Brick: Difference between revisions
m Reverted edits by 71.40.207.2 (talk) to last version by Materialscientist |
No edit summary |
||
Line 9: | Line 9: | ||
A '''brick''' is a [[block]] or a single unit of a [[ceramic]] material used in [[masonry]] construction. Typically bricks are stacked together or laid as [[brickwork]] using various kinds of [[mortar (masonry)|mortar]] to hold the bricks together and make a permanent structure.<ref>World Book Encyclopedia</ref> Bricks are typically produced in common or standard sizes in bulk quantities. They have been regarded as one of the longest lasting and strongest [[building material]]s used throughout history. |
A '''brick''' is a [[block]] or a single unit of a [[ceramic]] material used in [[masonry]] construction. Typically bricks are stacked together or laid as [[brickwork]] using various kinds of [[mortar (masonry)|mortar]] to hold the bricks together and make a permanent structure.<ref>World Book Encyclopedia</ref> Bricks are typically produced in common or standard sizes in bulk quantities. They have been regarded as one of the longest lasting and strongest [[building material]]s used throughout history. |
||
In the general sense, a "brick" is a standard-sized weight-bearing building unit. Bricks are laid in horizontal courses, sometimes dry and sometimes with [[mortar (masonry)|mortar]]. When the term is used in this sense, the brick might be made from [[clay]], lime-and-sand, concrete, or shaped stone. In a less clinical and more colloquial sense, bricks are made from dried earth, usually from clay-bearing subsoil. In some cases, such as [[adobe]], the brick is merely dried. More commonly it is fired in a kiln of some sort to form a true ceramic. |
In the general sense, a "brick" is a standard-sized weight-bearing building unit. Bricks are laid in horizontal courses, sometimes dry and sometimes with [[mortar (masonry)|mortar]]. When the term is used in this sense, the brick might be made from [[clay]], lime-and-sand, concrete, or shaped stone. In a less clinical and more colloquial sense, bricks are made from dried earth, usually from clay-bearing subsoil. In some cases, such as [[adobe]], the brick is merely dried. More commonly it is fired in a kiln of some sort to form a true ceramic.Bricks are fun. |
||
==History== |
==History== |
Revision as of 12:46, 12 February 2014


A brick is a block or a single unit of a ceramic material used in masonry construction. Typically bricks are stacked together or laid as brickwork using various kinds of mortar to hold the bricks together and make a permanent structure.[1] Bricks are typically produced in common or standard sizes in bulk quantities. They have been regarded as one of the longest lasting and strongest building materials used throughout history.
In the general sense, a "brick" is a standard-sized weight-bearing building unit. Bricks are laid in horizontal courses, sometimes dry and sometimes with mortar. When the term is used in this sense, the brick might be made from clay, lime-and-sand, concrete, or shaped stone. In a less clinical and more colloquial sense, bricks are made from dried earth, usually from clay-bearing subsoil. In some cases, such as adobe, the brick is merely dried. More commonly it is fired in a kiln of some sort to form a true ceramic.Bricks are fun.
History

Middle East
The earliest bricks were dried brick, meaning they were formed from clay-bearing earth or mud and dried (usually in the sun) until they were strong enough for use. The oldest discovered bricks, originally made from shaped mud and dating before 7500 BC, were found at Tell Aswad, in the upper Tigris region and in southeast Anatolia close to Diyarbakir.[2] Other more recent findings, dated between 7,000 and 6,395 BC, come from Jericho, Catal Hüyük, and the ancient Indus Valley cities of Buhen, Mohenjo-daro, Harappa,[3] and Mehrgarh.[4]


Ceramic, or fired brick was used as early as 2900 BC in early Indus Valley cities [5]
China
In pre-modern China, bricks were being used from the 2nd millennium BCE at a site near Xi'an.[6] Bricks were produced on a larger scale under the Western Zhou dynasty about 3,000 years ago, and evidence for some of the first fired bricks ever produced has been discovered in ruins dating back to the Zhou.[7][8][9] The carpenter's manual Yingzao Fashi, published in 1103 at the time of the Song Dynasty described the brick making process and glazing techniques then in use. Using the 17th century encyclopedic text Tiangong Kaiwu, historian Timothy Brook outlined the brick production process of Ming Dynasty China:
- "...the kilnmaster had to make sure that the temperature inside the kiln stayed at a level that caused the clay to shimmer with the colour of molten gold or silver. He also had to know when to quench the kiln with water so as to produce the surface glaze. To anonymous laborers fell the less skilled stages of brick production: mixing clay and water, driving oxen over the mixture to trample it into a thick paste, scooping the paste into standardized wooden frames (to produce a brick roughly 42cm long, 20cm wide, and 10cm thick), smoothing the surfaces with a wire-strung bow, removing them from the frames, printing the fronts and backs with stamps that indicated where the bricks came from and who made them, loading the kilns with fuel (likelier wood than coal), stacking the bricks in the kiln, removing them to cool while the kilns were still hot, and bundling them into pallets for transportation. It was hot, filthy work.

