Pellet mill
A pellet mill, also known as a pellet press,[1] is a type of mill or machine press used to create pellets from powdered material. Pellet mills are unlike grinding mills, in that they combine small materials into a larger, homogeneous mass, rather than break large materials into smaller pieces.
Types
There are many types of pellet mills that can be generally grouped into large-scale and small-scale types. According to the production capacity, pellet mill can produce from 1-50 tons of output. According to the structure,pellet mills also can be divided into flat die pellet mill and ring die pellet mill.
Large-scale
There are two common types of large-scale pellet mills: flat die mills and ring die mills. Flat die mills use a flat die with slots. The powder is introduced to the top of the die and as the die rotates a roller presses the powder through the holes in the die. A cutter on the other side of the die cuts the exposed pellet free from the die.[1] In the ring die there are radial slot throughout the die. Powder is fed into the inside of the die and spreaders evenly distribute the powder. Two rollers then compress the powder through the die holes. Two cutters are used to cut the pellets free from the outside of the die.[2]
Large scale pellet mills are usually used to produce animal feed,[1] wood pellets, and fuel pellets for use in a pellet stove.
Small-scale
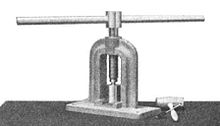
Small-scale mills are usually variations of screw presses or hydraulic presses. The same basic process is used for both types. A die, also known as a mold, holds the uncompressed powder in a shaped pocket. The pocket shape defined the final pellet shape. A platen is attached to the end of the screw (in a screw press) or the ram (in a hydraulic press) which compresses the powder.[3]
Some platens are heated to speed up the time it takes and improve the overall structure of the pellet. They may also have water ports for quick cooling between uses.[citation needed]
Working principle
- The material is conveyed into the modulator through the speed-regulating feeding auger. In order to obtain a good granulation benefit, after adding hot steam for conditioning, the chute-shaped feeding pipe passes through the ring die cover, with the help of graity and the centrifugal force generated by the rotation of the ring die, the material is tightly attached to the ring die cover and the inner wall of the mold(feeding area).
- Under the action of the shifting knife, the material is fed evenly and continuously, and the wedge-shaped space(pressing area) formed by each pressing roller and the ring die.
- because the gap between the working surface of the outer wall of the pressure roller and the working surface of the inner diameter of the ring die is only 0.1-0.3mm, and this gap is basically horizontal, a certain extrusion force(extrusion zone) is formed.
- Due to the feeding of the material, under the strong extrusion between the die and the roller, the material is compacted, extruded into the die hole, and formed into a (forming area) in the die hole.
The material is continuously fed into the pressing zone, then extruded into shape, continuously extruded from the die hole, and cut into various required particle lengths by a cutter with an adjustable distance between the knife edge and the outer wall of the ring die.[4]
Applications
One of the more common applications is to produce KBr pellets which are used in infrared spectroscopy applications.
Animal feed pellets are usually a mixture of dry powdered feedstock, such as flour, sawdust, or grass, and a wet ingredient, such as molasses or steam. Feedstocks for pellet mills can sometimes break down and then re-form, or polymerize, under the extreme heat and pressure of the pellet mill.[citation needed]
References
- ^ a b c Pietsch, Wolfgang (2005), Agglomeration in Industry: Occurrence and Applications, vol. 1, Wiley-VCH, p. 254, ISBN 978-3-527-30582-7.
- ^ Matz, Samuel A. (1991), The chemistry and technology of cereals as food and feed (2nd ed.), Springer, p. 328, ISBN 978-0-442-30830-8.
- ^ Connecticut Agricultural Experiment Station (1898), Tenth Annual Report of the Storrs Agricultural Experiment Station, Storrs, Conn. 1897, Pelton & King, pp. 208–209.
- ^ "Richi Pellet Machine | Pellet Mills | Customize Pellet Production Line". RICHI Pellet Machine. Retrieved 2023-03-08.