrete must always be done with proper protective equipment. Contact with wet concrete can cause skin chemical burns due to the caustic nature of the mixture of cement and water. Indeed, the pH of fresh cement water is highly alkaline due to the presence of free potassium and sodium hydroxides in solution (pH ~ 13.5). Eyes, hands and feet must be correctly protected to avoid any direct contact with wet concrete and washed without delay if necessary.

Damage modes
Concrete can be damaged by many processes such as, e.g., the expansion of corrosion products of the steel reinforcement bars, freezing of trapped water, fire or radiant heat, aggregate expansion, sea water effects, bacterial corrosion, leaching, erosion by fast-flowing water, physical damage and chemical damage (from carbonation, chlorides, sulfates and distillate water).
Manufacturers of cement and concrete admixtures must keep on top of microbiological contamination in raw materials, intermediates and final products to prevent product spoilage. One method of keeping controlling contamination is through 2nd Generation ATP test.[40]
Concrete repair
Concrete pavement preservation (CPP) and concrete pavement restoration (CPR) are techniques used to manage the rate of pavement deterioration on concrete streets, highways and airports. Without changing concrete grade, this non-overlay method is used to repair isolated areas of distress. CPP and CPR techniques include slab stabilization, full- and partial-depth repair, dowel bar retrofit, cross stitching longitudinal cracks or joints, diamond grinding and joint and crack resealing. CPR methods, developed over the last 40 years, are utilized in lieu of short-lived asphalt overlays and bituminous patches to repair roads. These methods are often less expensive [citation needed]than an asphalt overlay but last three times longer and provide a greener solution.[41]
CPR techniques can be used to address specific problems or bring a pavement back to its original quality. When repairing a road, design data, construction data, traffic data, environmental data, previous CPR activities and pavement condition, must all be taken into account. Pavements repaired using CPR methods usually last 15 years. The methods are described below.
- Slab stabilization restores support to concrete slabs by filling small voids that develop underneath the concrete slab at joints, cracks or the pavement edge.
- Full-depth repairs fixes cracked slabs and joint deterioration by removing at least a portion of the existing slab and replacing it with new concrete.
- Partial-depth repairs corrects surface distress and joint-crack deterioration in the upper third of the concrete slab. Placing a partial-depth repair involves removing the deteriorated concrete, cleaning the patch area and placing new concrete.
- Dowel bar retrofit consists of cutting slots in the pavement across the joint or crack, cleaning the slots, placing the dowel bars and backfilling the slots with new concrete. Dowel bar retrofits link slabs together at transverse cracks and joints so that the load is evenly distributed across the crack or joint.
- Cross-stitching longitudinal cracks or joints repairs low-severity longitudinal cracks. This method adds reinforcing steel to hold the crack together tightly.
- Diamond grinding, by removing faulting, slab warping, studded tire wear and unevenness resulting from patches, diamond grinding creates a smooth, uniform pavement profile. Diamond grinding reduces road noise by providing a longitudinal texture, which is quieter than transverse textures. The longitudinal texture also enhances surface texture and skid resistance in polished pavements.
- Joint and crack sealing minimizes the infiltration of surface water and incompressible material into the joint system. Minimizing water entering the joint reduces sub-grade softening, slows pumping and erosion of the sub-base fines, and may limit dowel-bar corrosion caused by de-icing chemicals.[42]
Concrete recycling
Recycling:The multiple use of a product represents another way to conserve natural resources and avoid wastes. This process is usually termed as “recycling”.
Recycled Concrete : Hardened concrete that has been processed for reuse, usually as aggregates.
Concrete recycling is an increasingly common method of disposing of concrete structures. Concrete debris was once routinely shipped to landfills for disposal, but recycling is increasing due to improved environmental awareness, governmental laws, and economic benefits.
Concrete, which must be free of trash, wood, paper and other such materials, is collected from demolition sites and put through a crushing machine, often along with asphalt, bricks, and rocks.
