Bicycle brake

A bicycle brake is used to slow down or stop a bicycle. There have been various types of brake used throughout history, and several are still in use today. The three main types are: rim brakes, disc brakes, and drum brakes.
Most bicycle brake systems consist of three main components: a mechanism for the rider to apply the brakes, such as brake levers or pedals; a mechanism for transmitting that signal, such as Bowden cables, hydraulic hoses, rods, or the bicycle chain; and the brake mechanism itself, a calliper or drum, to press two or more surfaces together in order to convert, via friction, kinetic energy of the bike and rider into thermal energy to be dissipated.
History
The earliest bicycles with pedals such as the boneshaker were fitted with a spoon brake which pressed onto the rear wheel.[1] The brake was operated by a lever or by a cord connecting to the handlebars. The rider could also slow down by resisting the pedals of the fixed wheel drive.
The next development of the bicycle, the penny-farthings, were similarly braked with a spoon brake or by back pedalling. During its development from 1870 to 1878, there were various designs for brakes, most of them operating on the rear wheel. However, as the rear wheel became smaller and smaller, with more of the rider's weight over the front wheel, braking on the rear wheel became less effective. The front brake, introduced by John Kean in 1873, had been generally adopted by 1880 because of its greater stopping power.[2]
Some penny-farthing riders used only back pedalling and got off and walked down steep hills, but most also used a brake.[1] Having a brake meant that riders could coast down hill by taking their feet off the pedals and placing the legs over the handlebars, although most riders preferred to dismount and walk down steep hills.[2] Putting the legs under the handlebars with the feet off the pedals placed on foot-rests on the forks had resulted in serious accidents caused by the feet getting caught in the spokes.[1]
An alternative to the spoon brake for penny-farthings was the calliper brake patented by Browett and Harrison in 1887.[3] This early version of calliper braking used a rubber block to contact the outside of the penny-farthing's small rear tyre.
The 1870s and 1880s saw the development of the safety bicycle which roughly resembles bicycles today, with two wheels of equal size, initially with solid rubber tyres. These were typically equipped with a front spoon brake and no rear brake mechanism, but like penny-farthings they used fixed gears, allowing rear wheel braking by resisting the motion of the pedals. The relative fragility of the wooden rims used on most bicycles still precluded the use of rim brakes.[citation needed] In the late 1890s came the introduction of rim brakes and the freewheel.[1]
With the introduction of mass-produced pneumatic tyres by the Dunlop Tyre Company, the use of spoon brakes began to decline, as they tended to quickly wear through the thin casing of the new tyres.[citation needed] This problem led to demands for alternative braking systems. On November 23, 1897, Abram W. Duck of Duck's Cyclery in Oakland, California was granted a patent for his Duck Roller Brake (U.S. Patent 594,234).[4] The duck brake used a rod operated by a lever on the handlebar to pull twin rubber rollers against the front tyre, braking the front wheel.[5]
In 1898, after the advent of freewheel coasting mechanisms, the first internal coaster brakes were introduced for the rear wheel. The coaster brake was contained in the rear wheel hub, and was engaged and controlled by backpedaling, thus eliminating the issue of tyre wear. In the United States, the coaster brake was the most commonly fitted brake throughout the first half of the 20th century, often comprising the only braking system on the bicycle.
Brake types
Spoon brakes
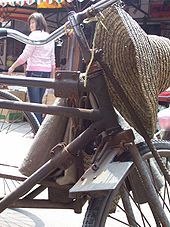
The spoon brake, or plunger brake was probably the first type of bicycle brake and precedes the pneumatic tyre.[6] Spoon brakes were used on penny farthings with solid rubber tyres in the 1800s and continued to be used after the introduction of the pneumatic-tyred safety bicycle. The spoon brake consists of a pad (often leather) or metal shoe (possibly rubber faced), which is pressed onto the top of the front tyre. These were almost always rod-operated by a right-hand lever. In developing countries, a foot-operated form of the spoon brake sometimes is retrofitted to old rod brake roadsters. It consists of a spring-loaded flap attached to the back of the fork crown. This is depressed against the front tyre by the rider's foot.
Perhaps more so than any other form of bicycle brake, the spoon brake is sensitive to road conditions and increases tyre wear dramatically.
Though made obsolete by the introduction of the duck brake, coaster brake, and rod brake, spoon brakes continued to be used in the West supplementally on adult bicycles until the 1930s, and on children's bicycles until the 1950s. In the developing world, they were manufactured until much more recently.
Duck Brake
Invented in 1897, the duck brake, aka Duck Roller Brake used a rod operated by a lever on the handlebar to pull twin friction rollers (usually made of wood or rubber) against the front tyre.[5] Mounted on axles secured by friction washers and set at an angle to conform to the shape of the tyre, the rollers were forced against their friction washers upon contacting the tyre, thus braking the front wheel.[5] A tension spring held the rollers away from the tyre except when braking.[5] Braking power was enhanced by an extra-long brake lever mounted in parallel with and behind the handlebar, which provided additional leverage when braking (two hands could be used to pull the lever if necessary).[5] Used in combination with a rear coaster brake, a cyclist of the day could stop much more quickly and with better modulation of braking effort than was possible using only a spoon brake or rear coaster brake.[7][8] Known colloquially as the duck brake, the design was used by many notable riders of the day, and was widely exported to England, Australia, and other countries.[9] In 1902, Louis H. Bill was granted a patent for an improved version of the Duck Roller Brake (Patent 708,114) for use on motorized bicycles (motorcycles).[10][11]
Rim brakes
Rim brakes are so called because braking force is applied by friction pads to the rim of the rotating wheel, thus slowing it and the bicycle. Brake pads can be made of leather, rubber or cork and are mounted in metal "shoes". Rim brakes are typically actuated by the rider squeezing a lever mounted on the handlebar.
Advantages and disadvantages

Rim brakes are cheap, light, mechanically simple, easy to maintain, and powerful. However, they perform poorly when the rims are wet. This problem is less serious with rims made of aluminium than on those with steel or chromed rims. Rim brakes are also prone to clogging with mud, particularly when mountain biking.
Rim brakes require regular maintenance. Brake pads wear down and have to be replaced. Over longer time and use, rims become worn. Rims should be checked for wear periodically as they can fail catastrophically if the braking surface becomes too worn. Wear is accelerated by wet and muddy conditions. Some type of rim brakes e.g. dual pivot, require that the rim be relatively straight; if the rim has a pronounced wobble, then either the brake pads rub against it when the brakes are released, or apply insufficient or uneven pressure to the rim.