Europe
Early civilizations around the Mediterranean adopted the use of fired bricks, including the Ancient Greeks and Romans. The Roman legions operated mobile kilns,[citation needed] and built large brick structures throughout the Roman Empire, stamping the bricks with the seal of the legion.
During the Early Middle Ages the use of bricks in construction became popular in Northern Europe, after being introduced there from Northern-Western Italy. An independent style of brick architecture, known as brick Gothic (similar to Gothic architecture) flourished in places that lacked indigenous sources of rocks. Examples of this architectural style can be found in modern-day Denmark, Germany, Poland, and Russia.
This style evolved into Brick Renaissance as the stylistic changes associated with the Italian Renaissance spread to northern Europe, leading to the adoption of Renaissance elements into brick building. A clear distinction between the two styles only developed at the transition to Baroque architecture. In Lübeck, for example, Brick Renaissance is clearly recognisable in buildings equipped with terracotta reliefs by the artist Statius von Düren, who was also active at Schwerin (Schwerin Castle) and Wismar (Fürstenhof).

Long distance bulk transport of bricks and other construction equipment remained prohibitively expensive until the development of modern transportation infrastructure, with the construction of canal, roads and railways.
Industrial era
Production of bricks increased massively with the onset of the Industrial Revolution and the rise in factory building in England. For reasons of speed and economy, bricks were increasingly preferred as building material to stone, even in areas where the stone was available. It was at this time in London, that bright red brick was chosen for construction in order to make the buildings more visible in the heavy fog and to prevent traffic accidents.[10]
The transition from the traditional method of production known as 'hand-moulding' to a mechanised form of mass production slowly took place during the first half of the nineteenth century. Possibly the first successful brick-making machine was patented by a Mr Henry Clayton, employed at the Atlas Works in Middlesex, England, in 1855, and was capable of producing up to 25,000 bricks daily with minimal supervision.[11] His mechanical apparatus soon achieved widespread attention after it was adopted for use by the South Eastern Railway Company for brick-making at their factory near Folkestone.[12] The Bradley & Craven Ltd ‘Stiff-Plastic Brickmaking Machine’ was patented in 1853, apparently predating Clayton. Bradley & Craven went on to be a dominant manufacturer of brickmaking machinery.[13]
The demand for high office building construction at the turn of the 20th century, led to a much greater use of cast and wrought iron and later steel and concrete. The use of brick for skyscraper construction severely limited the size of the building - the Monadnock Building, built in 1896 in Chicago required exceptionally thick walls to maintain the structural integrity of its 17 storeys.
Following pioneering work in the 1950s at the Swiss Federal Institute of Technology [disambiguation needed] and the Building Research Establishment in Watford, UK, the use of improved masonry for the construction of tall structures up to 18 storeys high was made viable. However, the use of brick has largely remained restricted to small to medium sized buildings, as steel and concrete remain superior materials for high-rise construction.[14]
Methods of manufacture
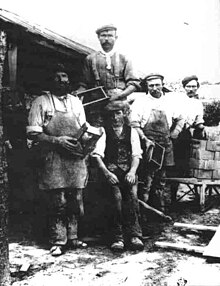
Modern clay bricks are formed in one of three processes – soft mud, dry press, or extruded.
