Cellulosic ethanol
Cellulosic ethanol is ethanol (ethyl alcohol) produced from cellulose (the stringy fiber of a plant) rather than from the plant's seeds or fruit. It is a biofuel produced from grasses, wood, algae, or other plants. The fibrous parts of the plants are mostly inedible to animals, including humans, except for ruminants (grazing, cud-chewing animals such as cows or sheep) and animals that rely on hindgut fermentation (like horses, rabbits and rhinos).
Interest in cellulosic ethanol is driven by its potential economic value. Growth of cellulose by plants is a mechanism that captures and stores solar energy chemically in nontoxic ways with resultant supplies that are easy to transport and store. Additionally, transport may be unneeded anyway, because grasses or trees can grow almost anywhere temperate. This is why commercially practical cellulosic ethanol is may be a next development for the biofuel industry that could reduce demand for oil and gas drilling in ways that grain-based ethanol fuel alone cannot. Potential exists for the many benefits of carbonaceous liquid fuels and petrochemicals (which today's standard of living depends on) but in a carbon cycle–balanced and renewable way (recycling surface and atmosphere carbon instead of pumping underground carbon up into it and thus adding to it). Commercially practical cellulosic alcohol could also avoid one of the problems with today's conventional (grain-based) biofuels, which is that they set up competition for grain with food purposes, potentially driving up the price of food. Production of cellulosic alcohol is currently uneconomical and not practiced on a commercial scale.
Overview
Cellulosic ethanol is a type of biofuel produced from lignocellulose, a structural material that comprises much of the mass of plants and is composed mainly of cellulose, hemicellulose and lignin. Popular sources of lignocellulose include both agricultural waste products (e.g. corn stover or wood chips) and grasses like switchgrass and miscanthus species.[1] These raw materials for ethanol production have the advantage of being abundant and diverse and would not compete with food production, unlike the more commonly used corn and cane sugars.[2] However, they also require more processing to make the sugar monomers available to the microorganisms typically used to produce ethanol by fermentation, which drives up the price of cellulos-derived ethanol.[3]
Cellulosic ethanol can reduce greenhouse gas emissions by 85% over reformulated gasoline.[4] By contrast, starch ethanol (e.g., from corn), which most frequently uses natural gas to provide energy for the process, may not reduce greenhouse gas emissions at all depending on how the starch-based feedstock is produced.[5] According to the National Academy of Sciences in 2011, there is no commercially viable bio-refinery in existence to convert lignocellulosic biomass to fuel.[6] Absence of production of cellulosic ethanol in the quantities required by the regulation was the basis of a United States Court of Appeals for the District of Columbia decision announced January 25, 2013, voiding a requirement imposed on car and truck fuel producers in the United States by the Environmental Protection Agency requiring addition of cellulosic biofuels to their products.[7] These issues, along with many other difficult production challenges, led George Washington University policy researchers to state that "in the short term, [cellulosic] ethanol cannot meet the energy security and environmental goals of a gasoline alternative."[8]
History
The French chemist, Henri Braconnot, was the first to discover that cellulose could be hydrolyzed into sugars by treatment with sulfuric acid in 1819.[9] The hydrolyzed sugar could then be processed to form ethanol through fermentation. The first commercialized ethanol production began in Germany in 1898, where acid was used to hydrolyze cellulose. In the United States, the Standard Alcohol Company opened the first cellulosic ethanol production plant in South Carolina in 1910. Later, a second plant was opened in Louisiana. However, both plants were closed after World War I due to economic reasons.[10]
The first attempt at commercializing a process for ethanol from wood was done in Germany in 1898. It involved the use of dilute acid to hydrolyze the cellulose to glucose, and was able to produce 7.6 liters of ethanol per 100 kg of wood waste (18 US gal (68 L) per ton). The Germans soon developed an industrial process optimized for yields of around 50 US gallons (190 L) per ton of biomass. This process soon found its way to the US, culminating in two commercial plants operating in the southeast during World War I. These plants used what was called "the American Process" — a one-stage dilute sulfuric acid hydrolysis. Though the yields were half that of the original German process (25 US gallons (95 L) of ethanol per ton versus 50), the throughput of the American process was much higher. A drop in lumber production forced the plants to close shortly after the end of World War I. In the meantime, a small but steady amount of research on dilute acid hydrolysis continued at the USFS's Forest Products Laboratory.[11][12][13] During World War II, the US again turned to cellulosic ethanol, this time for conversion to butadiene to produce synthetic rubber. The Vulcan Copper and Supply Company was contracted to construct and operate a plant to convert sawdust into ethanol. The plant was based on modifications to the original German Scholler process as developed by the Forest Products Laboratory. This plant achieved an ethanol yield of 50 US gal (190 L) per dry ton, but was still not profitable and was closed after the war.[14]
With the rapid development of enzyme technologies in the last two decades, the acid hydrolysis process has gradually been replaced by enzymatic hydrolysis. Chemical pretreatment of the feedstock is required to hydrolyze (separate) hemicellulose, so it can be more effectively converted into sugars. The dilute acid pretreatment is developed based on the early work on acid hydrolysis of wood at the USFS's Forest Products Laboratory. Recently, the Forest Products Laboratory together with the University of Wisconsin–Madison developed a sulfite pretreatment to overcome the recalcitrance of lignocellulose for robust enzymatic hydrolysis of wood cellulose.[15]
In his 2007 State of the Union Address on January 23, 2007, US President George W. Bush announced a proposed mandate for 35 billion US gallons (130×10 9 L) of ethanol by 2017. Later that year, the US Department of Energy awarded $385 million in grants aimed at jump-starting ethanol production from nontraditional sources like wood chips, switchgrass, and citrus peels.[16]
Production methods
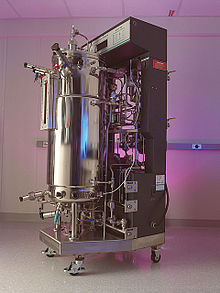
The stages to produce ethanol using a biological approach are:[17]
- A "pretreatment" phase to make the lignocellulosic material such as wood or straw amenable to hydrolysis
- Cellulose hydrolysis (cellulolysis) to break down the molecules into sugars
- Microbial fermentation of the sugar solution
- Distillation and dehydration to produce pure alcohol
In 2010, a genetically engineered yeast strain was developed to produce its own cellulose-digesting enzymes.[18] Assuming this technology can be scaled to industrial levels, it would eliminate one or more steps of cellulolysis, reducing both the time required and costs of production.[citation needed]
Although lignocellulose is the most abundant plant material resource, its usability is curtailed by its rigid structure. As a result, an effective pretreatment is needed to liberate the cellulose from the lignin seal and its crystalline structure so as to render it accessible for a subsequent hydrolysis step.[19] By far, most pretreatments are done through physical or chemical means. To achieve higher efficiency, both physical and chemical pretreatments are required. Physical pretreatment involves reducing biomass particle size by mechanical processing methods such as milling or extrusion. Chemical pretreatment partially depolymerizes the lignocellulose so enzymes can access the cellulose for microbial reactions.[20]
Chemical pretreatment techniques include acid hydrolysis, steam explosion, ammonia fiber expansion, organosolv, sulfite pretreatment,[15] AVAP® (SO2-ethanol-water) fractionation,[21] alkaline wet oxidation and ozone pretreatment.[22] Besides effective cellulose liberation, an ideal pretreatment has to minimize the formation of degradation products because they can inhibit the subsequent hydrolysis and fermentation steps.[23] The presence of inhibitors further complicates and increases the cost of ethanol production due to required detoxification steps. For instance, even though acid hydrolysis is probably the oldest and most-studied pretreatment technique, it produces several potent inhibitors including furfural and hydroxymethylfurfural.[24] Ammonia Fiber Expansion (AFEX) is an example of a promising pretreatment that produces no inhibitors.[25]
