Concrete

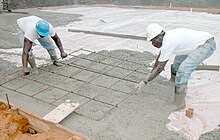
In construction, concrete is a composite building material made from the combination of aggregate and cement binder.
The most common form of concrete is Portland cement concrete, which consists of mineral aggregate (generally gravel and sand), Portland cement and water. Contrary to common belief, concrete does not solidify from drying after mixing and placement. Instead, the cement hydrates, gluing the other components together and eventually creating a stone-like material. When used in the generic sense, this is the material referred to by the term concrete. Concrete is used to make pavements, building structures, foundations, motorways/roads, overpasses, parking structures, brick/block walls and bases for gates, fences and poles. Concrete is used more than any other man-made material on the planet, with water being the only substance on Earth we utilize more. As of 2005 over six billion tons of concrete are made each year, amounting to the equivalent of one ton for every person on Earth, and powers a 35 billion dollar industry which employs over two million workers in the United States alone. Over 55,000 miles of freeways and highways in America are made of this material. An old name for concrete is liquid stone.
However, asphalt concrete is strictly speaking a form of concrete as well.
History
The Assyrians and Babylonians used clay as cement in their concretes. The Egyptians used lime and gypsum cement. In the Roman Empire, cements made from pozzolanic ash/pozzolana and an aggregate made from pumice were used to make a concrete very similar to modern portland cement concrete. In 1756, British engineer John Smeaton pioneered the use of portland cement in concrete, using pebbles and powdered brick as aggregate. In the modern day, the use of recycled/reused materials as concrete ingredients is gaining popularity due to increasingly stringent environmental legislation. The most conspicuous of these is pulverized fuel ash, recycled from the ash by-products of coal power plants. This has a significant impact in reducing the amount of quarrying and the ever-attenuating landfill space.
Characteristics
During hydration and hardening, concrete needs to develop certain physical and chemical properties, among others, mechanical strength, low permeability to ingress of moisture, and chemical and volume stability. Concrete has relatively high compressive strength, but significantly lower tensile strength (about 10% of the compressive strength). As a result, concrete always fails from tensile stresses - even when loaded in compression. The practical implication of these facts is that concrete elements that are subjected to tensile stresses must be reinforced. To illustrate this difference in compressive and tensile strength for unreinforced concrete one only has to imagine a 10' x 10' section of concrete 4 inches thick suspended on its edges. This section of concrete would be unable to support its own weight and would crack in two. Concrete is most often constructed with the addition of steel bar or fiber reinforcement. The reinforcement can be by bars (rebars), mesh, or fibres to produce reinforced concrete. Concrete can also be prestressed (reducing tensile stress) using steel cables, allowing for beams or slabs with a longer span than is practical with reinforced concrete.
The ultimate strength of concrete is related to water/cement ratio, the proportion and type of cement to fillers, and the size, shape, and strength of the aggregate used. Concrete with lower water/cement ratio (down to 0.35) makes a stronger concrete than a higher ratio. Concrete made with smooth pebbles is weaker than that made with rough-surfaced broken rock pieces for example, pebbles require more bonding material (Cement) per area than larger rock, which has less surface area to bond than the smaller "pea gravel".
Certain shapes are very strong in compression, such as arches and vaults, and are therefore preferred for concrete construction. A structural member such as a bridge beam may have a moment ( a bend ) placed in it by tensioning the steel ( wire or cable ) which keeps the beam in compression even when carrying a load.
Cracking
Concrete is placed in a wet or plastic state, and therefore can be manipulated and molded as needed. Hydration and hardening of concrete may lead to tensile stresses at a time when it has not yet gained significant strength, resulting in shrinkage cracks. Extending the period concrete stays damp during curing increases its strength. Minimizing stress prior to curing minimizes cracking. High early strength concrete is designed to cure faster and thus can be stressed earlier than other concretes.
Cracking may start out as micro cracking, thus not readily appparent.
Freezing of concrete (such as in cold climates) before the curing is complete will interrupt the hydration process, reducing the concrete strength and leading to scaling and other damage or failure.