Normally, brick contains the following ingredients:[15]
- Silica (sand) – 50% to 60% by weight
- Alumina (clay) – 20% to 30% by weight
- Lime – 2 to 5% by weight
- Iron oxide – ≤ 7% by weight
- Magnesia – less than 1% by weight
Mud bricks
The soft mud method is the most common, as it is the most economical. It starts with the raw clay, preferably in a mix with 25–30% sand to reduce shrinkage. The clay is first ground and mixed with water to the desired consistency. The clay is then pressed into steel moulds with a hydraulic press. The shaped clay is then fired ("burned") at 900–1000 °C to achieve strength.
Rail kilns

In modern brickworks, this is usually done in a continuously fired tunnel kiln, in which the bricks are fired as they move slowly through the kiln on conveyors, rails, or kiln cars, which achieves a more consistent brick product. The bricks often have lime, ash, and organic matter added, which accelerates the burning process.
Bull's Trench Kilns
In India, brick making is typically a manual process. The most common type of brick kiln in use there is the Bull's Trench Kiln (BTK), based on a design developed by British engineer W. Bull in the late 19th century.
An oval or circular trench is dug, 6–9 metres wide, 2-2.5 metres deep, and 100–150 metres in circumference. A tall exhaust chimney is constructed in the centre. Half or more of the trench is filled with "green" (unfired) bricks which are stacked in an open lattice pattern to allow airflow. The lattice is capped with a roofing layer of finished brick.
In operation, new green bricks, along with roofing bricks, are stacked at one end of the brick pile; cooled finished bricks are removed from the other end for transport to their destinations. In the middle, the brick workers create a firing zone by dropping fuel (coal, wood, oil, debris, and so on) through access holes in the roof above the trench.

The advantage of the BTK design is a much greater energy efficiency compared with clamp or scove kilns. Sheet metal or boards are used to route the airflow through the brick lattice so that fresh air flows first through the recently burned bricks, heating the air, then through the active burning zone. The air continues through the green brick zone (pre-heating and drying the bricks), and finally out the chimney, where the rising gases create suction which pulls air through the system. The reuse of heated air yields savings in fuel cost.
As with the rail process above, the BTK process is continuous. A half dozen laborers working around the clock can fire approximately 15,000–25,000 bricks a day. Unlike the rail process, in the BTK process the bricks do not move. Instead, the locations at which the bricks are loaded, fired, and unloaded gradually rotate through the trench.[16]
Dry pressed bricks
The dry press method is similar to the soft mud brick method, but starts with a much thicker clay mix, so it forms more accurate, sharper-edged bricks. The greater force in pressing and the longer burn make this method more expensive.
Extruded bricks
For extruded bricks the clay is mixed with 10–15% water (stiff extrusion) or 20–25% water (soft extrusion) in a pugmill. This mixture is forced through a die to create a long cable of material of the desired width and depth. This mass is then cut into bricks of the desired length by a wall of wires. Most structural bricks are made by this method as it produces hard, dense bricks, and suitable dies can produce perforations as well. The introduction of such holes reduces the volume of clay needed, and hence the cost. Hollow bricks are lighter and easier to handle, and have different thermal properties from solid bricks. The cut bricks are hardened by drying for 20 to 40 hours at 50 to 150 °C before being fired. The heat for drying is often waste heat from the kiln.
European-style extruded bricks or blocks are used in single-wall construction with finishes applied on the inside and outside. Their many voids comprise a greater proportion of the volume than the solid, thin walls of fired clay. Such bricks are made in 15-, 25-, 30-, 42- and 50-cm widths. Some models have very high thermal insulation properties, making them suitable for zero-energy buildings.