Reinforced concrete contains rebar and other metallic reinforcements, which are removed with magnets and recycled elsewhere. The remaining aggregate chunks are sorted by size. Larger chunks may go through the crusher again. Smaller pieces of concrete are used as gravel for new construction projects. Aggregate base gravel is laid down as the lowest layer in a road, with fresh concrete or asphalt placed over it. Crushed recycled concrete can sometimes be used as the dry aggregate for brand new concrete if it is free of contaminants, though the use of recycled concrete limits strength and is not allowed in many jurisdictions. On March 3, 1983, a government funded research team (the VIRL research.codep) approximated that almost 17% of worldwide landfill was by-products of concrete based waste.
Recycling concrete provides environmental benefits, conserving landfill space and use as aggregate reduces the need for gravel mining.
World records
The world record for the largest concrete pour in a single project is the Three Gorges Dam in Hubei Province, China by the Three Gorges Corporation. The amount of concrete used in the construction of the dam is estimated at 16 million cubic meters over 17 years. The previous record was 3.2 million cubic meters held by Itaipu hydropower station in Brazil. [43] [44]
Concrete pumping
The world record was set at on 7 August 2009 during the construction of the Parbati Hydroelectric Project, near the village of Suind, Himachal Pradesh, India, when the concrete mix was pumped through a vertical height of 715 m (2,346 ft).[45][46]
Continuous pours
The world record for largest continuously poured concrete raft was achieved in August, 2007 in Abu Dhabi by contracting firm, Al Habtoor-CCC Joint Venture. The pour (a part of the foundation for the Abu Dhabi's Landmark Tower) was 16,000 cubic meters of concrete poured within a two day period.[47] The previous record (close to 10,500 cubic meters) was held by Dubai Contracting Company and achieved March 23, 2007.[48]
The world record for largest continuously poured concrete floor was completed November 8, 1997 in Louisville, Kentucky by design-build firm, EXXCEL Project Management. The monolithic placement consisted of 225,000 square feet (20,900 m2) of concrete placed within a 30 hour period, finished to a flatness tolerance of FF 54.60 and a levelness tolerance of FL 43.83. This surpassed the previous record by 50% in total volume and 7.5% in total area.[49][50]
The record for the largest continuously placed underwater concrete pour was completed October 18, 2010 in New Orleans, Louisiana by contractor, C.J. Mahan Construction Company, LLC out of Grove City, Ohio. The placement consisted of 10,224 cubic yards of concrete placed in a 58 hour period using two concrete pumps and two dedicated concrete batch plants. Upon curing, this placement will allow the 50,180 square foot cofferdam to be dewatered approximately 26 feet below sea level to allow the construction of the IHNC GIWW Sill & Monolith Project to be completed in the dry.[citation needed]
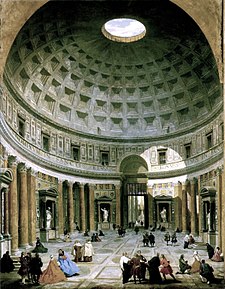
Use of concrete in infrastructure
Mass concrete structures
These include gravity dams such as the Hoover Dam, the Itaipu Dam, and the Three Gorges Dam and large breakwaters. Concrete that is poured all at once in one block (so that there are no weak points where the concrete is "welded" together) is used for tornado shelters.
Reinforced concrete structures
Reinforced concrete contains steel reinforcing that is designed and placed in structural members at specific positions to cater for all the stress conditions that the member is required to accommodate.
Prestressed concrete structures
Prestressed concrete is a form of reinforced concrete that builds in compressive stresses during construction to oppose those found when in use. This can greatly reduce the weight of beams or slabs, by better distributing the stresses in the structure to make optimal use of the reinforcement. For example a horizontal beam will tend to sag down. If the reinforcement along the bottom of the beam is prestressed, it can counteract this.
In pre-tensioned concrete, the prestressing is achieved by using steel or polymer tendons or bars that are subjected to a tensile force prior to casting, or for post-tensioned concrete, after casting.
Concrete textures
When one thinks of concrete, the image of a dull, gray concrete wall often comes to mind. With the use of form liner, concrete can be cast and molded into different textures and used for decorative concrete applications. Sound/retaining walls, bridges, office buildings and more serve as the optimal canvases for concrete art. For example, the Pima Freeway/Loop 101 retaining and sound walls in Scottsdale, Arizona, feature desert flora and fauna, a 67-foot (20 m) lizard and 40-foot (12 m) cacti along the 8-mile (13 km) stretch. The project, titled "The Path Most Traveled," is one example of how concrete can be shaped using elastomeric form liner.