Most pretreatment processes are not effective when applied to feedstocks with high lignin content, such as forest biomass. These require alternative or specialized approaches. Organosolv, SPORL ('sulfite pretreatment to overcome recalcitrance of lignocellulose') and SO2-ethanol-water (AVAP®) processes are the three processes that can achieve over 90% cellulose conversion for forest biomass, especially those of softwood species. SPORL is the most energy efficient (sugar production per unit energy consumption in pretreatment) and robust process for pretreatment of forest biomass with very low production of fermentation inhibitors. Organosolv pulping is particularly effective for hardwoods and offers easy recovery of a hydrophobic lignin product by dilution and precipitation.[26]</ref> AVAP® process effectively fractionates all types of lignocellulosics into clean highly digestible cellulose, undegraded hemicellulose sugars, reactive lignin and lignosulfonates, and is characterized by efficient recovery of chemicals.[27][28]
Cellulolytic processes
The hydrolysis of cellulose (cellulolysis) produces simple sugars that can be fermented into alcohol. There are two major cellulolysis processes: chemical processes using acids, or enzymatic reactions using cellulases.[17]
Chemical hydrolysis
In the traditional methods developed in the 19th century and at the beginning of the 20th century, hydrolysis is performed by attacking the cellulose with an acid.[29] Dilute acid may be used under high heat and high pressure, or more concentrated acid can be used at lower temperatures and atmospheric pressure. A decrystallized cellulosic mixture of acid and sugars reacts in the presence of water to complete individual sugar molecules (hydrolysis). The product from this hydrolysis is then neutralized and yeast fermentation is used to produce ethanol. As mentioned, a significant obstacle to the dilute acid process is that the hydrolysis is so harsh that toxic degradation products are produced that can interfere with fermentation. BlueFire Renewables uses concentrated acid because it does not produce nearly as many fermentation inhibitors, but must be separated from the sugar stream for recycle [simulated moving bed chromatographic separation, for example] to be commercially attractive.[citation needed]
Agricultural Research Service scientists found they can access and ferment almost all of the remaining sugars in wheat straw. The sugars are located in the plant's cell walls, which are notoriously difficult to break down. To access these sugars, scientists pretreated the wheat straw with alkaline peroxide, and then used specialized enzymes to break down the cell walls. This method produced 93 US gallons (350 L) of ethanol per ton of wheat straw.[30]
Enzymatic hydrolysis
Cellulose chains can be broken into glucose molecules by cellulase enzymes. This reaction occurs at body temperature in the stomachs of ruminants such as cattle and sheep, where the enzymes are produced by microbes. This process uses several enzymes at various stages of this conversion. Using a similar enzymatic system, lignocellulosic materials can be enzymatically hydrolyzed at a relatively mild condition (50 °C and pH 5), thus enabling effective cellulose breakdown without the formation of byproducts that would otherwise inhibit enzyme activity. All major pretreatment methods, including dilute acid, require an enzymatic hydrolysis step to achieve high sugar yield for ethanol fermentation.[25]
Fungal enzymes can be used to hydrolyze cellulose. The raw material (often wood or straw) still has to be pre-treated to make it amenable to hydrolysis.[31] In 2005, Iogen Coroporation announced it was developing a process using the fungus Trichoderma reesei to secrete "specially engineered enzymes" for an enzymatic hydrolysis process.[32]
Another Canadian company, SunOpta, uses steam explosion pretreatment, providing its technology to Verenium (formerly Celunol Corporation)'s facility in Jennings, Louisiana, Abengoa's facility in Salamanca, Spain, and a China Resources Alcohol Corporation in Zhaodong. The CRAC production facility uses corn stover as raw material.[33]
Microbial fermentation
Traditionally, baker's yeast (Saccharomyces cerevisiae), has long been used in the brewery industry to produce ethanol from hexoses (six-carbon sugars). Due to the complex nature of the carbohydrates present in lignocellulosic biomass, a significant amount of xylose and arabinose (five-carbon sugars derived from the hemicellulose portion of the lignocellulose) is also present in the hydrolysate. For example, in the hydrolysate of corn stover, approximately 30% of the total fermentable sugars is xylose. As a result, the ability of the fermenting microorganisms to use the whole range of sugars available from the hydrolysate is vital to increase the economic competitiveness of cellulosic ethanol and potentially biobased proteins.[citation needed]
In recent years, metabolic engineering for microorganisms used in fuel ethanol production has shown significant progress.[34] Besides Saccharomyces cerevisiae, microorganisms such as Zymomonas mobilis and Escherichia coli have been targeted through metabolic engineering for cellulosic ethanol production. An attraction towards alternative fermentation organism is its ability to ferment five carbon sugars improving the yield of the feed stock. This ability is often found in bacteria [35] based organisms.[citation needed]
Recently, engineered yeasts have been described efficiently fermenting xylose,[36][37] and arabinose,[38] and even both together.[39] Yeast cells are especially attractive for cellulosic ethanol processes because they have been used in biotechnology for hundreds of years, are tolerant to high ethanol and inhibitor concentrations and can grow at low pH values to reduce bacterial contamination.[citation needed]
Combined hydrolysis and fermentation
Some species of bacteria have been found capable of direct conversion of a cellulose substrate into ethanol. One example is Clostridium thermocellum, which uses a complex cellulosome to break down cellulose and synthesize ethanol. However, C. thermocellum also produces other products during cellulose metabolism, including acetate and lactate, in addition to ethanol, lowering the efficiency of the process. Some research efforts are directed to optimizing ethanol production by genetically engineering bacteria that focus on the ethanol-producing pathway.[40]
Gasification process (thermochemical approach)

The gasification process does not rely on chemical decomposition of the cellulose chain (cellulolysis). Instead of breaking the cellulose into sugar molecules, the carbon in the raw material is converted into synthesis gas, using what amounts to partial combustion. The carbon monoxide, carbon dioxide and hydrogen may then be fed into a special kind of fermenter. Instead of sugar fermentation with yeast, this process uses Clostridium ljungdahlii bacteria.[41] This microorganism will ingest carbon monoxide, carbon dioxide and hydrogen and produce ethanol and water. The process can thus be broken into three steps:
- Gasification — Complex carbon-based molecules are broken apart to access the carbon as carbon monoxide, carbon dioxide and hydrogen
- Fermentation — Convert the carbon monoxide, carbon dioxide and hydrogen into ethanol using the Clostridium ljungdahlii organism
- Distillation — Ethanol is separated from water
A recent study has found another Clostridium bacterium that seems to be twice as efficient in making ethanol from carbon monoxide as the one mentioned above.[42]
Alternatively, the synthesis gas from gasification may be fed to a catalytic reactor where it is used to produce ethanol and other higher alcohols through a thermochemical process.[43] This process can also generate other types of liquid fuels, an alternative concept successfully demonstrated by the Montreal-based company Enerkem at their facility in Westbury, Quebec.[44]
Hemicellulose to ethanol
Studies are intensively conducted to develop economic methods to convert both cellulose and hemicellulose to ethanol. Fermentation of glucose, the main product of cellulose hydrolyzate, to ethanol is an already established and efficient technique. However, conversion of xylose, the pentose sugar of hemicellulose hydrolyzate, is a limiting factor, especially in the presence of glucose. Moreover, it cannot be disregarded as hemicellulose will increase the efficiency and cost-effectiveness of cellulosic ethanol production.[45]
Sakamoto (2012) et al. show the potential of genetic engineering microbes to express hemicellulase enzymes. The researchers created a recombinant Saccharomyces cerevisiae strain that was able to:
- hydrolyze hemicellulase through codisplaying endoxylanase on its cell surface,
- assimilate xylose by expression of xylose reductase and xylitol dehydrogenase.