Calcium-Silicate bricks

The raw materials for calcium-silicate bricks include lime mixed with quartz, crushed flint or crushed siliceous rock together with mineral colourants. The materials are mixed and left until the lime is completely hydrated; the mixture is then pressed into moulds and cured in an autoclave for two or three hours to speed the chemical hardening. The finished bricks are very accurate and uniform, although the sharp arrises need careful handling to avoid damage to brick (and bricklayer). The bricks can be made in a variety of colours; white is common but pastel shades can be achieved. This type of brick is common in Sweden, especially in houses built or renovated in the 1970s, where it is known as "Mexitegel" (en: Mexi[can] Bricks). In India these are known as Fly ash bricks, manufactured using the FaL-G (fly ash, lime and gypsum) process. Calcium-silicate bricks are also manufactured in Canada and the United States, and meet the criteria set forth in ASTM C73 – 10 Standard Specification for Calcium Silicate Brick (Sand-Lime Brick). It has lower embodied energy than cement based man-made stone and clay brick.[citation needed]
Concrete bricks

Bricks of concrete with sand aggregate can be made using a simple machine and a basic assembly line. A conveyor belt adds the mixture to a machine, which pours a measured amount of concrete into a form. The form is vibrated to remove bubbles, after which it is raised to reveal the wet bricks, spaced out on a plywood sheet. A small elevator then stacks these palettes, after which a forklift operator moves them to the brickyard for drying.
Influence on fired colour

The fired colour of clay bricks is influenced by the chemical and mineral content of the raw materials, the firing temperature, and the atmosphere in the kiln. For example, pink coloured bricks are the result of a high iron content, white or yellow bricks have a higher lime content. Most bricks burn to various red hues; as the temperature is increased the colour moves through dark red, purple and then to brown or grey at around 1,300 °C (2,372 °F). Calcium silicate bricks have a wider range of shades and colours, depending on the colourants used. The names of bricks may reflect their origin and colour, such as London stock brick and Cambridgeshire White.
"Bricks" formed from concrete are usually termed blocks, and are typically pale grey in colour. They are made from a dry, small aggregate concrete which is formed in steel moulds by vibration and compaction in either an "egglayer" or static machine. The finished blocks are cured rather than fired using low-pressure steam. Concrete blocks are manufactured in a much wider range of shapes and sizes than clay bricks and are also available with a wider range of face treatments – a number of which simulate the appearance of clay bricks.
An impervious and ornamental surface may be laid on brick either by salt glazing, in which salt is added during the burning process, or by the use of a "slip," which is a glaze material into which the bricks are dipped. Subsequent reheating in the kiln fuses the slip into a glazed surface integral with the brick base.
Natural stone bricks are of limited modern utility due to their enormous comparative mass, the consequent foundation needs, and the time-consuming and skilled labour needed in their construction and laying. They are very durable and considered more handsome than clay bricks by some. Only a few stones are suitable for bricks. Common materials are granite, limestone and sandstone. Other stones may be used (for example, marble, slate, quartzite, and so on) but these tend to be limited to a particular locality.
Optimal dimensions, characteristics, and strength

For efficient handling and laying, bricks must be small enough and light enough to be picked up by the bricklayer using one hand (leaving the other hand free for the trowel). Bricks are usually laid flat and as a result the effective limit on the width of a brick is set by the distance which can conveniently be spanned between the thumb and fingers of one hand, normally about four inches (about 100 mm). In most cases, the length of a brick is about twice its width, about eight inches (about 200 mm) or slightly more. This allows bricks to be laid bonded in a structure which increases stability and strength (for an example, see the illustration of bricks laid in English bond, at the head of this article). The wall is built using alternating courses of stretchers, bricks laid longways, and headers, bricks laid crossways. The headers tie the wall together over its width. In fact, this wall is built in a variation of English bond called English cross bond where the successive layers of stretchers are displaced horizontally from each other by half a brick length. In true English bond, the perpendicular lines of the stretcher courses are in line with each other.
A bigger brick makes for a thicker (and thus more insulating) wall. Historically, this meant that bigger bricks were necessary in colder climates (see for instance the slightly larger size of the Russian brick in table below), while a smaller brick was adequate, and more economical, in warmer regions. A notable illustration of this correlation is the Green Gate in Gdansk; built in 1571 of imported Dutch brick, too small for the colder climate of Gdansk, it was notorious for being a chilly and drafty residence. Nowadays this is no longer an issue, as modern walls typically incorporate specialized insulation materials.