-
Three textures of concrete featured in Scottsdale, AZ, created with form liner.
-
A 67-foot concrete lizard basks in the sun, featured on a sound/retaining wall in Scottsdale, AZ.
-
40-foot cacti decorate a sound/retaining wall in Scottsdale, AZ.
Building with concrete
Concrete is one of the most durable building materials. It provides superior fire resistance compared with wooden construction, can gain strength over time. Structures made of concrete can have a long service life. Concrete is the most widely used construction material in the world with annual consumption estimated at between 21 and 31 billion tonnes [citation needed].
Environmentally sustainable
With its 100-year service life, concrete conserves resources by reducing the need for reconstruction. Its ingredients are cement and readily available natural materials: water, aggregate (sand and gravel or crushed stone). Concrete does not require any CO2 absorbing trees to be cut down. The land required to extract the materials needed to make concrete is only a fraction of that used to harvest forests for lumber.

Concrete absorbs CO2 throughout its lifetime through carbonation, helping reduce its carbon footprint. A recent study [51] indicates that in countries with the most favorable recycling practices, it is realistic to assume that approximately 86% of the concrete is carbonated after 100 years. During this time, the concrete will absorb approximately 57% of the CO2 emitted during the original calcination. About 50% of the CO2 is absorbed within a short time after concrete is crushed during recycling operations.
Concrete consists of between 7% and 15% cement, its only energy-intensive ingredient. A study [52] comparing the CO2 emissions of several different building materials for construction of residential and commercial buildings found that concrete accounted for 147 kg of CO2 per 1000 kg used, metals accounted for 3000 kg of CO2 and wood accounted for 127 kg of CO2. The quantity of CO2 generated during the cement manufacturing process can be reduced by changing the raw materials used in its manufacture.
A new environmentally friendly blend of cement known as Portland-limestone cement (PLC) is gaining ground all over the world. It contains up to 15% limestone, rather than the 5% in regular Portland cement and results in 10% less CO2 emissions from production with no impact on product performance. Concrete made with PLC performs similarly to concrete made with regular cement and thus PLC-based concrete can be widely used as a replacement. In Europe, PLC-based concrete has replaced about 40% of general use concrete. In Canada, PLC will be included in the National Building Code in 2010. The approval of PLC is still under consideration in the United States.
Energy efficiency
Energy requirements for transportation of concrete are low because it is produced locally from local resources, typically manufactured within 100 kilometers of the job site. Once in place, concrete offers significant energy efficiency over the lifetime of a building .[53] Concrete walls leak air far less than those made of wood-frames. Air leakage accounts for a large percentage of energy loss from a home. The thermal mass properties of concrete increase the efficiency of both residential and commercial buildings. By storing and releasing the energy needed for heating or cooling, concrete's thermal mass delivers year-round benefits by reducing temperature swings inside and minimizing heating and cooling costs. While insulation reduces energy loss through the building envelope, thermal mass uses walls to store and release energy. Modern concrete wall systems use both insulation and thermal mass to create an energy-efficient building. Insulating Concrete Forms (ICFs) are hollow blocks or panels made of either insulating foam or rastra that are stacked to form the shape of the walls of a building and then filled with reinforced concrete to create the structure.

Fire safety and quality of life
Concrete buildings are more resistant to fire than those constructed using wood or steel frames. Since concrete does not burn and stops fire from spreading, it offers total fire protection for occupants and their property. Concrete reduces the risk of structural collapse and is an effective fire shield, providing safe means of escape for occupants and protection for firefighters. Furthermore, it does not produce any smoke or toxic gases and does not drip molten particles, which can spread fire. Neither heat, flames nor the water used to extinguish a fire seriously affect the structure of concrete walls and floors making repairs after a fire a relatively simple task.