Concrete can be sampled and tested off site for strength. Such tests may use hydraulic ram compression.

Additives
Additives are organic or non-organic materials in form of solids or fluids that are added to the concrete to give it certain characteristics. In normal use the additives make up less than 5% of the cement weight. The most used types of additives are:
- Accelerators: Speed up the hydration (strengthening) of the concete.
- Retarders: Slow the hydration of concrete.
- Air-entrainers: Add and distribute air to the concrete.
- Plasticizers: Increase the workability of concrete.
- Liquid Colors: Changes the color of concrete for aesthetics.
Workability
Workability is the ability of a fresh (plastic) concrete mix to fill the form/mould properly with the desired work (vibration) and without reducing the concrete's quality. Workability depends on water content, additives, aggregate (shape and size distribution) and age (level of hydration). Raising the water content or adding plasticizer will increase the workability. Too much water will lead to bleeding (loss of water) and/or segregation (concrete starts to get heterogeneous) and the resulting concrete will have reduced quality.
Workability is normally tested by slump measurement. High flow concrete, like self compacting concrete, are normally tested by one of several flow measuring methods.
Concrete slump is a simplistic measure of fresh (plastic) concrete's workability. Slump is normally determined by the ASTM C 143 or EN 12350-2 slump test standards, using the Abrams cone, into which concrete is placed for testing. When the cone is carefully lifted off the enclosed material, it will slump a certain amount due to its water content. A relatively dry sample will slump very little, and be given a slump of one or two inches (25 or 50 mm), while a relatively wet concrete sample may slump as much as six or seven inches (150 to 175 mm).
To increase the slump, the rule of thumb is:
- US units
- Add 1 US gallon of water per cubic yard of concrete in the mixer truck to increase slump by 1 inch. Adding 27 US gallons to 9 cubic yards of batched concrete will therefore increase the slump by about 3 inches.
- Metric units (converted from US rule of thumb)
- Add 2 litres of water per cubic metre of concrete in the mixer truck to increase slump by 1 cm. Adding 60 litres to 10 cubic metres of batched concrete will therefore increase the slump by about 3 cm.
Slump can also be increased by adding a plasticizer, without changing the water/cement ratio.
Self compacting concretes
During the 1980s a number of countries including Japan, Sweden and France developed a range of concretes that were self-compacting. These 'SCC's are characterised by their extreme fluidity (using plasticizers), behaving more like water than the traditional viscous concrete.
SCCs are characterized by
- extreme fluidity measured by flow or slump, typically measured between 700-750 mm.
- no need for vibrators to compact the concrete, which can be noisy
- no or little need for expensive concrete pumping equipment
- no bleed water (excess water draining out of the concrete)
SCC can offer benefits of up to 50% in labour costs, due to it being poured up to 80% faster and having reduced wear and tear on formwork.
As of 2005, self compacting concretes account for 10-15% of concrete sales in some European countries.
Shotcrete / sprayed concrete
Main article: Shotcrete
Shotcrete uses compressed air to shoot (cast) concrete to a frame or structure. Shotcrete is mostly used for rock support, especially in tunnelling. Today there are two application methods for shotcrete: the dry-mix and the wet-mix procedure. In Dry-mix the dry mixture of cement and aggregates is filled into the machine and conveyed with compressed air through the hoses. The water needed for the hydration is added at the nozzle. In Wet-mix the mixes are prepared with all necessary water for hydration. The mixes are pumped through the hoses. At the nozzle compressed air is added for spraying. For both methods additives such as plasticizers and accelerators may be used. Shotcrete is normally reinforced by fibers.
See also
- Building construction
- Concrete mixer
- Concrete recycling
- Concrete resurfacing
- Reinforced concrete
- Slab-on-grade foundations
- Shotcrete
- Formwork
- Mortar (masonry)
- Litracon
External link
- History of Concrete
- EcoSmart Concrete A non-profit organization dedicated to reduce the GHG signature of concrete.