The strain was able to convert rice straw hydrolyzate to ethanol, which contains hemicellulosic components. Moreover, it was able to produce 2.5x more ethanol than the control strain, showing the highly effective process of cell surface-engineering to produce ethanol.[45]
Advantages
General advantages of ethanol fuel
Ethanol burns more cleanly and more efficiently than gasoline.[46][47] Because plants consume carbon dioxide as they grow, bioethanol has an overall lower carbon footprint than fossil fuels.[48] Substituting ethanol for oil can also reduce a country's dependence on oil imports.[49]
Advantages of cellulosic ethanol over corn or sugar-based ethanol
U.S. Environmental Protection Agency Draft life cycle GHG emissions reduction results for different time horizon and discount rate approaches[50] (includes indirect land use change effects) | ||
---|---|---|
Fuel Pathway | 100 years + 2% discount rate |
30 years + 0% discount rate |
Corn ethanol (natural gas dry mill)(1) | -16% | +5% |
Corn ethanol (Best case NG DM)(2) | -39% | -18% |
Corn ethanol (coal dry mill) | +13% | +34% |
Corn ethanol (biomass dry mill) | -39% | -18% |
Corn ethanol (biomass dry mill with combined heat and power) |
-47% | -26% |
Brazilian sugarcane ethanol | -44% | -26% |
Cellulosic ethanol from switchgrass | -128% | -124% |
Cellulosic ethanol from corn stover | -115% | -116% |
Notes: (1) Dry mill (DM) plants grind the entire kernel and generally produce only one primary co-product: distillers grains with solubles (DGS). (2) Best case plants produce wet distillers grains co-product. |
Commercial production of cellulosic ethanol, which unlike corn and sugarcane would not compete with food production, would be highly attractive since it would alleviate pressure on these foodcrops.
Although its processing costs are higher, the price of cellulose biomass much cheaper than that of grains or fruits. Moreover, since cellulose is the main component of plants, the whole plant can be harvested, rather than just the fruit or seeds. This results in much better yields; for instance, switchgrass yields twice as much ethanol per acre as corn.[51] Biomass materials for cellulose production require fewer inputs, such as fertilizer, herbicides, and their extensive roots improve soil quality, reduce erosion, and increase nutrient capture.[52][53] The overall carbon footprint and global warming potential of cellulosic ethanol are considerably lower (see chart)[54][55][56] and the net energy output is several times higher than that of corn-based ethanol.
The potential raw material is also plentiful. Around 44% of household waste generated worldwide consists of food and greens.[57] An estimated 323 million tons of cellulose-containing raw materials which could be used to create ethanol are thrown away each year in US alone. This includes 36.8 million dry tons of urban wood wastes, 90.5 million dry tons of primary mill residues, 45 million dry tons of forest residues, and 150.7 million dry tons of corn stover and wheat straw.[58] Moreover, even land marginal for agriculture could be planted with cellulose-producing crops, such as switchgrass, resulting in enough production to substitute for all the current oil imports into the United States.[59]
Paper, cardboard, and packaging comprise around 17% of global household waste;[57] although some of this is recycled. As these products contain cellulose, they are transformable into cellulosic ethanol,[58] which would avoid the production of methane, a potent greenhouse gas, during decomposition.[60]
Disadvantages
General disadvantages
The main overall drawback of ethanol fuel is its lower fuel economy compared to gasoline.[49]
Disadvantages of cellulosic ethanol over corn or sugar-based ethanol
The main disadvantage of cellulosic ethanol is its high cost and complexity of production, which has been the main impediment to its commercialization (see below).[61][62]
Economics
Although the global bioethanol market is sizable (around 110 billion liters in 2019), the vast majority is made from corn or sugarcane, not cellulose.[63] In 2007, the cost of producing ethanol from cellulosic sources was estimated ca. USD 2.65 per gallon (€0.58 per liter), which is around 2–3 times more expensive than ethanol made from corn.[64] However, the cellulosic ethanol market remains relatively small and reliant on government subsidies.[62] The US government originally set cellulosic ethanol targets gradually ramping up from 1 billion liters in 2011 to 60 billion liters in 2022.[65] However, these annual goals have almost always been waived after it became clear there was no chance of meeting them.[61] Most of the plants to produce cellulosic ethanol were canceled or abandoned in the early 2010s.[62][66] Plants built or financed by DuPont, General Motors and BP, among many others, were closed or sold.[67] As of 2018, only one major plant remains in the US.[62]
In order for it to be grown on a large-scale production, cellulose biomass must compete with existing uses of agricultural land, mainly for the production of crop commodities. Of the United States' 2.26 billion acres (9.1 million km2) of unsubmerged land,[68] 33% are forestland, 26% pastureland and grassland, and 20% crop land. A study by the U.S. Departments of Energy and Agriculture in 2005 suggested that 1.3 billion dry tons of biomass is theoretically available for ethanol use while maintaining an acceptable impact on forestry, agriculture.[69]
Comparison with corn-based ethanol
Currently, cellulose is more difficult and more expensive to process into ethanol than corn or sugarcane. The US Department of Energy estimated in 2007 that it costs about $2.20 per gallon to produce cellulosic ethanol, which is 2–3 times much as ethanol from corn. Enzymes that destroy plant cell wall tissue cost USD 0.40 per gallon of ethanol compared to USD 0.03 for corn.[64] However, cellulosic biomass is cheaper to produce than corn, because it requires fewer inputs, such as energy, fertilizer, herbicide, and is accompanied by less soil erosion and improved soil fertility. Additionally, nonfermentable and unconverted solids left after making ethanol can be burned to provide the fuel needed to operate the conversion plant and produce electricity. Energy used to run corn-based ethanol plants is derived from coal and natural gas. The Institute for Local Self-Reliance estimates the cost of cellulosic ethanol from the first generation of commercial plants will be in the $1.90–$2.25 per gallon range, excluding incentives. This compares to the current cost of $1.20–$1.50 per gallon for ethanol from corn and the current retail price of over $4.00 per gallon for regular gasoline (which is subsidized and taxed).[70]
Enzyme-cost barrier
Cellulases and hemicellulases used in the production of cellulosic ethanol are more expensive compared to their first generation counterparts. Enzymes required for maize grain ethanol production cost 2.64-5.28 US dollars per cubic meter of ethanol produced. Enzymes for cellulosic ethanol production are projected to cost 79.25 US dollars, meaning they are 20-40 times more expensive.[71] The cost differences are attributed to quantity required. The cellulase family of enzymes have a one to two order smaller magnitude of efficiency. Therefore, it requires 40 to 100 times more of the enzyme to be present in its production. For each ton of biomass it requires 15-25 kilograms of enzyme.[72] More recent estimates[73] are lower, suggesting 1 kg of enzyme per dry tonne of biomass feedstock. There is also relatively high capital costs associated with the long incubation times for the vessel that perform enzymatic hydrolysis. Altogether, enzymes comprise a significant portion of 20-40% for cellulosic ethanol production. A recent paper[73] estimates the range at 13-36% of cash costs, with a key factor being how the cellulase enzyme is produced. For cellulase produced offsite, enzyme production amounts to 36% of cash cost. For enzyme produced onsite in a separate plant, the fraction is 29%; for integrated enzyme production, the faction is 13%. One of the key benefits of integrated production is that biomass instead of glucose is the enzyme growth medium. Biomass costs less, and it makes the resulting cellulosic ethanol a 100% second-generation biofuel, i.e., it uses no ‘food for fuel’.[citation needed]
Feedstocks
In general there are two types of feedstocks: forest (woody) Biomass and agricultural biomass. In the US, about 1.4 billion dry tons of biomass can be sustainably produced annually. About 370 million tons or 30% are forest biomass.[74] Forest biomass has higher cellulose and lignin content and lower hemicellulose and ash content than agricultural biomass. Because of the difficulties and low ethanol yield in fermenting pretreatment hydrolysate, especially those with very high 5 carbon hemicellulose sugars such as xylose, forest biomass has significant advantages over agricultural biomass. Forest biomass also has high density which significantly reduces transportation cost. It can be harvested year around which eliminates long term storage. The close to zero ash content of forest biomass significantly reduces dead load in transportation and processing. To meet the needs for biodiversity, forest biomass will be an important biomass feedstock supply mix in the future biobased economy. However, forest biomass is much more recalcitrant than agricultural biomass. Recently, the USDA Forest Products Laboratory together with the University of Wisconsin–Madison developed efficient technologies[15][75] that can overcome the strong recalcitrance of forest (woody) biomass including those of softwood species that have low xylan content. Short-rotation intensive culture or tree farming can offer an almost unlimited opportunity for forest biomass production.[76]