Rim brakes also heat the rim because the brake functions by converting kinetic energy into thermal energy. In normal use this is not a problem, as the brakes are applied with limited force and for a short time, so the heat quickly dissipates to the surrounding air. However, on a heavily-laden bike on a long descent, heat energy is added more quickly than it can dissipate and temperature at the rim and its enclosed tube can increase tire pressure so much that the tire blows off the rim. If this happens on the front wheel, a serious accident is almost inevitable. The risk can be reduced by using both brakes,[12] or by fitting a drag brake.
Although becoming superseded by disc brakes on off-road machines, rims with a hard, rough ceramic coating on the braking surface are available. This coating significantly reduces rim wear and can also improve both wet and dry braking provided appropriate pads are used. It also reduces heat transfer to the air in the tire because the ceramic coating, although thin, is a thermal insulator.[citation needed]
Brake pads
There are many designs of brake pads (brake blocks). Most consist of a replaceable rubber pad held in a metal channel (brake shoe), with a post or bolt protruding from the back to allow attachment to the brake. Some are made as one piece with the attachment directly molded in the pad for lower production costs; brake pads of the cartridge type are held in place by a metal split pin or threaded grub screw and can be replaced without moving the brake shoe from its alignment to the rim. The rubber can be softer for more braking force with less lever effort, or harder for longer life. The rubber can also contain abrasives for better braking, at the expense of rim wear. Compounds vie for better wet braking efficiency. Typically pads are relatively short, but longer varieties are also manufactured to provide more surface area for braking; these often must be curved to match the rim. A larger pad does not give more friction but wears more slowly, so a new pad can be made thinner, simplifying wheel removal with linear-pull brakes in particular. In general, a brake can be fitted with any of these many varieties of pads, as long as the pad mounting method is compatible. Carbon-fiber rims, as on some disc wheels, generally have to use non-abrasive cork pads.
Ceramic-coated rims should be used with special pads because of heat build-up at the pad-rim interface; standard pads can leave a "glaze" on the ceramic braking surface, reducing its inherent roughness and leading to a severe drop in wet-weather braking performance. Kool-Stop, Mavic and Swisstop make "ceramic" pads, which contain substances such as chromium to improve heat tolerance.
Types of rim brakes
The following are among the many sub-types of rim brakes:[13]
Rod-actuated brakes
The rod-actuated brake, or simply rod brake, uses a series of rods and pivots, rather than Bowden cables, to transmit force applied to a hand lever to pull friction pads upwards against the inner surface, which faces the hub, of the wheel rim. They were often called stirrup brakes due to their shape. Rod brakes are used with a rim profile known as the Westwood rim, which has a slightly concave area on the braking surface and lacks the flat outer surface required by brakes that apply the pads on opposite sides of the rim.
The rear linkage mechanism is complicated by the need to allow rotation where the fork and handlebars attach to the frame. A common setup was to combine a front rod brake with a rear coaster brake. Although heavy and complex, the linkages are reliable and durable and can be repaired or adjusted with simple hand tools. The design is still in use, typically on African and Asian roadsters such as the Sohrab and Flying Pigeon.
The calliper brake design
The calliper brake is a class of cable-actuated brake in which the brake mounts to a single point above the wheel, theoretically allowing the arms to auto-centre on the rim. Arms extend around the tyre and end in brake shoes that press against the rim. While some designs incorporate dual pivot points — the arms pivot on a sub-frame — the entire assembly still mounts to a single point.
Calliper brakes tend to become less effective as tyres get wider, and so, deeper, reducing the brakes' mechanical advantage. Thus calliper brakes are rarely found on modern mountain bikes. But they are almost ubiquitous on road bikes, particularly the dual-pivot side-pull calliper brake.
Side-pull calliper brakes

Single-pivot side-pull calliper brakes consist of two curved arms that cross at a pivot above the wheel and hold the brake pads on opposite sides of the rim. These arms have extensions on one side, one attached to the cable, the other to the cable housing. When the brake lever is squeezed, the arms move together and the brake pads squeeze the rim.
These brakes are simple and effective for relatively narrow tyres but have significant flex and resulting poor performance if the arms are made long enough to fit wide tyres. Low-quality varieties also tend to rotate to one side during actuation and to stay there, so that one brake pad continually rubs the rim. These brakes are now used on inexpensive bikes; before the introduction of dual-pivot calliper brakes they were used on all types of road bikes.
Dual-pivot side-pull calliper brakes are used on most modern racing bicycles. One arm pivots at the centre, like a side-pull; and the other pivots at the side, like a centre-pull. The cable housing attaches like that of a side-pull brake.
The centring of side-pull brakes was improved with the mass-market adoption of dual-pivot side-pulls (an old design re-discovered by Shimano in the early 1990s). These brakes offer a higher mechanical advantage, and resulting better braking. Dual-pivot brakes are slightly heavier than conventional side-pull callipers and cannot accurately track an out-of-true rim.
Centre-pull calliper brakes

Centre-pull calliper brakes have symmetrical arms and as such centre more effectively. The cable housing attaches to a fixed cable stop attached to the frame, and the inner cable bolts to a sliding piece (called a "braking delta", "braking triangle", or "yoke") or a small pulley, over which runs a straddle cable connecting the two brake arms. Tension on the cable is evenly distributed to the two arms, preventing the brake from taking a "set" to one side or the other.
These brakes were reasonably priced, and in the past filled the price niche between the cheaper and the more expensive models of side-pull brakes.
U-brakes

U-brakes (also known by the trademarked term "990-style") are essentially the same design as the centre-pull calliper brake. The difference is that the two arm pivots attach directly to the frame or fork while those of the centre-pull calliper brake attach to an integral bridge frame that mounts to the frame or fork by a single bolt. Like roller cam brakes, this is a first-class cantilever design with pivots located above the rim. Thus U-brakes are often interchangeable with, and have the same maintenance issues as, roller cam brakes.
U-brakes were used on mountain bikes through the early 1990s, particularly in the then-popular under-the-chainstays rear location.[14]
They are the current standard on Freestyle BMX frames and forks. The U-brake's main advantage over cantilever and linear-pull brakes in this application is that sideways protrusion of the brake and cable system is minimal, and the exposed parts are smooth. This is especially valuable on freestyle BMX bikes where any protruding parts are susceptible to damage and may interfere with the rider's body.
The cantilever brake design
The cantilever brake is a class of brake in which each arm is attached to a separate pivot point on one side of the seat stay or fork. Thus all cantilever brakes are dual-pivot. Both first- and second-class lever designs exist; second-class is by far the most common. In the second-class lever design, the arm pivots below the rim. The brake shoe is mounted above the pivot and is pressed against the rim as the two arms are drawn together. In the first-class lever design, the arm pivots above the rim. The brake shoe is mounted below the pivot and is pressed against the rim as the two arms are forced apart.
