Warehouse
This article needs additional citations for verification. (March 2009) |
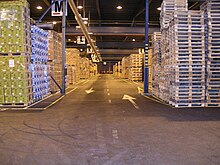
A warehouse is a commercial building for storage of goods. Warehouses are used by manufacturers, importers, exporters, wholesalers, transport businesses, customs, etc. They are usually large plain buildings in industrial areas of cities and towns. They usually have loading docks to load and unload goods from trucks. Sometimes warehouses load and unload goods directly from railways, airports, or seaports. They often have cranes and forklifts for moving goods, which are usually placed on ISO standard pallets loaded into pallet racks.
Nature of goods stored
Stored goods can include any raw materials, components, or finished goods associated with agriculture, manufacturing, or commerce.
Types of warehouse storage systems

Some of the most common warehouse storage systems are:
- Pallet rack including selective, drive-in, drive-thru, double-deep, pushback, and gravity flow
- Mezzanine including structural, roll formed, rack supported, and shelf supported
- Cantilever Rack including structural and roll formed
- Industrial Shelving including metal, steel, wire, and catwalk
- Automated Storage and Retrieval System (ASRS) including vertical carousels, vertical lift modules, horizontal carousels, robotics, mini loads, and compact 3D
Processes and IT
Major warehousing processes include:
- Receiving
- Put away
- Order preparation / picking
- Shipping
- Inventory management (cycle counting, addressing...)
Warehouses frequently provide services, such as:
- Co-packing
- Kitting
- Repair
A piece pick, also known as broken case pick, split-case pick, each pick, over-pack or pick/pack, is a type of order selection process where product is picked and handled in individual units and placed in an outer carton, tote or other container before shipping. Catalog companies and internet retailers are examples of predominantly piece-pick operations. Their customers rarely order in pallet or case quantities; instead, they typically order just one or two pieces of one or two items.
Material direction and tracking in a warehouse can be coordinated by a Warehouse Management System (WMS), a database driven computer program. Logistics personnel use the WMS to improve warehouse efficiency by directing putaways and to maintain accurate inventory by recording warehouse transactions.
Automation and optimization
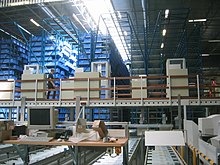
Some warehouses are completely automated, and require no workers inside. Pallets and product move on a system of automated conveyors, cranes and automated storage and retrieval systems coordinated by programmable logic controllers and computers running logistics automation software. These systems are often installed in refrigerated warehouses where temperatures are kept very cold to keep product from spoiling, and also where land is expensive, as automated storage systems can use vertical space efficiently. These high-bay storage areas are often more than 10 meters (33 feet) high, with some over 20 meters (65 feet) high.
For a warehouse to function efficiently, the facility must be properly slotted. Slotting addresses which storage medium a product is picked from (pallet rack or carton flow), and how they are picked (pick-to-light, pick-to-voice, or pick-to-paper). With a proper slotting plan, a warehouse can improve its inventory rotation requirements—such as first in, first out (FIFO) and last in, first out (LIFO)—control labor costs and increase productivity.[1]
Modern trends

Traditional warehousing has declined since the last decades of the 20th century, with the gradual introduction of Just In Time (JIT) techniques. The JIT system promotes product delivery directly from suppliers to consumer without the use of warehouses. However, with the gradual implementation of outsourcing with companies like GlobalTranz, offshore outsourcing and offshoring in about the same time period, the distance between the manufacturer and the retailer (or the parts manufacturer and the industrial plant) grew considerably in many domains, necessitating at least one warehouse per country or per region in any typical supply chain for a given range of products.
Recent retailing trends have led to the development of warehouse-style retail stores. These high-ceiling buildings display retail goods on tall, heavy duty industrial racks rather than conventional retail shelving. Typically, items ready for sale are on the bottom of the racks, and crated or palletized inventory is in the upper rack. Essentially, the same building serves as both warehouse and retail store.
Large exporters/manufacturers use warehouses as distribution points for developing retail outlets in a particular region or country. This concept reduces end cost to the consumer and enhances the production sale ratio.
Internet impact

The internet has had an influence on warehouses. Internet-based stores do not require physical retail space, but still require warehouses to store goods. This kind of warehouse fills many small orders directly from end customers rather than fewer orders of many items from stores.
Having a large and complex supply chain containing many warehouse can be costly. It may be beneficial for a company to have one large warehouse per continent, typically located centrally to transportation. At these continental hubs, goods may be customized for different countries. For example, goods get a price ticket in the language of the destination country. Small, in-warehouse adjustments to goods are called value added services.
See also
- Automated storage and retrieval system
- Inventory
- Inventory management software
- Kiva Systems—a manufacturer of robots for warehouse automation
- Pick and pack
- RFID
- Shipping list
- Voice Directed Warehousing
- Warehouse management system
References
- ^ Effectively Slotting a Warehouse or Distribution Center by By Paul Hansen and Kelvin Gibson. Cygnus Supply and Demand Chain Executive. Accessed 2010-08-06.