Woodchips from slashes and tree tops and saw dust from saw mills, and waste paper pulp are forest biomass feedstocks for cellulosic ethanol production.[77]
Switchgrass (Panicum virgatum) is a native tallgrass prairie grass. Known for its hardiness and rapid growth, this perennial grows during the warm months to heights of 2–6 feet. Switchgrass can be grown in most parts of the United States, including swamplands, plains, streams, and along the shores & interstate highways. It is self-seeding (no tractor for sowing, only for mowing), resistant to many diseases and pests, & can produce high yields with low applications of fertilizer and other chemicals. It is also tolerant to poor soils, flooding, & drought; improves soil quality and prevents erosion due its type of root system.[78]
Switchgrass is an approved cover crop for land protected under the federal Conservation Reserve Program (CRP). CRP is a government program that pays producers a fee for not growing crops on land on which crops recently grew. This program reduces soil erosion, enhances water quality, and increases wildlife habitat. CRP land serves as a habitat for upland game, such as pheasants and ducks, and a number of insects. Switchgrass for biofuel production has been considered for use on Conservation Reserve Program (CRP) land, which could increase ecological sustainability and lower the cost of the CRP program. However, CRP rules would have to be modified to allow this economic use of the CRP land.[78]
Miscanthus × giganteus is another viable feedstock for cellulosic ethanol production. This species of grass is native to Asia and is a sterile hybrid of Miscanthus sinensis and Miscanthus sacchariflorus. It has high crop yields, is cheap to grow, and thrives in a variety of climates. However, because it is sterile, it also requires vegetative propagation, making it more expensive.[79]
It has been suggested that Kudzu may become a valuable source of biomass.[80]
Cellulosic ethanol commercialization
![]() | This section needs to be updated.(December 2015) |
![]() |
Fueled by subsidies and grants, a boom in cellulosic ethanol research and pilot plants occurred in the early 2000s. Companies such as Iogen, POET, and Abengoa built refineries that can process biomass and turn it into ethanol, while companies such as DuPont, Diversa, Novozymes, and Dyadic invested in enzyme research. However, most of these plants were canceled or closed in the early 2010s as technical obstacles proved too difficult to overcome. As of 2018, only one cellulosic ethanol plant remained operational.[62]
In the 2010s, various companies occasionally attempted smaller-scale efforts at commercializing cellulosic ethanol. In 2018, Versalis acquired the defunct Mossi & Ghisolfi Group, which had operated a short-lived plant between 2013 and 2016, with the intention of re-starting production.[81] Xyleco, an engineering firm, claims that the global warming potential of its cellulosic ethanol is 83% lower than gasoline, 77% lower than corn ethanol and 40% lower than sugarcane ethanol,[82] although its commercialization plans have been met with skepticism.[83][84] In 2013, the Brazilian company GranBio, a Brazilian producer of biofuels and biochemicals, commissioned a cellulosic ethanol plant in the state of Alagoas.[85] As of 2020, its theoretical capacity was 30 million liters per year.[86]
Cellulosic ethanol commercialization involves converting cellulose-containing organic matter into cellulosic ethanol for use as a biofuel. The shift from food crop feedstocks (primarily corn) to waste residues and native grasses offers potential opportunities for farmers, biotechnology firms, project developers and investors.[87]
Cellulosic ethanol production
Cellulosic ethanol can be produced from a diverse array of feedstocks, such as wood pulp from trees or any plant matter. However, current economics favor corn-based bioethanol.
Commercialization by country
Australia
Ethtec built a pilot plant in New South Wales. It uses wood residues as a feedstock.[88]
Canada
Iogen Corporation is a developer of cellulosic ethanol process technology. It operated a demonstration unit in Ontario from 2007 to 2012. After the unit was shut down, Iogen laid off the majority of their workforce.[89][90]
Denmark
Inbicon's bioethanol plant in Kalundborg, with the capacity to produce 5.4 million liters (1.4 million gallons) annually, was opened in 2009. Believed to be the world's largest cellulosic ethanol plant as of early 2011, the facility runs on about 30,000 metric tons (33,000 tons) of straw per year and the plant employs about 30 people. The plant also produces 13,000 metric tons of lignin pellets per year, used as fuel at combined-heat-and-power plants, and 11,100 metric tons of C5 molasses which is currently used for biomethane production via anaerobic digestion, and has been tested as a high carbohydrate animal feed supplement and potential bio-based feedstock for production of numerous commodity chemicals including diols, glycols, organic acids, and biopolymer precursors and intermediates.[91]
Since October 2010, an E5 blend of 95% gasoline and 5% cellulosic ethanol blend has been available at 100 filling stations across Denmark. Distributed by Statoil, the Bio95 2G mixture uses ethanol derived from wheat straw collected on Danish fields after harvest and produced by Inbicon (a div. of DONG Energy), using enzyme technology from Novozymes.[92]
Germany
In Straubing, the specialty chemicals company Clariant has been operating a precommercial plant based on its sunliquid® process since 2012. The plant is able to produce up to 1000 tons of cellulosic ethanol from agricultural residues such as wheat straw, corn stover or sugarcane bagasse. The process technology uses enzymatic hydrolysis, followed by fermentation of C5 and C6 sugar into ethanol.[93]
Italy
Italy-based Mossi & Ghisolfi Group broke ground for its 13 million US gallons (49,000 m3) per year cellulosic ethanol facility in Crescentino in northwestern Italy on April 12, 2011. The project will be the largest cellulosic ethanol project in the world, 10 times larger than any of the currently operating demonstration-scale facilities. The plant is "expected to become operational in 2012 and will use a variety of locally sourced feedstocks, beginning with wheat straw and Arundo donax, a perennial giant cane".[94] The company went to bankruptcy on 2018 and had to auction the plant. [95]
Romania
Clariant is building a cellulosic ethanol plant to be sourced with agricultural residues and based on their sunliquid® technology. The plant will have an annual capacity of 50,000 tons of ethanol and be located in Podari in southwestern Romania. [96]
Russia
A commercial factory converting wood (50% softwood + 50% hardwood) into Ethanol is in operation in Northern Russia, the city of Kirov, since 1972 and is still profitable. As side products the company, Kirov Biochemical Works, is offering dry fodder yeast (20 tons/month) and Lignin. To install equipment for drying and burning Lignin, both fresh and accumulated in the landfill, for steam and electricity, a bank loan of $200 million was recently secured.[97]
Spain
Abengoa continues to invest heavily in the necessary technology for bringing cellulosic ethanol to market. Utilizing process and pre-treatment technology from SunOpta Inc., Abengoa is building a 5 million US gallons (19,000 m3) cellulosic ethanol facility in Spain and have recently entered into a strategic research and development agreement with Dyadic International, Inc. (AMEX: DIL), to create new and better enzyme mixtures which may be used to improve both the efficiencies and cost structure of producing cellulosic ethanol.[98]
Sweden
SEKAB has developed an industrial process for production of ethanol from biomass feed-stocks, including wood chips and sugar cane bagasse. The development work is being carried out at an advanced pilot plant in Örnsköldsvik, and has sparked international interest. The technology will be gradually scaled up to commercial production in a new breed of bio-refineries from 2013 to 2015.[99]
United States
The US government actively supports the development and commercialization of cellulosic ethanol through a variety of mechanisms. In the first decade of the 21st century, a lot of companies announced plans to build commercial cellulosic ethanol plants, but most of those plans eventually fell apart, and many of the small companies went bankrupt. Currently (2016), there are many demonstration plants throughout the country, and handful of commercial-scale plants which are in operation or close to it.