Cantilever brakes are preferred for bicycles that use wide tyres, such as those on mountain bikes. (Standard calliper brakes are problematic in these applications since the long distance from the pivot to the pad reduces mechanical advantage and allows the arms to flex, reducing braking effectiveness.) Because the arms move only in their designed arcs, the brake shoe must be adjustable in several planes. Thus cantilever brake shoes are notoriously difficult to adjust. As the brake shoes of a second-class cantilever brake wears, they ride lower on the rim. Eventually, one may go underneath the rim, inactivating the brake.
There are several brake types based on the cantilever brake design: cantilever brakes and direct-pull brakes - both second class lever designs - and roller cam brakes and U-brakes - both first class lever designs.
Traditional cantilever brakes
The traditional cantilever brake, or commonly cantilever brake, pre-dates the direct-pull brake. It is a centre-pull cantilever design with an outwardly-angled arm protruding on each side, a cable stop on the frame or fork to terminate the cable housing, and a straddle cable between the arms similar to centre-pull calliper brakes. The cable from the brake lever pulls upwards on the straddle cable, causing the brake arms to rotate up and inward thus squeezing the rim between the brake pads.
Traditional cantilever brakes are difficult to adapt to bicycle suspensions and protrude somewhat from the frame. Accordingly they are usually found only on bicycles without suspension.
V-brakes

Linear-pull brakes or direct-pull brakes, commonly referred to by Shimano's trademark V-brakes, are a side-pull version of cantilever brakes and mount on the same frame bosses. However, the arms are longer, with the cable housing attached to one arm and the cable to the other. As the cable pulls against the housing the arms are drawn together. Because the housing enters from vertically above one arm yet force must be transmitted laterally between arms, the flexible housing is extended by a rigid tube with a 90° bend known as the "noodle". The noodle seats in a stirrup attached to the arm. A flexible bellows often covers the exposed cable.[15]

Since there is no intervening mechanism between the cable and the arms, the design is called "direct-pull". And since the arms move the same distance that the cable moves with regard to its housing, the design is also called "linear-pull". The term "V-brake" is trademarked by Shimano and represents the most popular implementation of this design.
V-brakes function well with the suspension systems found on many mountain bikes because they do not require a separate cable stop on the frame or fork. Because of the higher mechanical advantage of V-brakes, they require brake levers with longer cable travel than levers intended for older types of brakes. Mechanical (i.e. cable-actuated) disc brakes use the same amount of cable travel as V-brakes, except for those that are described as being "road" specific. (See Actuation mechanisms below.) As a general rule, mechanical disc brakes for so-called "flat bar" bicycles (chiefly mountain and hybrid bicycles) are compatible with V-brake levers, whereas mechanical disc brakes intended for "drop-bar" bicycles are compatible with the cable pull of older brake designs (cantilever, calliper, and U-brake).
Cheap or poorly-specified V-brakes can suffer from a sudden failure when the noodle end pulls through the metal stirrup, leaving that wheel with no braking power whatsoever. Although the noodle can be regarded as a service item and changed regularly, the hole in the stirrup may enlarge through wear. The stirrup cannot normally be replaced, so good quality V-brakes use a hard and tough steel for the stirrup.[16]
Roller cam brakes
Roller cam brakes are centre-pull cantilever brakes actuated by the cable pulling a single two-sided sliding cam. (First and second-class lever designs exist; first-class is most common and is described here.) Each arm has a cam follower. As the cam presses against the follower it forces the arms apart. As the top of each arm moves outward, the brake shoe below the pivot is forced inward against the rim.[17] There is much in favor of the roller cam brake design. Since the cam controls the rate of closure, the clamping force can be made non-linear with the pull. And since the design can provide positive mechanical advantage, maximum clamping force can be higher than that of other types of brakes. They are known for being strong and controllable. On the downside, they require some skill to set up and can complicate wheel changes. And they require maintenance: like U-brakes, as the pad wears it strikes the rim higher; unless re-adjusted it can eventually contact the tyre's sidewall.
The roller cam design was first developed by Charlie Cunningham of WTB around 1982 and licensed to Suntour.[18] Roller cam brakes were used on early mountain bikes in the 1980s and into the 1990s, mounted to the head tube and seat stays in the standard locations, and below the chain stays for improved stiffness as they do not protrude to interfere with the crank. It is not unusual for a bicycle to have a single roller cam brake combined with another type. They are still used on some BMX and recumbent bicycles.[19] Note that the common first-class lever roller cam brake is generally not convertible to second-class lever cantilever brake types as the pivots are in different locations.
There are two rare variants that use the roller cam principle. For locations where centre-pull is inappropriate, the side-pull toggle cam brake was developed.[20] Also a first-class cantilever, it uses a single-sided sliding cam (the toggle)[21] against one arm that is attached by a link to the other arm. As the cam presses against the (single) follower, the force is also transmitted to the other arm via the link. And specifically for suspension forks where the housing must terminate at the brake frame, the side-pull sabre cam brake was developed.[22] In the sabre cam design, the cable end is fixed and the housing moves the single-sided cam.
Delta brakes

The delta brake is a road bicycle brake named due to its triangular shape. The cable enters at the centre, pulls a corner of a parallelogram linkage housed inside the brake across two opposite corners, pushing out at the other two corners on to the brake arms above the pivots, so that the arms below the pivots push pads in against the rim. A notable feature of the design is that the mechanical advantage varies as a tangent function across its range, where that of most other designs remains fixed.[23]
Many consider the brake attractive, and it has a lower wind profile than some other common brakes. However, Bicycle Quarterly criticized the delta brake for being heavy, giving mediocre stopping power, and suffering disadvantageous variable mechanical advantage.[24] In particular, with a small parallelogram, pad wear causes mechanical advantage to rise dramatically. However, with high leverage, the stroke of the lever is not enough to fully apply the brake, so the rider can have brakes that feel normal in light braking but which cannot be applied harder for hard braking.
The basic design dates from at least the 1930s. They were made most prominently by Campagnolo in 1985, but brakes based on the same mechanism were also manufactured by Modolo (Kronos), Weinmann, and others.[25] [26] They are no longer made and are now uncommon.

Hydraulic rim brakes
Hydraulic rim brakes are one of the least common types. These brakes are mounted either on the same pivot points used for cantilever and linear-pull brakes or they can be mounted on four-bolt brake mounts found on many trials frames. They were available on some high-end mountain bikes in the US in the early 1990s, but declined in popularity with the rise of disc brakes. The moderate performance advantage (greater power and control) they offer over cable actuated rim brakes is offset by their greater weight and complexity. The only significant current use of these brakes in the US is on bicycles used for trials riding. In Europe, however, the hydraulic rim brakes manufactured by Magura still enjoy a steady popularity, and remain a viable alternative to disc brakes.