A study[citation needed] was conducted in Sweden by Olle Lundberg on the cost of fire damage associated with larger fires in multi-unit buildings, based on statistics from the insurance association in Sweden (Försäkringsförbundet). The study was limited to buildings with an insured value greater than €150,000. It covered 125 fires that occurred between 1995 and 2004, about 10% of the fires in multi-family homes, but 56% of the major fires.) The results showed that:
- the average insurance payout per fire, per unit in wood frame buildings was around five times that of fires in concrete buildings (approximately €50,000 compared with €10,000)
- a major fire is more than 11 times more likely to develop in a wood-frame house than in one built using concrete
- among the burned houses, 50% of those made with wood had to be demolished, whereas only 9% of the concrete ones were beyond repair
- the fire spread to neighbouring apartments in only three of the 55 fires in concrete houses
- of those 55 fires, 45 were in attics and roofing
Options for non-combustible construction include floors, ceilings and roofs made of cast-in-place and hollow-core precast concrete. For walls, concrete masonry technology and Insulating Concrete Forms (ICFs) are additional options. ICFs are hollow blocks or panels made of fire-proof insulating foam that are stacked to form the shape of the walls of a building and then filled with reinforced concrete to create the structure.
“Fire-wall” tests, in which ICF walls were subjected to a continuous gas flame with a temperature of more than 1000°C for as long as 4 hours showed no significant breaks in the concrete layer or dangerous transmission of heat. In comparison, wood frame walls normally collapse in an hour or less under these conditions. Concrete provides stable compartmentation in large industrial and multi-storey buildings so a fire starting in one section does not spread to others.
Using concrete to construct buildings offers the best possible protection and safety in fires:
- it does not burn or add to fire load
- it has high resistance to fire, preventing it from spreading thus reduces resulting environmental pollution
- it does not produce any smoke, toxic gases or drip molten particles
- it reduces the risk of structural collapse
- it provides safe means of escape for occupants and access for firefighters as it is an effective fire shield
- it is not affected by the water used to put out a fire
- it is easy to repair after a fire and thus helps residents and businesses recover sooner
- it resists extreme fire conditions, making it ideal for storage facilities with a high fire load
- it provides complete fire protection so there is normally no need for additional measures
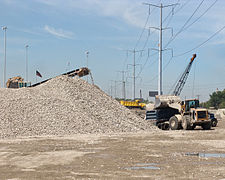
Concrete also provides the best resistance of any building material to high winds, hurricanes, tornadoes due to its lateral stiffness that results in minimal horizontal movement. When properly designed for ductility, it also provides superior resistance to seismic events. It does not rust, rot or sustain growth of mold and stands up well to the freeze – thaw cycle. As a result of all these benefits, insurance for concrete homes is often 15 to 25 percent lower than for comparable wood frame homes.
Concrete buildings also have excellent indoor air quality with no off-gassing, toxicity and release of volatile organic compounds so they are generally healthier to live in than those made of wood or steel. As it is practically inert and waterproof, concrete does not need volatile organic-based preservatives, special coatings or sealers. Concrete can be easily cleaned with organic, non-toxic substances. Its sound insulating properties make buildings and homes a quiet and comfortable living environment. After accounting for sound passing through windows, a concrete home is about two-thirds quieter than a comparable wood-frame home.[54]
Due to the long life of concrete structures, their impacts on the environment are negligible. Once built, they have minimal maintenance requirements and as a result minimal social disruption. Using concrete reduces construction waste as it is used on an as-required basis, thereby minimizing the waste put into landfills.
Recycling and recyclable
A nearly inert material, concrete is suitable as a medium for recycling waste and industrial byproducts. Fly ash, slag and silica fume are used in making concrete, which helps reduce embodied energy, carbon footprint and quantity of landfill materials. The process of making cement also uses waste materials. Tires have high energy content and can supplement coal as fuel in the kiln. Industrial byproducts such as ash from coal combustion, fly ash from power stations as well as mill scale and foundry sand from steel casting provide the silica, calcium, alumina and iron needed for making cement. Even kiln dust, a solid waste generated by cement manufacturing, is often recycled back into the kiln as a raw material. Old concrete that has reached the end of its service life can be recycled and reused as granular fill for road beds.
See also
|
|
|

References
Notes
- ^ The Roman Pantheon: The Triumph of Concrete
- ^ Lomborg, Bjørn (2001). The Skeptical Environmentalist: Measuring the Real State of the World. p. 138. ISBN 0521804477.