Government support
The US Federal government is promoted the development of ethanol from cellulosic feedstocks as an alternative to conventional petroleum transportation fuels. For example, programs sponsored by U.S. Department of Energy (DOE) included research to develop better cellulose hydrolysis enzymes and ethanol-fermenting organisms, to engineering studies of potential processes, to co-funding initial ethanol from cellulosic biomass demonstration and production facilities. This research was conducted by various national laboratories, including the National Renewable Energy Laboratory (NREL), Oak Ridge National Laboratory (ORNL) and Idaho National Laboratory (INL), as well as by universities and private industry. [100]
In May 2008, Congress passed a new farm bill that will accelerate the commercialization of advanced biofuels, including cellulosic ethanol. The Food, Conservation, and Energy Act of 2008 provides for grants covering up to 30% of the cost of developing and building demonstration-scale biorefineries for producing "advanced biofuels," which essentially includes all fuels that are not produced from corn kernel starch. It also allows for loan guarantees of up to $250 million for building commercial-scale biorefineries to produce advanced biofuels.[101]
Using a newly developed tool known as the "Biofuels Deployment Model", Sandia researchers have determined that 21 billion US gallons (79,000,000 m3) of cellulosic ethanol could be produced per year by 2022 without displacing current crops. The Renewable Fuels Standard, part of the 2007 Energy Independence and Security Act, calls for an increase in biofuels production to 36 billion US gallons (140,000,000 m3) a year by 2022.[102]
In January 2011, the USDA approved $405 million in loan guarantees through the 2008 Farm Bill to support the commercialization of cellulosic ethanol at three facilities owned by Coskata, Enerkem and INEOS New Planet BioEnergy. The projects represent a combined 73 million US gallons (280,000 m3) per year production capacity and will begin producing cellulosic ethanol in 2012. The USDA also released a list of advanced biofuel producers who will receive payments to expand the production of advanced biofuels.[103] In July 2011, the US Department of Energy gave in $105 million in loan guarantees to POET for a commercial-scale plant to be built Emmetsburg, Iowa.[104]
The American company Range Fuels announced in July 2007 that it was awarded a construction permit from the state of Georgia to build the first commercial-scale 100-million-US-gallon (380,000 m3)-per-year cellulosic ethanol plant in the US.[105] Construction began in November, 2007.[106] The Range Fuels plant was built in Soperton, GA, but was shut down in January 2011, without ever having produced any ethanol. It had received a $76 million grant from the US Department of Energy, plus $6 million from the State of Georgia, plus an $80 million loan guaranteed by the U.S. Biorefinery Assistance Program.[107]
Commercial development
Their are few commercial-scale cellulosic ethanol plants in the United States.[108]
Company | Location | Feedstock | Capacity (million gal/year) | Operated | Type |
---|---|---|---|---|---|
Abengoa Bioenergy | Hugoton, KS | Wheat straw | 25 - 30 [108][109] | 2013 - 2016 (bankrupt) | Commercial |
American Process, Inc | Alpena, MI | Wood chips | 1.0 | 2012 - 2015[110] | Demonstration |
Verbio | Nevada, IA | Corn stover | 30[111] | 2018 (acquision) [112] | Semi-Commercial |
Environmental issues
According to US Department of Energy studies conducted by the Argonne National Laboratory of the University of Chicago, cellulosic ethanol reduces greenhouse gas emissions (GHG) by 85% over reformulated gasoline. [citation needed]By contrast, starch ethanol (e.g., from corn), which usually uses natural gas to provide energy for the process, reduces greenhouse gas emissions by 18% to 29% over gasoline.[citation needed]
Critics question the likelihood of environmental, energy or economic benefits from cellulosic ethanol technology from non-waste.[113][114]
See also
References
- ^ Ziolkowska JR (2020). "Biofuels technologies: An overview of feedstocks, processes, and technologies". Biofuels for a More Sustainable Future. Elsevier. pp. 1–19. doi:10.1016/b978-0-12-815581-3.00001-4. ISBN 978-0-12-815581-3.
- ^ "The pros and cons of biofuels - Cellulosic ethanol". Fortune. Retrieved 2021-05-03.
{{cite web}}
: CS1 maint: url-status (link) - ^ Markings S (April 25, 2017). "The Disadvantages of Cellulose Biofuel". Sciencing. Retrieved 2021-05-03.
{{cite web}}
: CS1 maint: url-status (link) - ^ Wang M (September 2005). Updated Energy and Greenhouse Gas Emissions Results of Fuel Ethanol (PDF). The 15th International Symposium on Alcohol Fuels. San Diego, CA. Archived from the original (PDF) on 2013-02-16. Retrieved 2013-03-02.
- ^ "Clean cars, cool fuels". 5 (2). Environment California. 2007. Archived from the original on 2007-11-03. Retrieved 2007-11-28.
{{cite journal}}
: Cite journal requires|journal=
(help) - ^ National Research Council of the National Academies (2011), Renewable Fuel Standard: Potential Economic and Environmental Effects of U.S. Biofuel Policy, Washington, D.C.: The National Academies Press, p. 3 of "Summary", doi:10.17226/13105, ISBN 978-0-309-18751-0
- ^ Wald ML (January 25, 2013). "Court Overturns E.P.A.'s Biofuels Mandate". The New York Times. Retrieved January 26, 2013.
wishful thinking rather than realistic estimates
- ^ Somma D, Lobkowicz H, Deason JP (2010). "Growing America's fuel: an analysis of corn and cellulosic ethanol feasibility in the United States" (PDF). Clean Techn Environ Policy. 12 (4): 373–380. doi:10.1007/s10098-009-0234-3. S2CID 111303200.
- ^ Braconnot H (1819). "Verwandlungen des Holzstoffs mittelst Schwefelsäure in Gummi, Zucker und eine eigne Säure, und mittelst Kali in Ulmin". Annalen der Physik. 63 (12): 348. Bibcode:1819AnP....63..347B. doi:10.1002/andp.18190631202.
- ^ Solomon BD, Barnes JR, Halvorsen KE (June 2007). "Grain and cellulosic ethanol: History, economics, and energy policy". Biomass and Bioenergy. 31 (6): 416–425. doi:10.1016/j.biombioe.2007.01.023.