Disc brakes
A disc brake consists of a metal disc attached to the wheel hub that rotates with the wheel. Callipers are attached to the frame or fork along with pads that squeeze together on the disc. As the pads drag against the disc, the wheel - and thus the bicycle - is slowed as kinetic energy (motion) is transformed into thermal energy (heat). (In basic operation, disc brakes are identical to rim brakes.) A bicycle disc brake may be mechanically actuated, as with a Bowden cable, or hydraulically actuated, or a combination of the two.
Disc brakes are used mainly on mountain bikes ridden off-road, but sometimes on hybrid bicycles and touring bicycles. A disc brake is sometimes employed as a drag brake.
Advantages and disadvantages
Disc brakes tend to perform equally well in all conditions including water, mud, and snow due to several factors:
- The braking surface is farther from the ground and possible contaminants like mud which can coat or freeze on the rim and pads.
- Disc brakes are less prone to fading under heavy or prolonged braking compared with rim brakes, and the heat is not dissipated into the tyre.
- Disc brake pads when fully retracted ride much closer to the braking surface than rim brake pads.[27] This better prevents a buildup of water or debris under the pad.
- There are holes in the rotor, providing a path for water and debris to get out from under the pads.
- Wheel rims tend to be made of lightweight metal. Brake discs and pads are harder and can accept higher maximum loads.
- Disc brakes do not create wear on the rim unlike rim brakes, especially if grit becomes embedded in the brake pads.
- Disc brakes permit a bicycle with a buckled wheel to be ridden, which would not be possible with a rim brake since the buckled wheel would bind on the brake pads.
- When riding a mountain bike with rim brakes in thick mud, the first point that the mud builds up is usually on the rim brakes. A mountain bicycle with disc brakes is usually less susceptible to mud buildup provided the rear frame and front fork yoke have sufficient clearance from the wheels.
The use of very wide tyres favours disc brakes, as rim brakes require ever-longer arms to clear the wider tyre. Longer arms tend to flex more, degrading braking. Disc brakes are unaffected by tyre width.
Unlike some rim brake designs, disc brakes are compatible with front and rear suspension.
Disc brake assemblies are heavier than rim brakes, and are generally more expensive.
Disc brakes require a hub built to accept the disc. Front hubs designed for discs often move the left hub's flange inward to make room for the disc, which causes the wheel to be dished. A dished wheel is laterally weaker when forced to the non-disc side. Other hubs use conventional flange spacing and provide a wheel without dish, but require a less common wide-spaced fork.
A rim brake works directly on the rim and the attached tyre; a disc brake applies a potentially large torque moment at the hub. The latter has two main disadvantages:
- The torque moment must be transmitted to the tyre through the wheel components: flanges, spokes, nipples, and rim spoke bed. Engineering for this moment inevitably leads to a heavier wheel.
- A front disc brake places a bending moment on the fork between the calliper anchor points and the tip of the dropout. In order to counter this moment and to support the anchor points and weight of the calliper, the fork must be thicker and heavier.[28]
The heavier fork and wheels compound the weight disadvantage of the brake assembly itself.
Disc brakes are sensitive to lateral play or "slop", so careful manufacture and adjustment is required. Hub bearing wear is an issue with disc brakes.[citation needed]
While all types of brakes will eventually wear out the braking surface, a brake disc is easier and cheaper to replace than a wheel rim or drum.
While a disc brake does not heat the rim as does a rim brake, excessive heat build up can also lead to failure with disc brakes. If brake friction exceeds convection and radiation losses, the temperature of the disc can quickly rise to where the metal weakens, causing the disc to warp or crack. (With hydraulic actuation, brake fluid may boil. See Actuation mechanisms below.)
The design and positioning of disc brakes can interfere with pannier racks not designed for them. For this reason, many manufacturers produce "disc" and "non-disc" versions.
Since about 2003, riders have reported a dangerous problem using disc brakes: under hard braking, the front wheel comes out from the dropouts. The problem occurs where the brake pads and dropouts are aligned so the brake reaction force tends to eject the wheel from the dropout. Under repeated hard braking, the axle moves in the dropout in a way that unscrews the quick release. Riders should make sure the skewers are properly tightened before riding.[29][30] Forks that use different brake/dropout orientations or through-axles are not subject to this problem.
Hydraulic vs. mechanical
There are two main types of disc brake: mechanical (cable-actuated) and hydraulic. For more details on this topic, see Actuation mechanisms.
The advantages of mechanically actuated disc brakes are in their lower cost, lower maintenance, and lighter system weight. Additionally, mechanically actuated disc brakes also have another potential advantage: they are traditionally the only type of disc brake that can be used with drop handlebars,[31] however prototype drop bar hydraulic conversion components have been developed.[32]
Single vs dual actuation
Many disc brakes have their pads actuated from both sides of the calliper, while some have only one pad that moves. Dual actuation can move both pads relative to the calliper, or can move one pad relative to the calliper, then move the calliper and other pad relative to the rotor, called a "floating calliper" design. Single-actuation brakes use either a multi-part rotor that floats axially on the hub, or bend the rotor sideways as needed. Bending the rotor is theoretically inferior, but in practice gives good service, even under high-force braking with a hot disc, and can also yield more progressiveness (which is generally sought after for the rear brake).[citation needed]
Self-adjusting
Many hydraulic disc brakes have a self-adjusting mechanism so as the brake pad wears, the pistons keep the distance from the pad to the disc consistent to maintain the same brake lever throw. Some hydraulic brakes, especially older ones, and most mechanical discs have manual controls to adjust the pad-to-rotor gap. Typically, several pad adjustments are needed during the life of the pads.
Multi-part construction
Hydraulic callipers are typically made in one piece to reduce weight, increase stiffness and reduce leaks. The two-piece design reduces heat build-up more effectively.[citation needed] Many older brakes and high-performance models use a two-piece calliper, where the two parts are bolted together. Many mechanical disc brake callipers are two-piece, notably the popular Avid BB-5 and BB-7 brakes.
Multiple pistons
Many high-performance callipers use two or three pistons per side; lower-cost and lower-performance callipers often have only one per side. Using more pistons allows a larger piston area and thus increased leverage with a given master cylinder. Also, pistons may be of several sizes so pad force can be controlled across the face of the pad, especially when the pad is long and narrow. A long narrow pad may be desired to increase pad area and thus reduce the frequency of pad changes. In contrast, using a single large piston may be heavier to accomplish the same results.