The correct brick for a job can be selected from a choice of colour, surface texture, density, weight, absorption and pore structure, thermal characteristics, thermal and moisture movement, and fire resistance.
Standard | Imperial | Metric |
---|---|---|
![]() |
9 × 4⅓ × 3 in | 230 × 110 × 76 mm |
![]() |
9 × 4¼ × 2¼ in | 228 × 108 × 54 mm |
![]() |
9 × 4¼ × 2¾ in | 240 × 115 × 71 mm |
![]() |
9 × 4¼ × 2¾ in | 228 × 107 × 69 mm |
![]() |
9 × 4¼ × 2½ in | 240 × 115 × 63 mm |
![]() |
10 × 4¾ × 2½ in | 250 × 120 × 65 mm |
![]() |
8¾ × 4 × 3 in | 222 × 106 × 73 mm |
![]() |
10 × 4¾ × 2½ in | 250 × 120 × 62 mm |
![]() |
8½ × 4 × 2½ in | 215 × 102.5 × 65 mm |
![]() |
7⅝ × 3⅝ × 2¼ in | 194 × 92 × 57 mm |
In England, the length and width of the common brick has remained fairly constant over the centuries (but see brick tax), but the depth has varied from about two inches (about 51 mm) or smaller in earlier times to about two and a half inches (about 64 mm) more recently. In the United Kingdom, the usual size of a modern brick is 215 × 102.5 × 65 mm (about 8+5⁄8 × 4+1⁄8 × 2+5⁄8 inches), which, with a nominal 10 mm (3⁄8 inch) mortar joint, forms a unit size of 225 × 112.5 × 75 mm (9 × 4+1⁄2 × 3 inches), for a ratio of 6:3:2.
In the United States, modern standard bricks are (controlled by American Society for Testing and Materials ASTM [17]) about 8 × 3+5⁄8 × 2+1⁄4 inches (203 × 92 × 57 mm). The more commonly used is the modular brick 7+5⁄8 × 3+5⁄8 × 2+1⁄4 inches (194 × 92 × 57 mm). This modular brick of 7+5⁄8 plus a 3⁄8 mortar joint eased the calculations of the number of bricks in a given run.[18]
Some brickmakers create innovative sizes and shapes for bricks used for plastering (and therefore not visible) where their inherent mechanical properties are more important than their visual ones.[19] These bricks are usually slightly larger, but not as large as blocks and offer the following advantages:
- a slightly larger brick requires less mortar and handling (fewer bricks), which reduces cost
- their ribbed exterior aids plastering
- more complex interior cavities allow improved insulation, while maintaining strength.
Blocks have a much greater range of sizes. Standard coordinating sizes in length and height (in mm) include 400×200, 450×150, 450×200, 450×225, 450×300, 600×150, 600×200, and 600×225; depths (work size, mm) include 60, 75, 90, 100, 115, 140, 150, 190, 200, 225, and 250. They are usable across this range as they are lighter than clay bricks. The density of solid clay bricks is around 2,000 kg/m³: this is reduced by frogging, hollow bricks, and so on, but aerated autoclaved concrete, even as a solid brick, can have densities in the range of 450–850 kg/m³.
Bricks may also be classified as solid (less than 25% perforations by volume, although the brick may be "frogged," having indentations on one of the longer faces), perforated (containing a pattern of small holes through the brick, removing no more than 25% of the volume), cellular (containing a pattern of holes removing more than 20% of the volume, but closed on one face), or hollow (containing a pattern of large holes removing more than 25% of the brick's volume). Blocks may be solid, cellular or hollow
The term "frog" for the indentation on one bed of the brick is a word that often excites curiosity as to its origin. The most likely explanation is that brickmakers also call the block that is placed in the mould to form the indentation a frog. Modern brickmakers usually use plastic frogs but in the past they were made of wood. When these are wet and have clay on them they resemble the amphibious kind of frog and this is where they got their name. Over time this term also came to refer to the indentation left by them.