- ^ Saeman JF (1945). "Kinetics of wood saccharification: Hydrolysis of cellulose and decomposition of sugars in dilute acid at high temperature". Industrial and Engineering Chemistry. 37 (1): 43–52. doi:10.1021/ie50421a009.
- ^ Harris EE, Beglinger E, Hajny GJ, Sherrard EC (1945). "Hydrolysis of Wood: Treatment with Sulfuric Acid in a stationary digester". Industrial and Engineering Chemistry. 37 (1): 12–23. doi:10.1021/ie50421a005.
- ^ Conner AH, Lorenz LF (1986). "Kinetic modeling of hardwood prehydrolysis. Part III. Water and dilute acetic acid Prehydrolysis of southern red oak" (PDF). Wood and Fiber Science. 18 (2): 248–263.
- ^ Katzen R, Schell DJ (2006). "Lignocellulosic feedstock Biorefinery: History and Plant Development for Biomass Hydrolysis". In Kamm B, Gruber PR, Kamm M (eds.). Biorefineries - Industrial processes and Products. Vol. 1. Weinheim: Wiley-VCH. pp. 129–138. doi:10.1002/9783527619849.ch6. ISBN 978-3-527-61984-9.
- ^ a b c Zhu JY, Pan XJ, Wang GS, Gleisner R (April 2009). "Sulfite pretreatment (SPORL) for robust enzymatic saccharification of spruce and red pine". Bioresource Technology. 100 (8): 2411–8. doi:10.1016/j.biortech.2008.10.057. PMID 19119005.
- ^ Lammers D (2007-03-04). "Gasification may be key to U.S. Ethanol". CBS News. Archived from the original on 2007-11-22. Retrieved 2007-11-28.
- ^ a b Amezcua-Allieri MA, Sánchez Durán T, Aburto J (2017). "Study of Chemical and Enzymatic Hydrolysis of Cellulosic Material to Obtain Fermentable Sugars". Journal of Chemistry. 2017: 1–9. doi:10.1155/2017/5680105. ISSN 2090-9063.
{{cite journal}}
: CS1 maint: unflagged free DOI (link) - ^ Galazka JM, Tian C, Beeson WT, Martinez B, Glass NL, Cate JH (October 2010). "Cellodextrin transport in yeast for improved biofuel production". Science. 330 (6000): 84–6. Bibcode:2010Sci...330...84G. doi:10.1126/science.1192838. PMID 20829451. S2CID 20444539.
- ^ Mosier N, Wyman C, Dale BE, Elander R, Lee YY, Holtzapple M, Ladisch M (2005). "Features of promising technologies for pretreatment of lignocellulosic biomass". Bioresour Technol. 96 (6): 673–686. doi:10.1016/j.biortech.2004.06.025. PMID 15588770.
- ^ Taylor MJ, Alabdrabalameer HA, Skoulou V (2019-06-30). "Choosing Physical, Physicochemical and Chemical Methods of Pre-Treating Lignocellulosic Wastes to Repurpose into Solid Fuels". Sustainability. 11 (13): 3604. doi:10.3390/su11133604. ISSN 2071-1050.
{{cite journal}}
: CS1 maint: unflagged free DOI (link) - ^ Iakovlev M, van Heiningen A (2012). "Efficient fractionation of spruce by SO2-Ethanol-Water (SEW) treatment: closed mass balances for carbohydrates and sulfur". ChemSusChem. 5 (8): 1625–1637. doi:10.1002/cssc.201100600. PMID 22740146.
- ^ Klinke HB, Thomsen AB, Ahring BK (2004). "Inhibition of ethanol-producing yeast and bacteria by degradation products produced during pre-treatment of biomass". Appl Microbiol Biotechnol. 66 (1): 10–26. doi:10.1007/s00253-004-1642-2. PMID 15300416. S2CID 41941145.
- ^ Olsson L, Hahn-Hägerdal B (1996). "Fermentation of lignocellulosic hydrolysates for ethanol fermentation". Enzyme Microb Technol. 18: 312–331. doi:10.1016/0141-0229(95)00157-3.
- ^ Palmqvist E, Hahn-Hägerdal B (2000). "Fermentation of lignocellulosic hydrolysates. I. Inhibition and deoxification". Bioresour Technol. 74: 17–24. doi:10.1016/s0960-8524(99)00160-1.
- ^ a b Lynd LR (1996). "Overview and evaluation of fuel ethanol from cellulosic biomass: technology, economics, the environment, and policy". Annual Review of Energy and the Environment. 21: 403–465. doi:10.1146/annurev.energy.21.1.403.
- ^ Macfarlane AL, Farid MM, Chen JJ (2010). Organosolv delignification of willow. Lambert Academic Press. ISBN 978-3-8383-9155-7.
- ^ Iakovlev M (2011). SO2-Ethanol-Water Fractionation of Lignocellulosics (PDF) (Ph.D. thesis). Aalto University, Finland.
- ^ US granted 8030039, Retsina T, Pylkkanen V, "Method for the production of fermentable sugars and cellulose from lignocellulosic material", assigned to American Process, Inc.
- ^ Boullanger E (1924). Distillerie Agricole et Industrielle [Wood Alcohol] (in French). Translated by Marc de Piolenc F. Paris: Ballière.
- ^ Perry A (9 April 2010). "Cellulosic Ethanol: Expanding Options, Identifying Obstacles". Agricultural Research Service (ARS). U.S. Department of Agriculture.
- ^ Dashtban M, Schraft H, Qin W (September 2009). "Fungal bioconversion of lignocellulosic residues; opportunities & perspectives". International Journal of Biological Sciences. 5 (6): 578–95. doi:10.7150/ijbs.5.578. PMC 2748470. PMID 19774110.
- ^ "Iogen technology makes it possible (process overview)". Iogen Corp. 2005. Archived from the original on 2006-02-03. Retrieved 2007-11-28.
- ^ "Sunopta updates current cellulosic ethanol projects". Sunopta press release. 2007.
- ^ Jeffries TW, Jin YS (2004). "Metabolic engineering for improved fermentation of pentoses by yeasts". Appl Microbiol Biotechnol. 63 (5): 495–509. doi:10.1007/s00253-003-1450-0. PMID 14595523. S2CID 26069067.
- ^ McMillan JD (January 1993). "Xylose Fermentation to Ethanol: A Review" (PDF). National Renewable Energy Laboratory. U.S. Department of Energy.
- ^ Brat D, Boles E, Wiedemann B (2009). "Functional expression of a bacterial xylose isomerase in Saccharomyces cerevisie". Appl. Environ. Microbiol. 75 (8): 2304–2311. doi:10.1128/AEM.02522-08. PMC 2675233. PMID 19218403.
- ^ Ohgren K, Bengtsson O, Gorwa-Grauslund MF, Galbe M, Hahn-Hagerdal B, Zacchi G (2006). "Simultaneous saccharification and co-fermentation of glucose and xylose in steam-pretreated corn stover at high fiber content with Saccharomyces cerevisiae TMB3400". J Biotechnol. 126 (4): 488–98. doi:10.1016/j.jbiotec.2006.05.001. PMID 16828190.
- ^ Becker J, Boles E (2003). "A modified Saccharomyces cerevisiae strain that consumes L-Arabinose and produces ethanol". Appl Environ Microbiol. 69 (7): 4144–50. doi:10.1128/AEM.69.7.4144-4150.2003. PMC 165137. PMID 12839792.