Calliper mounting standards
There are many standards for mounting disc brake callipers. I.S. (International Standard) is different for 160mm and 203mm rotor and differs between forks with a QR and 20 mm through axle. The post-mount standard also differs by disc size and axle type. Many incompatible variants were produced over the years, mostly by fork manufacturers.[citation needed] The mount used on the Rockshox Boxxer is the most typical of these specialty mounts, but most fork manufactures now use either the IS or post-mount standard for their current forks. As a point of reference, Hayes currently sells no fewer than 13 different adapters to fit their brakes to various mounting patterns.[33]
Advantages and disadvantages of various types of mounts
A disadvantage of post mounts is that the bolt is threaded directly into the fork lowers. If the threading is stripped or if the bolt is stuck, then new fork lowers are required. Frame manufacturers have standardized the IS mount for the rear disc brake mount. In recent years post mount has gained ground and is becoming the most common. This is mostly due to decreased manufacturing and part cost for the brake callipers when using post mount.[citation needed] A limitation of the mount is that the location of the rotor disc is more tightly constrained: it is possible to encounter incompatible hub/fork combinations, where the rotor is out of range. With an IS mount, the calliper can be moved closer to or further from the mount point using spacers; this can permit a wider range. [citation needed]
Disc mounting standards
There are many options for disc rotor mounting - International Standard (IS), centerlock, Cannondale's 4-bolt pattern, Hope's 5-bolt pattern and Rohloff's 4-bolt pattern, to name a few. IS is a six-bolt mount and is the industry standard. Centerlock is patented by Shimano and uses a splined interface along with a lockring to secure the disc. The advantages of centerlock are that the splined interface is theoretically stiffer, and removing the disc is quicker because it only requires one lockring to be removed. Some of the disadvantages are that the design is patented requiring a licensing fee from Shimano. A Shimano cassette lockring tool (or an external BB tool in case of through-axle hub) is needed to remove the rotor and is more expensive and less common than a Torx key. Advantages of IS six-bolt are that there are more choices when it comes to hubs and rotors. IS rotors use button head socket cap screws (typically M5x0.8x10mm with locking patch) with either a hex socket or Torx socket to secure them to the hub. This can make IS rotors more time consuming to install and remove. Torx screws are preferred for the superior torque: it is easy to strip the socket of a hex bolt by overtightening it, leaving a rotor that is hard to remove.[citation needed]
Standards
- Centerlock (Shimano proprietary)
- International Standard (IS) (in widespread use) 44mm BCD
- AMP 6-bolt (AMP proprietary, obsolete)
- Cannondale's 4-bolt pattern (obsolete)
- Freewheel thread (used by Mountain Cycles and others; obsolete)
- Hope Technology's 5-bolt pattern (Hope proprietary, obsolete)
- Hope Technology's 3-bolt pattern (Hope proprietary)
- Rohloff's 4-bolt pattern (proprietary, 65mm, same as some chainrings)
- Rock Shox 3-bolt pattern (proprietary, obsolete)
Disc sizes
Disc brake rotors come in many different sizes, typically 160 millimeter, 185 mm, or 203 mm in diameter. However, many other sizes are available as brake manufacturers make discs specific to their callipers — the dimensions often vary by a few millimeters.
Larger rotors provide greater braking force for a given pad pressure, by virtue of a longer moment arm for the calliper to act on.[dubious – discuss] Smaller rotors provide less stopping power but also less weight and better protection from knocks. Larger rotors dissipate heat more quickly and have a larger amount of mass to absorb heat, reducing brake fade or failure. Downhill racers typically run larger brakes to handle the greater braking loads and extended braking duration. Cross country racers typically run smaller rotors which can handle smaller braking loads yet offer a considerable weight savings of as much as 100g per rotor.[34] It is also common to use a larger diameter rotor on the front wheel and a smaller rotor on the rear wheel since the front wheel does the most braking (up to 90% of the total).[35]
With large rotors to dissipate heat, disc brakes are becoming more popular as drag brakes.
Drum brakes

Bicycle drum brakes operate like those of a car, although the bicycle variety use mechanical rather than hydraulic actuation. Two pads are pressed outward against the braking surface on the inside of the hub shell. Shell inside diameters on a bicycle drum brake are typically 70 – 120 mm. Drum brakes have been used on front hubs and hubs with both internal and external freewheels. Both cable- and rod-operated drum brake systems have been widely produced.
A Roller Brake is a modular cable-operated drum brake manufactured by Shimano for use on specially splined front and rear hubs. Unlike a traditional drum brake, the Roller Brake can be easily removed from the hub. Some models contain a torque-limiting device called a power modulator designed to make it difficult to skid the wheel. In practice this can reduce its effectiveness on bicycles with adult-sized wheels.
Drum brakes are most common on utility bicycles in some countries, especially the Netherlands, and are also often found on freight bicycles and velomobiles.
Advantages and disadvantages
Drum brakes provide consistent braking in wet or dirty conditions since the mechanism is fully enclosed.
Brake drums are less susceptible to wear than lightweight wheel rim sidewalls.
Drum brakes are heavier, more complicated, and often weaker than rim brakes, but they require less maintenance. Drum brakes do not adapt well to quick release axle fastening, and removing a drum brake wheel requires the operator to disconnect the brake cable as well as the axle.
Drum brakes have torque arms which must be anchored to the frame or fork of the bicycle, and not all bicycles are constructed to accommodate such fastenings or tolerate their applied forces.
Drum brakes often have a long break-in period during which their braking power increases gradually over the course of hundreds of miles of riding.
Coaster brakes

First invented in 1898, the coaster brake, also known as a back pedal brake or foot brake (contra or torpedo in some countries), is a type of drum brake integrated into hubs with an internal freewheel. Freewheeling functions as with other systems, but when back pedaled, the brake engages after a fraction of a revolution. The coaster brake can be found in both single-speed and internally geared hubs.
When such a hub is pedaled forwards, the sprocket drives a screw which forces a clutch to move along the axle, driving the hub shell or gear assembly. When pedaling is reversed, the screw drives the clutch in the opposite direction, forcing it either between two brake pads and pressing them against the shell, or into a split collar and expanding it against the shell. The braking surface is often steel, and the braking element brass or phosphor-bronze, as in the Birmingham-made Perry Coaster Hub.
Coaster-brake bicycles are generally equipped with a single cog and chain wheel and often use 1/8" wide chain. However, there have been several models of coaster brake hubs with dérailleurs, most notably the Sachs 2x3. These use special extra-short dérailleurs which can stand up to the forces of being straightened out frequently and do not require an excessive amount of reverse pedal rotation before the brake engages. Coaster brakes have also been incorporated into hub gear designs - for example the AWC from Sturmey Archer, and the Shimano Nexus 3-speed.
Advantages and disadvantages
Coaster brakes have the advantage of being protected from the elements and thus perform well in rain or snow. Though coaster brakes generally go years without needing maintenance, they are more complicated than rim brakes to repair if it becomes necessary. Coaster brakes also do not have sufficient heat dissipation for use on long descents, a characteristic made legendary through events such as the 'Repack Downhill' race, where riders almost certainly would need to repack their coaster brakes after the grease melted or smoked due to the heat from lengthy downhill runs.[36] A coaster brake can only be applied when the cranks are reasonably level, limiting how quickly it can be applied. As coaster brakes are only made for rear wheels, they have the disadvantage common to all rear brakes of skidding the wheel easily. This disadvantage may, however, be alleviated if the bicycle also has a hand-lever-operated front brake and the cyclist uses it. Another disadvantage is that the coaster brake is completely dependent on the chain being fully intact. If the chain breaks, the coaster brake provides no braking power whatsoever.