The compressive strength of bricks produced in the United States ranges from about 1000 lbf/in² to 15,000 lbf/in² (7 to 105 MPa or N/mm² ), varying according to the use to which the brick are to be put. In England clay bricks can have strengths of up to 100 MPa, although a common house brick is likely to show a range of 20–40 MPa.
Use
Bricks are used for building, block paving and pavement. In the USA, brick pavement was found incapable of withstanding heavy traffic,[citation needed] but it is coming back into use as a method of traffic calming or as a decorative surface in pedestrian precincts. For example, in the early 1900s, most of the streets in the city of Grand Rapids, Michigan were paved with brick. Today, there are only about 20 blocks of brick paved streets remaining (totalling less than 0.5 percent of all the streets in the city limits).[20]
Bricks in the metallurgy and glass industries are often used for lining furnaces, in particular refractory bricks such as silica, magnesia, chamotte and neutral (chromomagnesite) refractory bricks. This type of brick must have good thermal shock resistance, refractoriness under load, high melting point, and satisfactory porosity. There is a large refractory brick industry, especially in the United Kingdom, Japan, the United States, Belgium and the Netherlands.
In Northwest Europe, bricks have been used in construction for centuries. Until recently, almost all houses were built almost entirely from bricks. Although many houses are now built using a mixture of concrete blocks and other materials, many houses are skinned with a layer of bricks on the outside for aesthetic appeal.
Engineering bricks are used where strength, low water porosity or acid (flue gas) resistance are needed.
In the UK a redbrick university is one founded and built in the Victorian era, often as a technical college. The term serves to distinguish these polytechnic colleges from older, more classics-oriented universities.
Colombian architect Rogelio Salmona was noted for his extensive use of red brick in his buildings and for using natural shapes like spirals, radial geometry and curves in his designs.[21] Most buildings in Colombia are made of brick, given the abundance of clay in equatorial countries like this one.
Limitations
Starting in the 20th century, the use of brickwork declined in some areas due to concerns with earthquakes. Earthquakes such as the San Francisco earthquake of 1906 and the 1933 Long Beach earthquake revealed the weaknesses of brick masonry in earthquake-prone areas. During seismic events, the mortar cracks and crumbles, and the bricks are no longer held together. Brick masonry with steel reinforcement, which helps hold the masonry together during earthquakes, was used to replace many of the unreinforced masonry buildings. Retrofitting older unreinforced masonry structures has been mandated in many jurisdictions.
Gallery
-
Roman opus reticulatum on Hadrian's Villa in Tivoli, Italy (2nd century)
-
Eastern gable of church of St. James in Toruń (14th century)
-
Decorative pattern made of strongly fired bricks in Radzyń Castle (14th century)
-
Brick sculpturing on Thornbury Castle, Thornbury, near Bristol, England. The chimneys were erected in 1514
-
A typical brick house in the Netherlands.
-
Decorative bricks in St Michael and All Angels Church, Blantyre, Malawi
-
A brick kiln, Tamil Nadu, India
-
Porotherm style clay block brick
-
Moulding bricks, Poland
-
Brick made as a byproduct of ironstone mining Normanby – UK
See also
- Brick tinting
- Brickwork
- Ceramic building material
- Ceramics
- Clinker brick
- Concrete masonry unit (cinder block)
- Fire brick
- Fly ash brick
- Masonry
- Millwall brick, a street weapon in England
- Mortar, the materials that bricks are bound together with
- Mudbrick
- Roman brick
- Tile
- Wienerberger
Notes
- ^ World Book Encyclopedia
- ^ Template:Fr icon IFP Orient – Tell Aswad. Wikis.ifporient.org. Retrieved on 2012-11-16.
- ^ History of brickmaking, Encyclopædia Britannica.
- ^ Kenoyer, Jonathan Mark (2005), "Uncovering the keys to the Lost Indus Cities", Scientific American, 15: 24–33, doi:10.1038/scientificamerican0105-24sp
- ^ [1], Bricks and urbanism in the Indus Valley.