- ^ Karhumaa K, Wiedemann B, Hahn-Hägerdal B, Boles E, Gorwa-Grauslund MF (April 2006). "Co-utilization of L-arabinose and D-xylose by laboratory and industrial Saccharomyces cerevisiae strains". Microbial Cell Factories. 5: 18. doi:10.1186/1475-2859-5-18. PMC 1459190. PMID 16606456.
{{cite journal}}
: CS1 maint: unflagged free DOI (link) - ^ "Genome Sequencing Reveals Key to Viable Ethanol Production". University of Rochester Press Release. 2 March 2007.
- ^ "Providing for a Sustainable Energy Future by producing clean RENEWABLE liquid energy and green power". Bioengineering Resources Inc. Archived from the original on 2006-04-21. Retrieved 2007-11-28.
- ^ Rajagopalan S, Datar R, Lewis RS (2002). "Formation of Ethanol from Carbon Monoxide via New Microbial Catalyst". Biomass & Energy. 23 (6): 487–493. doi:10.1016/s0961-9534(02)00071-5.
- ^ "Power Energy Fuels Homepage". Enerkem. Power Energy Fuels, Inc. Archived from the original on 2007-12-12. Retrieved 2007-11-28.
- ^ "Westbury, Quebec". Archived from the original on 2011-08-06. Retrieved 2011-07-27.
- ^ a b Sakamoto T, Hasunuma T, Hori Y, Yamada R, Kondo A (April 2012). "Direct ethanol production from hemicellulosic materials of rice straw by use of an engineered yeast strain codisplaying three types of hemicellulolytic enzymes on the surface of xylose-utilizing Saccharomyces cerevisiae cells". Journal of Biotechnology. 158 (4): 203–10. doi:10.1016/j.jbiotec.2011.06.025. PMID 21741417.
- ^ Demain AL, Newcomb M, Wu JH (March 2005). "Cellulase, clostridia, and ethanol". Microbiology and Molecular Biology Reviews. 69 (1): 124–54. doi:10.1128/MMBR.69.1.124-154.2005. PMC 1082790. PMID 15755956.
- ^ "Ethanol Benefits and Considerations". Alternative Fuels Data Center.
- ^ "Alternative Fuels Data Center: Ethanol Benefits and Considerations". afdc.energy.gov. US Department of Energy. Retrieved 2021-05-03.
{{cite web}}
: CS1 maint: url-status (link) - ^ a b Beck K (November 2019). "Advantages & Disadvantages of Ethanol Biofuel". Sciencing. Retrieved 2021-05-03.
{{cite web}}
: CS1 maint: url-status (link) - ^ "EPA Lifecycle Analysis of Greenhouse Gas Emissions from Renewable Fuels - Technical Highlights" (PDF). Retrieved 2009-06-07. See Table 1.
- ^ Montenegro M (5 December 2006). "The numbers behind ethanol, cellulosic ethanol, and biodiesel in the U.S." Grist.
- ^ Nelson R (2007). "Cellulosic ethanol: bioethanol in Kansas" (PDF). Archived from the original (PDF) on 2008-09-10. Retrieved 2007-12-09.
- ^ Rice CW (2002). "Storing Carbon in Soil: Why and How?". Retrieved 2008-11-10.
- ^ Farrell AE, Plevin RJ, Turner BT, Jones AD, O'Hare M, Kammen DM (January 2006). "Ethanol can contribute to energy and environmental goals". Science. 311 (5760): 506–8. Bibcode:2006Sci...311..506F. doi:10.1126/science.1121416. PMID 16439656. S2CID 16061891.
- ^ Crutzen, PJ, Mosier AR, Smith KA, Winiwarter W (2008). "Nitrous oxide release from agro-biofuel production negates global warming reduction by replacing fossil fuels" (PDF). Atmospheric Chemistry and Physics. 8 (2): 389–395. doi:10.5194/acp-8-389-2008.
{{cite journal}}
: CS1 maint: unflagged free DOI (link) - ^ Solomon BD, Barnes JR, Halvorson KE (2007). "History, economics, and energy policy". Biomass Bioenergy. 31 (6): 416–425. doi:10.1016/j.biombioe.2007.01.023.
- ^ a b "Trends in Solid Waste Management". World Bank. Retrieved 2021-05-04.
{{cite web}}
: CS1 maint: url-status (link) - ^ a b Walsh M (10 April 2000). "Biomass Resource Estimates". Oak Ridge, TN: Oak Ridge National Laboratory. Archived from the original on 2008-02-09.
- ^ "Switchgrass Fuel Yields Bountiful Energy: Study". Reuters. January 10, 2008. Retrieved 2008-02-12.
- ^ McKibben B (October 2007). "Carbon's New Math". National Geographic Magazine.
- ^ a b Loyola M (2019-11-23). "Stop the Ethanol Madness". The Atlantic. Retrieved 2021-05-03.
- ^ a b c d e Rapier R. "Cellulosic Ethanol Falling Far Short Of The Hype". Forbes. Retrieved 2021-05-03.
- ^ "Alternative Fuels Data Center: Maps and Data - Global Ethanol Production". afdc.energy.gov. US Department of Energy. May 2020. Retrieved 2021-05-03.
{{cite web}}
: CS1 maint: url-status (link) - ^ a b Osborne S (November 2007). "Energy in 2020: Assessing the Economic Effects of Commercialization of Cellulosic Ethanol" (PDF). US Department of Commerce. Retrieved 2021-05-03.
- ^ Orcutt M (9 May 2012). "U.S. Will Be Hard-Pressed to Meet Its Biofuel Mandates". MIT Technology Review. Archived from the original on 29 April 2014.
- ^ Bullis K (November 2012). "BP Plant Cancellation Darkens Cellulosic Ethanol's Future". MIT Technology Review. Retrieved 2021-05-03.
{{cite web}}
: CS1 maint: url-status (link) - ^ Mayer A (2018-01-02). "Cellulosic Ethanol Push Stalls In The Midwest Amid Financial, Technical Challenges". KCUR 89.3 - NPR in Kansas City. Local news, entertainment and podcasts. Retrieved 2021-05-03.
{{cite web}}
: CS1 maint: url-status (link) - ^ The World Fact Book, www.cia.org, 01 May 2008
- ^ "Cellulosic Ethanol: Benefits and Challenges. Genomics: GTL". U.S. Department of Energy Office of Science. 2007. Archived from the original on 2007-12-21. Retrieved 2007-12-09.
- ^ "Cellulosic ethanol: fuel of the future?" (PDF). ILSR Daily. 2007. Archived from the original (PDF) on 2006-09-27.
- ^ Sainz MB (June 2009). "Commercial cellulosic ethanol: the role of plant-expressed enzymes". In Vitro Cellular & Developmental Biology-Plant. 45 (3): 314–29. doi:10.1007/s11627-009-9210-1.
- ^ Yang B, Wyman CE (2007). "Pretreatment: the key to unlocking low‐cost cellulosic ethanol". Biofuels, Bioproducts and Biorefining. 2 (1): 26–40. doi:10.1002/bbb.49.
- ^ a b Johnson E (18 Feb 2016). "Integrated enzyme production lowers the cost of cellulosic ethanol". Biofuels, Bioproducts and Biorefining. 10 (2): 164–174. doi:10.1002/bbb.1634.
- ^ Perlack RD (2005). Biomass as feedstock for a bioenergy and bioproducts Industry: the technical feasibility of a billion-ton annual supply. Oak Ridge National Laboratory Report ORNL/TM-2005/66 (Report). Oak Ridge, TN: US Department of Energy.