Drag brakes
A drag brake is a type of brake defined by its use rather than by its mechanical design.
A drag brake is intended to provide a constant decelerating force to slow a bicycle on a long downhill rather than to stop it — a separate braking system is used to stop the bicycle. A drag brake is often employed on a heavy bicycle such as a tandem in mountainous areas where extended use of rim brakes could cause a rim to become hot enough to blow out.[37] [38] The typical drag brake has long been a drum brake. The largest manufacturer of this type of brake is Arai, whose brakes are screwed onto hubs with conventional freewheel threading on the left side of the rear hub and operated via Bowden cables. As of 2011, the Arai drum brake has been out of production for several years, with remaining stocks nearing depletion and used units commanding premium prices on internet auction sites.
More recently, large-rotor disc brakes are being used as drag brakes.[39] DT-Swiss make an adapter to mate disk rotors with hubs threaded for the Arai drum brake, but this still leaves the problem of fitting the calliper.
Band brake
A band brake consists of a band, strap, or cable that wraps around a drum that rotates with a wheel and is pulled tight to generate braking friction. Band brakes appeared as early as 1884 on tricycles.[40] Star Cycles introduced a band brake in 1902 on its bicycles with freewheels.[41] Band brakes are still manufactured for bicycles today.[42]
A rim band brake, as implemented on the Yankee bicycle by Royce Husted in the 1990s, consists of a stainless-steel cable, wrapped in a kevlar sheath[disambiguation needed], that rides in a u-shaped channel on the side of the wheel rim. Squeezing the brake lever tightens the cable against the channel to produce braking friction.[43] A return spring slackens the cable when the brake lever is released, no adjustment is required, and the brake becomes more forceful when wet. Husted said his inspiration was the band brake used on industrial machinery.[44] The Yankee bicycle only included a rear brake, but that met U.S. Consumer Product Safety Commission standards.
Actuation mechanisms
The actuation mechanism is that part of the brake system that transmits force from the rider to that part of the system that does the actual braking. Brake system actuation mechanisms are either mechanical or hydraulic.
Mechanical
The primary modern mechanical actuation mechanism uses brake levers coupled to Bowden cables to move brake arms, thus forcing pads against a braking surface. Other mechanical actuation mechanisms exist: see Coaster brakes for back-pedal actuation mechanisms, and Rod-actuated brakes for a mechanism incorporating metal rods.
The first Spoon brakes were actuated by a cable that was pulled by twisting the end of a handlebar.[45]
Hydraulic
Hydraulic brakes also use brake levers to push fluid from a reservoir through a hose to move pistons in a calliper, thus forcing pads against a braking surface. While hydraulic rim brakes exist, today the hydraulic actuation mechanism is identified mostly with Disc brakes.
Two types of brake fluid are used today: mineral oil and DOT fluid. Mineral oil is generally inert, while DOT is corrosive to frame paint but has a higher boiling point. Using the wrong fluid can cause seals to swell or become corroded.[citation needed]
Hybrid
Some older designs, notably the AMP and Mountain Cycles brakes, use a cable from lever to calliper, then use a master cylinder integrated into the piston. Some Santana tandem bicycles used a cable from lever to a master cylinder mounted near the head tube, with a hydraulic line to the rear wheel calliper. Such "hybrid" designs allow the leverage of a hydraulic system while allowing use of cable brake levers, but may be heavier and can suffer from grit intrusion in the standard cable.
Brake levers

Brake levers are usually mounted on the handlebars within easy reach of the rider's hands. They may be distinct from or integrated into the shifting mechanism. The brake lever transmits the force applied by the rider through either a mechanical or hydraulic mechanism.
Bicycles with drop handlebars may have more than one brake lever for each brake to facilitate braking from multiple hand positions. Levers that allow the rider to work the brakes from the tops of the bars, introduced in the '70s, are called extension levers or safety levers.[46] The modern equivalents are called interrupt brake levers and are considered superior.[47]
The mechanical advantage of the brake lever must be matched to the brake it is connected to in order for the rider to have sufficient leverage and travel to actuate the brake. Using mismatched brakes and levers could result in too much mechanical advantage and hence not enough travel to properly actuate the brake (v-brakes with conventional levers) or too little mechanical advantage, requiring a very strong pull to apply the brakes hard (v-brake levers with other types of brake).
Mechanical (cable) brake levers come in two varieties based on the length of brake cable pulled for a given amount of lever movement:[48]
- Standard pull levers work with most brake designs, including calliper brakes, traditional cantilever brakes, and mechanically actuated disc brakes branded for "Road".
- Long pull levers work with "direct-pull" cantilever brakes, such as Shimano "V-Brakes",[49] and mechanically actuated disc brakes branded for "Mountain". Direct-pull levers are generally unsuited for use on drop handlebars.[50]
Adapters are available to allow the use of one type of lever with an otherwise incompatible type of rim brake.[51] Some brake levers have adjustable leverage that can be made to work with either type of brake. Others vary their mechanical advantage as the lever moves to move the pad quickly at first, then provide more leverage once it contact the brake surface.[52]
Hydraulic brake levers move a piston in a fluid reservoir. The mechanical advantage of the lever depends on the brake system design.
Advantages and disadvantages
The cable mechanism is cheaper, but Bowden cables have issues (see here) that are applicable to any braking system incorporating them.
A hydraulic mechanism is closed and so less likely than a cable mechanism to suffer from contamination. Hydraulic brakes rarely fail, but failure tends to be complete. Hydraulic systems require specialized equipment to repair. Hydraulic fluid may boil from excessive heat build up, causing complete brake failure.[53]
Braking technique
There are several techniques for efficient braking on a standard, two-brake bicycle. The one most commonly taught is the 25-75 technique. This method entails supplying 75% of the stopping power to the front brake, and about 25% of the power to the rear. Since the bicycle's deceleration causes a transfer of weight to the front wheel, there is much more traction on the front wheel. Therefore, the rear brake can exert less braking force than on the front before the rear wheel starts skidding. For a more-detailed analysis, see bicycle and motorcycle dynamics.