- ^ "Minerals commodity summary - cement - 2007". US United States Geographic Service. 2007-06-01. Retrieved 2008-01-16.
- ^ Stella L. Marusin (January 1, 1996). "Ancient Concrete Structures" (Document). Concrete International. pp. 56–58.
{{cite document}}
: Unknown parameter|issue=
ignored (help); Unknown parameter|volume=
ignored (help) - ^ Donald H. Campbell and Robertt L. Folk. "Ancient Egyptian Pyramids--Concrete or Rock". Concrete International. 13 (8): 28 & 30–39.
- ^ Lancaster, Lynne (2005). Concrete Vaulted Construction in Imperial Rome. Innovations in Context. Cambridge University Press. ISBN 978-0-511-16068-4.
- ^ D.S. Robertson: Greek and Roman Architecture, Cambridge, 1969, p. 233
- ^ Henry Cowan: The Masterbuilders, New York 1977, p. 56, ISBN 978-0-471-02740-9
- ^ Robert Mark, Paul Hutchinson: "On the Structure of the Roman Pantheon", Art Bulletin, Vol. 68, No. 1 (1986), p. 26, fn. 5
- ^ http://www.allacademic.com/meta/p_mla_apa_research_citation/0/2/0/1/2/p20122_index.html
- ^ http://www.djc.com/special/concrete/10003364.htm
- ^ olemiss.edu - Missing File
- ^ http://www.concreteresearch.org/PDFsandsoon/Inhomog%20Denver.pdf
- ^ http://www.concreteresearch.org
- ^ a b U.S. Federal Highway Administration. "Admixtures". Retrieved 2007-01-25.
- ^ Cement Admixture Association. "CAA". www.admixtures.org.uk. Retrieved 2008-04-02.
- ^ Kosmatka, S.H. (1988). Design and Control of Concrete Mixtures. Skokie, IL, USA: Portland Cement Association. pp. 17, 42, 70, 184. ISBN 0-89312-087-1.
{{cite book}}
: Unknown parameter|coauthors=
ignored (|author=
suggested) (help) - ^ U.S. Federal Highway Administration. "Fly Ash". Retrieved 2007-01-24.
- ^ U.S. Federal Highway Administration. "Ground Granulated Blast-Furnace Slag". Retrieved 2007-01-24.
- ^ U.S. Federal Highway Administration. "Silica Fume". Retrieved 2007-01-24.
- ^ article of Maksym Bulavytskyi (Ukraine)
- ^ Premixed Cement Paste
- ^ Measuring, Mixing, Transporting, and Placing Concrete
- ^ U.S. patent 5,443,313 - Method for producing construction mixture for concrete
- ^ "Concrete Testing". Retrieved 2008-11-10.
- ^ Resulting strength distribution in vertical elements researched and presented at the article "Concrete Inhomogeneity of Vertical Cast-In-Place Elements In Skeleton-Type Buildings"
- ^ The Cement Sustainability Initiative: Progress report, World Business Council for Sustainable Development, published 2002-06-01
- ^ http://www.sustainableconcrete.org.uk/main.asp?page=0
- ^
Mahasenan, Natesan (2003). "The Cement Industry and Global Climate Change: Current and Potential Future Cement Industry CO2 Emissions". Greenhouse Gas Control Technologies - 6th International Conference. Oxford: Pergamon. pp. 995–1000. ISBN 9780080442761.
{{cite book}}
:|access-date=
requires|url=
(help); External link in
(help); Unknown parameter|chapterurl=
|chapterurl=
ignored (|chapter-url=
suggested) (help); Unknown parameter|coauthors=
ignored (|author=
suggested) (help) - ^ EIA - Emissions of Greenhouse Gases in the U.S. 2006-Carbon Dioxide Emissions
- ^ Water Environment Federation, Alexandria, VA; and American Society of Civil Engineers, Reston, VA. "Urban Runoff Quality Management." WEF Manual of Practice No. 23; ASCE Manual and Report on Engineering Practice No. 87. 1998. ISBN 1-57278-039-8. Chapter 1.