- ^ Wang GS, Pan XJ, Zhu JY, Gleisner R, Rockwood D (2009). "Sulfite pretreatment to overcome recalcitrance of lignocellulose (SPORL) for robust enzymatic saccharification of hardwoods". Biotechnology Progress. 25 (4): 1086–93. doi:10.1002/btpr.206. PMID 19551888. S2CID 18328577.
- ^ Foody BE, Foody KJ (1991). "Development of an integrated system for producing ethanol from biomass.". In Klass DL (ed.). Energy from Biomass and Waste. Chicago: Institute of Gas Technology. pp. 1225–1243.
- ^ Patel P (9 September 2008). "Better Bug to Make Cellulosic Ethanol: A new strain of bacteria could make cellulosic ethanol cheaper". MIT Technology Review. Archived from the original on 8 June 2011.
- ^ a b Rinehart L (2006). "Switchgrass as a Bioenergy Crop. National Sustainable Agriculture Information Service" (PDF). Archived from the original (PDF) on 2007-07-15. Retrieved 2007-12-10.
- ^ Christian DG, Riche AB, Yates NE (November 2008). "Growth, yield and mineral content of Miscanthus×giganteus grown as a biofuel for 14 successive harvests". Industrial Crops and Products. 28 (3): 320–327. doi:10.1016/j.indcrop.2008.02.009.
- ^ Lugar RG, Woolsey RJ (1999). "The New Petroleum". Foreign Affairs. 78 (1): 88–102. doi:10.2307/20020241. JSTOR 20020241.
- ^ Voegele E (March 9, 2020). "Ethanol Producer Magazine – The Latest News and Data About Ethanol Production". ethanolproducer.com. Retrieved 2021-05-03.
{{cite web}}
: CS1 maint: url-status (link) - ^ "The unlikely, eccentric inventor turning inedible plant life into fuel". 60 Minutes. January 2019.
- ^ Hewage G. "Xyleco: The Next Bio-Based Scam Looking to Cash in on the Sustainability Craze". www.luxresearchinc.com. Retrieved 2021-05-03.
- ^ Lane J (January 2019). "Don't Mess with my Toot Toot: The Zydeco of Xyleco". Biofuels Digest. Retrieved 2021-05-03.
{{cite web}}
: CS1 maint: url-status (link) - ^ "Granbio CEO confirmed investment of 450 million reais in new ethanol …". 2014-06-20.
- ^ "GranBio and NextChem partner to develop cellulosic ethanol market". Green Car Congress. Retrieved 2021-05-03.
- ^ Pernick, Ron and Wilder, Clint (2007). The Clean Tech Revolution p. 96.
- ^ https://www.ethtec.com.au/ethtec-pilot-plant
- ^ http://www.iogen.ca/cellulosic_ethanol/scale-up.html
- ^ https://www.cbc.ca/news/canada/ottawa/ottawa-biofuel-company-iogen-lays-off-150-1.1135219
- ^ Lisa Gibson. Bioethanol plant in Denmark inaugurated Biomass Magazine, November 19, 2009.
- ^ Cellulosic ethanol blend available at filling stations in Denmark Green Car Congress, 28 October 2010.
- ^ Clariant homepage
- ^ Kris Bevill (April 12, 2010). "World's largest cellulosic ethanol plant breaks ground in Italy". Ethanol Producer Magazine.
- ^ https://www.biofuelsdigest.com/bdigest/2018/07/22/biochemtex-beta-renewables-ibp-and-italian-bio-products-to-be-auctioned-off/
- ^ https://www.clariant.com/en/Company/Contacts-and-Locations/Key-Sites/Romania
- ^ "Кировский БиоХимЗавод".
- ^ Cellulosic ethanol Archived 2007-09-28 at the Wayback Machine
- ^ American interest in SEKAB’s cellulosic ethanol technology[permanent dead link ]
- ^ Feasibility Study for Co-Locating and Integrating Ethanol Production Plants from Corn Starch and Lignocellulosic Feedstocks: A Joint Study Sponsored by U.S. Department of Agriculture and U.S. Department of Energy Archived July 15, 2007, at the Wayback Machine January 2005, p. 1.
- ^ Food, Conservation, and Energy Act of 2008
- ^ Biofuels Can Provide Viable, Sustainable Solution To Reducing Petroleum Dependence, Study Shows
- ^ Bevill, Kris (January 20, 2011). "USDA approves loan guarantees for 3 cellulosic projects". Ethanol Producer Magazine.
- ^ Matthew L. Wald (July 6, 2011). "U.S. Backs Project to Produce Fuel From Corn Waste". The New York Times. Retrieved July 7, 2011.
The Energy Department plans to provide a $105 million loan guarantee for the expansion of an ethanol factory in Emmetsburg, Iowa, that intends to make motor fuel from corncobs, leaves and husks.
- ^ "Range Fuels awarded permit to construct the nation's first commercial cellulosic ethanol plant". Range Fuels. 2007-07-02. Archived from the original on 2007-10-12. Retrieved 2007-11-28.
- ^ Kathleen Schalch (2007-11-05). "Georgia plant is first for making ethanol from waste". NPR. Retrieved 2007-11-28.
- ^ "Green-energy plant sucks up subsidies, then goes bust". Archived from the original on 2011-03-08. Retrieved 2011-03-20.
- ^ a b Building Cellulose
- ^ "Permit clears way for Abengoa plant in Hugoton." The Garden City Telegraph. September 21, 2011
- ^ http://biomassmagazine.com/articles/12334/api-announces-temporary-closure-of-alpena-biorefinery
- ^ "DuPont breaks ground at 30 MMgy cellulosic ethanol facility". Ethanol Producer Magazine. November 30, 2012. Retrieved December 15, 2012.
- ^ "VERBIO acquires cellulose ethanol plant from DuPont in Nevada/Iowa, USA". 2018-11-08.
- ^ Ethanol From Switch Grass Deemed Feasible
- ^ ""Grass gas" shows promise as super efficient, clean fuel". Archived from the original on 2008-03-21. Retrieved 2008-01-12.
External links
- List of U.S. Ethanol Plants
- Cellulosic Ethanol Path is Paved With Various Technologies
- The Transition to Second Generation Ethanol
- USDA & DOE Release National Biofuels Action Plan
- Commercializing Cellulosic Ethanol
- Cellulosic ethanol output could "explode"
- Poet Producing Cellulosic Ethanol on Pilot Scale
- More U.S. backing seen possible for ethanol plants
- Shell fuels cellulosic ethanol push with new Codexis deal
- Enerkem to build cellulosic ethanol plant in U.S.
- Ethanol Production Could Reach 90 Billion Gallons by 2030 | backed by Sandia National Laboratories and GM Corp.
- Sandia National Laboratories & GM study: PDF format from hitectransportation.org
- Switchgrass Fuel Yields Bountiful Energy.
- Ethanol From Cellulose: A General Review — P.C. Badger, 2002
- US DOEOffice of Biological and Environmental Research (OBER).
- National Renewable Energy Laboratory, Research Advances – Cellulosic Ethanol.
- USDA Forest Products Laboratory
- reuters.com, New biofuels to come from many sources: conference, Fri Feb 13, 2009 2:50pm EST
- reuters.com, U.S. weekly ethanol margins rise to above break even, Fri Feb 13, 2009 4:01pm EST
- wired.com, One Molecule Could Cure Our Addiction to Oil, 09.24.07
Further reading
- Mansoori GA, Enayati N, Agyarko LB (2016). Energy: Sources, Utilization, Legislation, Sustainability, Illinois as Model State. World Sci. Pub. Co. doi:10.1142/9699. ISBN 978-981-4704-00-7.