If too much power is applied to the front brake, then the momentum of the rider propels him/her over the handlebars, thereby flipping the bicycle. The skidding of the rear wheel can serve as a signal to reduce force on the front brake; a skillful cyclist in effect becomes a human anti-lock braking machine, thus they must use both front and back brakes [54]
Some front brakes have a spring that limits the applied force; this is easier to use but limits the braking force and cannot compensate for changes in brake effectiveness due, for example, to a wet rim or overheated brake disc. On tandem bicycles and other long-wheel-base bicycles (including recumbents and other specialized bicycles), the lower relative centre of mass makes it virtually impossible for heavy front braking to flip the bicycle; the front wheel would skid first.[55]
A skillful bicyclist often will use the front brake alone for moderate braking when riding on a good, paved surface. As the front wheel does not skid in those conditions, the front brake poses less risk of loss of control, and does not cause rapid tyre wear.
In some situations, it is advisable to slow down and to use the rear brake more and the front brake less:
- When unfamiliar with the braking characteristics of a bicycle. It is important to test the brakes and learn how much hand force is needed when first riding it.
- When leaning in a turn (or preferably, brake before turning).
- Slippery surfaces, such as wet pavement, mud, snow, ice, or loose stones/gravel. It is difficult to recover from a front-wheel skid on a slippery surface, especially when leaned over.
- Bumpy surfaces: If the front wheel comes off the ground during braking, it will stop completely. Landing on a stopped front wheel with the brakes still applied is likely to cause the front wheel to skid and may flip the rider over the handlebar.
- Very loose surfaces (such as gravel and loose dirt): In some loose-surface situations, it may be beneficial to completely lock up the rear wheel in order to slow down or maintain control. On very steep slopes with loose surfaces where any braking will cause the wheel to skid, it can be better to maintain control of the bicycle by the rear-brake more than one would normally. However neither wheel should stop rotating completely, as this will result in very little control.
- Steep descents : the slope angle makes the front flip more easily reached, and moreover a front-wheel skid would be very difficult to recover (crash highly probable), whereas a rear skid does still drag the bike without losing too much control.
- Wet weather conditions, when the road surfaces are generally more slippery.
- Long descents: alternating the front and back brake can help prevent hand fatigue and overheating of the wheel rims which can cause a disastrous tyre blow-out, or boiling of the hydraulic fluid in case of hydraulic disc brakes.
- Flat front tyre: braking a tyre that has little air can cause the tyre to come off the rim, which is likely to cause a crash.[56]
It is customary to place the front brake lever on the left in right-side-driving countries, and vice versa,[57] because the hand on the side nearer the centre of the road is more commonly used for hand signals, and the rear brake can not pitch the bicyclist forward. However, a skillful bicyclist does better with the front brake on the side that is less often used for hand signals. In an emergency situation, operation of the brake has to be second nature; an unskilled bicyclist could find reversed brake levers confusing. Fortunately, it is usually easy to switch brake cables.
Bicycles without brakes
Track bicycles are built without brakes so as to avoid sudden changes in speed when racing on a velodrome. Since track bikes have a fixed gear, braking can be accomplished by reversing the force on the pedals to slow down, or by locking the pedals and inducing a skid.
Fixed gear road bikes may also lack brakes. Slowing and stopping is accomplished as with a track bike. Many fixed gear bikes are, however, fitted with a front brake for safety reasons, or because it is a legal requirement.
Some BMX bicycles do not have brakes. The usual method of stopping is for the rider to put one or both feet on the ground, or to wedge a foot between the seat and the rear tire, effectively acting as a spoon brake.
In Australia, Germany and the UK, it is illegal to ride a bicycle without brakes on a public road. [58][59][60]
See also
References
- ^ a b c d Nick Clayton (1986). Early Bicycles. Shire publications, Princes Risborough UK. pp. 8–15. ISBN 0-85263-803-5.
- ^ a b Serena Beeley (1992). A History of Bicycles. Studio Editions, London. p. 32. ISBN 1-85170-753-0.
- ^ Hudson, William (2008). "Myths and Milestones in Bicycle Evolution". Jim Langley. Retrieved 2009-09-22.
- ^ Duck, Abram W., United States Patent Office, Letters Patent No. 594,234, November 23, 1897
- ^ a b c d e Duck, Abram W., Patent No. 594,234
- ^ Bicycling Science (2nd ed.), pp.153–154
- ^ Whitt, Frank R. and Wilson, David G., Bicycling Science (2nd ed.), Massachusetts Institute of Technology, (1982), ISBN 0-262-23111-5, pp. 198-233: The spoon brake was fairly ineffective, while the coaster brake did not operate on the front tire, the most effective position on a two-wheel vehicle during a hard stop.
- ^ Parliamentary Debates: Senate and House of Representatives, Tariff Preferences, Volume 34 (19 September 1906), p. 4951
- ^ Parliamentary Debates, p. 4951
- ^ Bill, Louis H., United States Patent Office, Letters Patent No. 708,114, September 2, 1902
- ^ Duck Brake Company, Testimonial of Geo. A. Wyman (1903): George A. Wyman, who crossed the United States aboard a motorized bicycle with a Duck roller brake praised its efficiency, stating that "I controlled my motor[bike] with it on the steepest grades of the Rocky Mountains".
- ^ Forester, John. ""safe" brakes that burn up". Retrieved 2010-06-05.
- ^ Rim brakes have been the subject of countless "engineering innovations". Some of the more unusual results can be seen here [1].
- ^ Brown, p. [2] Adjusting Cantilever Brakes
- ^ Brown, p. [3] Direct-Pull Cantilever Brakes
- ^
Chris Juden (2006). "Check your "V" brakes". CTC - the UK’s national cyclists’ organisation. Retrieved 2010-02-06.
{{cite web}}
: Unknown parameter|month=
ignored (help) - ^ Pictures of a rear and a front roller cam brake.
- ^ Private communication by Jeff Archer of the Museum of Mountain Bike Art & Technology [4]
- ^ Brown 2007, p. [5] Roller-cam Brake
- ^ "Retrobike Gallery and Archive". Retrieved 2009-08-03. Drawings and technical description.
- ^ An example of the toggle integral to the toggle cam brake appears here [6]. The cam surface is the upper edge of the 'tail' on the large central piece. The cable attaches to one of the three holes. Note that the cam must flare at twice the rate of the two-sided roller cam design in order to move the arms the same amount.
- ^ A picture of the rare sabre cam brake may be found at MOMBAT - click on the 2nd thumb from the left.
- ^ Brandt 2005, p. [7] Delta
- ^ Heine 2008, p. 36
- ^ Sutherland, Howard (1995). Sutherlands Handbook for Bicycle Mechanics (6th Edition). Berkley, CA, USA: Sutherland Publications. pp. 13.27 to 13.28. ISBN 0-914578-09-X.
{{cite book}}
: Unknown parameter|coauthors=
ignored (|author=
suggested) (help) - ^ Metz, Joel. "so, you like odd brakes, eh?". Retrieved 2010-02-01.
- ^ Because of the shorter lever arm, a disc brake requires more mechanical advantage between the lever and the pad than a rim brake. But the distance that a brake lever can travel and the amount of force a rider can provide are fixed. The result is that the disc pad is able to move a shorter distance than a rim pad.