- ^ G. Allen Burton, Jr., Robert Pitt (2001). Stormwater Effects Handbook: A Toolbox for Watershed Managers, Scientists, and Engineers. New York: CRC/Lewis Publishers. ISBN 0-87371-924-7.
{{cite book}}
: CS1 maint: multiple names: authors list (link) Chapter 2. - ^ U.S. Environmental Protection Agency (EPA). Washington, DC. "Protecting Water Quality from Urban Runoff." Document No. EPA 841-F-03-003. February 2003.
- ^ United States. National Research Council. Washington, DC. "Urban Stormwater Management in the United States." October 15, 2008. pp. 18-20.
- ^ a b c "Cool Pavement Report" (PDF). Environmental Protection Agency. June 2005. Retrieved 2009-02-06.
- ^ a b Gore, A (2008). World Changing: A User's Giode for the 21st Century. New York: Abrams. p. 258.
{{cite book}}
: Unknown parameter|coauthors=
ignored (|author=
suggested) (help) - ^ "Concrete facts". Pacific Southwest Concrete Alliance. Retrieved 2009-02-06.
- ^ http://jeq.scijournals.org/cgi/reprint/31/3/718.pdf
- ^ Radionuclide content of concrete building blocks and radiation dose rates in some dwellings in Ibadan, Nigeria
- ^ http://academy.luminultra.com/images/stories/docs/Product%20Validation%20-%20Cement_Concrete%20Admixtures.pdf
- ^ [1] Minnesota DOT
- ^ [2] Airport Business
- ^ "Concrete Pouring of Three Gorges Project Sets World Record". People’s Daily. 2001-01-04. Retrieved 2009-08-24.
- ^ China’s Three Gorges Dam By The Numbers
- ^ "Concrete Pumping to 715 m Vertical - A New World Record Parbati Hydroelectric Project Inclined Pressure Shaft Himachal Pradesh - A case Study". The Masterbuilder. Retrieved 21 October 2010.
- ^ "SCHWING Stetter Launches New Truck mounted Concrete Pump S-36". NBM&CW (New Building Materials and Construction World). October 2009. Retrieved 21 October 2010.
- ^ Al Habtoor Engineering - Abu Dhabi - Landmark Tower has a record-breaking pour - September/October 2007, Page 7.
- ^ Record concrete pour takes place on Al Durrah
- ^ "Continuous cast: Exxcel Contract Management oversees record concrete pour". US Concrete Products. 1998-03-01. Retrieved 2009-08-25.
- ^ Exxcel Project Management - Design Build, General Contractors -
- ^ Nordic Innovation Centre Project 03018 http://www.nordicinnovation.net/img/03018_carbon_dioxide_uptake_in_demolished_and_crushed_concrete.pdf
- ^ Pentalla, Vesa, Concrete and Sustainable Development, ACI Materials Journal, September- October 1997, American Concrete Institute, Farmington Hills, MI, 1997
- ^ Gajda, John, Energy Use of Single Family Houses with Various Exterior Walls, Construction Technology Laboratories Inc, 2001
- ^ Cyril M. Harris (1993). Noise Control in Buildings: A Guide for Architects and Engineers. Mcgraw-Hill. ISBN 978-0070268876.
Bibliography
- Matthias Dupke: Textilbewehrter Beton als Korrosionsschutz. Diplomica Verlag, Hamburg 2010, ISBN 978-3-8366-9405-6.
External links
- Template:Dmoz
- FLY ASH: ITs origin, applications and the environment
- Fly ash in concrete How Fly Ash Contributes to Concrete Durability and Strength.
- Concrete History Oct 1 2009
- Refractory Concrete Information related to heat resistant concrete; recipes, ingredients mixing ratio, work with and applications.
- Inhomogeneity of concrete strength distribution by volume of vertical monolithic (cast in situ) elements Reserves of concrete strength. Information may be used when design buildings against progressive failure.
- The History of Concrete
- Concrete carbonation chemistry at the TU Dresden
- Howard Kanare - Problems With Moisture in Concrete
- Short film on the reinforced concrete buildings that Ove Arup helped design for Dudley Zoo in the 1930s
- British Precast Concrete Federation