- ^ Brook, 19–20
- ^ Earliest Chinese building brick appeared in Xi'an (中國最早磚類建材在西安現身). takungpao.com (2010-1-28)
- ^ China's first brick, possible earliest brick in China (藍田出土"中華第一磚" 疑似我國最早的"磚")
- ^ 西安發現全球最早燒制磚 (Earliest fired brick discovered in Xi'an). sina.com.tw. 2010-01-30 (in Chinese)
- ^ Peter Ackroyd (2001). London the Biography. Random House. p. 435.
- ^ "Henry Clayton". Retrieved 17 December 2012.
- ^ The Mechanics Magazine and Journal of Engineering, Agricultural Machinery, Manufactures and Shipbuilding. Retrieved 17 December 2012.
- ^ The First Hundred Years: the Early History of Bradley & Craven, Limited, Wakefield, England by Bradley & Craven Ltd (1963)
- ^ "The History of Bricks". De Hoop:Steenwerve Brickfields.
- ^ Punmia, B.C.; Jain, Ashok Kumar (2003), Basic Civil Engineering, Firewall Media, pp. 33–, ISBN 978-81-7008-403-7
{{citation}}
: CS1 maint: multiple names: authors list (link) - ^ Pakistan Environmental Protection Agency, Brick Kiln Units (PDF file)
- ^ ASTM C652 – 13 Standard Specification for Hollow Brick (Hollow Masonry Units Made From Clay or Shale). Astm.org. Retrieved on 2013-10-01.
- ^ bricksizes. Maconline.org. Retrieved on 2013-10-01.
- ^ Crammix Maxilite. crammix.co.za
- ^ Michigan | Success Stories | Preserve America | Office of the Secretary of Transportation | U.S. Department of Transportation.
- ^ Romero, Simon (6 October 2007). "Rogelio Salmona, Colombian Architect Who Transformed Cities, Is Dead at 78". The New York Times.
References
- Brook, Timothy (1998), The Confusions of Pleasure: Commerce and Culture in Ming China, Berkeley: University of California Press, ISBN 0-520-22154-0
Further reading
- Aragus, Philippe (2003), Brique et architecture dans l'Espagne médiévale, Bibliothèque de la Casa de Velazquez, 2 (in French), Madrid
{{citation}}
: CS1 maint: location missing publisher (link) - Campbell, James W.; Pryce, Will, photographer (2003), Brick: a World History, London & New York: Thames & Hudson
{{citation}}
: CS1 maint: multiple names: authors list (link) - Coomands, Thomas; VanRoyen, Harry, eds. (2008), "Novii Monasterii, 7", Medieval Brick Architecture in Flanders and Northern Europe, Koksijde: Ten Duinen
- Das, Saikia Mimi; Das, Bhargab Mohan; Das, Madan Mohan (2010), Elements of Civil Engineering, New Delhi: PHI Learning Private Limited, ISBN 978-81-203-4097-8
- Kornmann, M. (2007), Clay Bricks and Roof Tiles, Manufacturing and Properties, Paris: Lasim, ISBN 2-9517765-6-X
{{citation}}
:|first2=
missing|last2=
(help) - Plumbridge, Andrew; Meulenkamp, Wim (2000), Brickwork. Architecture and Design, London: Seven Dials, ISBN 1-84188-039-6
- Dobson, E. A. (1850), Rudimentary Treatise on the Manufacture of Bricks and Tiles, London: John Weale
- Hudson, Kenneth (1972) Building Materials; chap. 3: Bricks and tiles. London: Longman; pp. 28–42
- Lloyd, N. (1925), History of English Brickwork, London: H. Greville Montgomery
External links
select an article title from: Wikisource:1911 Encyclopædia Britannica
- Compressive strength test of Bricks
- Brick in 20th-Century Architecture
- Brick Industry Association
- Mason Contractors Association of America
- Masonry Institute of America
- "Bricks Made Automatically by One-Man Machine" Popular Mechanics, April 1935, pg. 523 bottom-left