- ^ Brandt 2005, p. [8] Disc Brakes
- ^ Sheldon Brown. "Bicycle Glossary: Disc Brake". Retrieved 2011-11-22.
There have been concerns about the safety of front disc brakes, in conjunction with lightweight quick-release skewers.
- ^ Annan, James (2006). "Disk brakes and quick releases - what you need to know". Retrieved 2007-10-19.
{{cite web}}
: Unknown parameter|month=
ignored (help) - ^ Sheldon Brown, quoted at Brandt 2005, p. [9] Disc Brakes
- ^ "CXM Tech Exclusive: Drop Bar Hydraulic Disc Brake Adapter Tested at Nationals | Cyclocross Magazine – Cyclocross News, Races, Bikes, Photos, Videos". Cxmagazine.com. Retrieved 2012-08-17.
- ^ "Mount Bracket Chart 2005" (PDF). Retrieved 2010-06-15.
- ^ "Disc Brake weight listing". Retrieved 2006-11-07.
- ^ Bicycling Science (3rd ed.), p. 245: "The front brake therefore has to provide 90 percent of the total retarding force at a deceleration of 0.5 G ..."
- ^ Charlie Kelly's Repack Page (Repack Downhill bike race)
- ^ Brown 2007, p. [10] Drag Brake
- ^ Brown, p. [11] Brakes for Tandem Bicycles
- ^ Some tandem riders with Avid BB-7 mechanical disc brakes and 203mm rotors report fewer heat problems under heavy braking than when using the previous standard of comparison, an Arai drum used as a "drag" brake.
- ^ "TRICYCLES v BICYCLES predated CARS v MOTORCYCLES". www.triporteurs.co.uk. Retrieved 2010-04-02.
- ^ "Star Bicycles". Wolverhampton Museum of Industry. Retrieved 2010-04-02.
- ^ "Band Brake detailed product information". Cixi Dafeng Bicycle Co., Ltd. Retrieved 2010-04-02.
- ^ "Yankee Bicycle". US Times. Retrieved 2010-04-02.
- ^ Stuart F. Brown (August 1991). "The Anybody Bike". Popular Science: 58–59, 89.
- ^ Herlihy, David V. (2004). Bicycle, The History. Yale University Press. p. 76. ISBN 0-300-10418-9.
- ^ Brown 2007, p. [12] Extension levers
- ^ Brown 2007, p. [13] Interrupter Brake Levers
- ^ Brown 2007, p. [14] Brake Lever Types
- ^ Ibid. "Direct pull cantilevers have twice as much mechanical advantage as traditional brakes, so they require a lever with half as much mechanical advantage. Long pull levers pull the cable twice as far, but only half as hard."
- ^ Brown, p. [15] Brake Levers for Direct-pull Cantilevers
- ^ To solve the problem of using V-brakes with road levers, devices that use an eccentric pulley to increase the amount of cable pull of road levers, such as the "QBP Travel Agent", may be used.
- ^ Sheldon Brown. "The Geometry of Cantilever Brakes". Retrieved 2010-12-15.
- ^ Hydraulic systems transmit force through incompressible fluids. Boiling hydraulic fluid cannot transmit sufficient force since some of that fluid has become a compressible gas.
- ^ Allen, John S. "Using your Brakes". John S. Allen. Retrieved 2010-12-25.
- ^ Bill McCready, President Santana Cycles. "How To: Emergency Stops". Retrieved 2012-07-12.
A tandem with an adult stoker will skid instead of flip.
- ^ Brown, p. [16] Braking and Turning
- ^ Brown, p. [17] Right Front or Left Front?
- ^ "Western Australian Consolidated Regulations, Road Traffic Code 2000 - Reg 224". Retrieved 2011-07-02.
A person shall not ride a bicycle that does not have at least one effective brake.
- ^ "German road traffic licensing regulations (Straßenverkehrs-Zulassungs-Ordnung StVZO)". German Department of Justice. Retrieved 2012-07-27.
Fahrräder müssen zwei voneinander unabhängige Bremsen haben.
- ^ Matthew Sparkes (Wednesday 25 August 2010). "Cycling without brakes? You're breaking the law". Guardian News and Media Limited. Retrieved 2011-07-20.
Brakeless riders are strictly breaking the law in the UK.
{{cite web}}
: Check date values in:|date=
(help)
Sources
- Brandt, Jobst (2005). "Brakes from Skid Pads to V-brakes". Jobst Brandt: Frequently Asked Questions about Bicycles and Bicycling. Harris Cyclery. Retrieved 2009-01-22.
{{cite web}}
: Check|authorlink=
value (help); Cite has empty unknown parameter:|coauthors=
(help); External link in
(help); Invalid|authorlink=
|ref=harv
(help); Unknown parameter|month=
ignored (help)
- Brown, Sheldon. "Articles by Sheldon Brown and Others". Harris Cyclery Articles. Harris Cyclery. Retrieved 2010-06-21.
{{cite web}}
: Cite has empty unknown parameter:|month=
(help); Invalid|ref=harv
(help); Unknown parameter|coauthors=
ignored (|author=
suggested) (help)
- Brown, Sheldon (2007). "Bicycle Glossary". Sheldon Brown's Bicycle Glossary. Harris Cyclery. Retrieved 2010-06-21.
{{cite web}}
: Cite has empty unknown parameters:|month=
and|coauthors=
(help); Invalid|ref=harv
(help)
- Heine, Jan (2008). "Slow Down, The Story of Bicycle Brakes". Bicycle Quarterly (Winter 2008). Vintage Bicycle Press LLC: 36. ISSN 1941-8809.
{{cite journal}}
: Cite has empty unknown parameter:|coauthors=
(help); Invalid|ref=harv
(help)
- Whitt, Frank Rowland; Wilson, David Gordon (1982). Bicycling Science (2nd (hardcover) ed.). Cambridge, MA: The MIT Press. ISBN 978-0-262-23111-4. Retrieved 2010-05-04.
- Wilson, David Gordon (2004). Bicycling Science (3rd (paperback) ed.). Cambridge, MA: The MIT Press. ISBN 978-0-262-73154-6. Retrieved 2010-04-15.
{{cite book}}
: Cite has empty unknown parameters:|coauthors=
,|nopp=
,|chapterurl=
, and|authormask=
(help); Unknown parameter|month=
ignored (help)
- Template:Sv icon Ekström, Gert (2001). Älskade cykel (in Swedish) (1st ed.). Bokförlaget Prisma. ISBN 91-518-3906-7.
{{cite book}}
: Cite has empty unknown parameters:|origmonth=
,|month=
,|chapterurl=
, and|origdate=
(help); Unknown parameter|coauthors=
ignored (|author=
suggested) (help)CS1 maint: unrecognized language (link)