User:Quarks1318/sandbox
Centrifugal Fan Design
[edit]Centrifugal Fans are a part of our day to day life. They are used in pumps, compressors, blowers etc. The main function of centrifugal fan is to work on the fluid and to impart the static and kinetic energy with varying proportion depending upon the type of blades. The working of any centrifugal fan is a matter of converting the rotational energy of blades to the radial or axial energy of fluid. In centrifugal fan design the shape of blade is very important.
Design Variables of Centrifugal Fan
[edit]The design of centrifugal pump depends largely on the flow speed and the application of fan for example in blower or pump the blade shape is different. The various design variables of centrifugal fan design are explained below.

Blade Curvature
[edit]As mentioned above is determined by the application of fan i.e flow speed.In cases where the peripheral speed is high straight face blades are preferred over curved blades. This is because at high speed the blades subjected to high stresses and these stresses try to straighten the curved blades. In fan/blower the speed in relatively low hence curved blades are preferred. The choice of blade also depends on the volume flow rate. For more volume flow rate forward facing blades are used whereas backward curved blades are used for lesser volume flow rates.
Radial Depth of Blade
[edit]This is the length of blade measured along the impeller radius. This does not affect the pressure or the flow property. This length is greatest for the backward Curved blades and is smallest for the forward curved blades.
Axial Length of Blade
[edit]The axial length of blades changes considerably for different types of blades and different applications. This is the length of blade measured along the shaft. This determines the width of blade and hence also determine the volume flow rate. More the axial length of blade more will be the volume flow rate.
This dimension usually determines the size rating for similar type of blade. The volume flow rate varies with the square of the impeller diameter but there is not much effect on the head.
Velocity Triangle
[edit]Velocity triangle helps us in determining the flow geometry at the entry and exit of a blade. A minimum number of data is required to draw a velocity triangle at a point on blade. Some component of velocity varies at different point on the blade due to changes in the direction of flow. Hence an infinite number of velocity triangles are possible for a given blade. In order to describe the flow using only two velocity triangles we define mean values of velocity and their direction. Velocity triangle of any turbo machine has three components as shown:

- U - Blade velocity
- Vr – Relative Velocity
- V - Absolute velocity
These velocities are related by the triangle law of vector addition: -
- V=U+Vr
This relatively simple equation is used frequently while drawing the velocity diagram. The velocity diagram for the forward, backward face blades shown are drawn using this law. The angle α is the angle made by the absolute velocity with the axial direction and angle β is the angle made by blade with respect to axial direction.
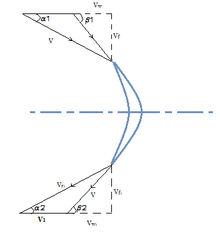
Noise
[edit]Noise is any unwanted or undesired sound. Noise has become an important design parameter for any equipment in recent decades since continuous exposure to elevated noises can create health problems like hearing impairment, hypertension, ischemic heart disease, annoyance, and sleep disturbance etc. Fans and blowers contribute to major portion of noise in industries. Noises from ventilation systems are another noise sources which should be taken care of.
Due to the flow within the fan noises are generated aerodynamically which are much higher than the noises generated from the bearings and vibration of various parts. If we install the fan properly and well balanced mechanical noises are almost negligible.
Turbulence is the main reason for noise in fans which are unavoidable. Turbulence increases with wake formation, higher fan speeds and off-design operations.
Main causes of aerodynamically generated noises are the flow at the entry and exit of the fan, rotation of blades through air or gas, passage of blades through wakes, turbulence of air, shedding of vortices from blades, separation, stalling and surging.
The sound power produced by centrifugal fans and axial fans can be approximated by a simple equation:
LW = KW + 10 log10Q + 20 log10P +BFI +CN
Where:
- LW = sound power level (dB)
- KW = specific sound power level depending on the type of fan (see Fig 9-3), from empirical data provided by fan manufacturer
- Q = volume flow rate (cfm)
- P = total pressure (inches of H20)
- BFI= Blade Frequency Increment = Correction for pure tone produced by the blade passing frequency (bpf), add this correction only to the octave band whose centre frequency is closest to the blade passing frequency.
- bpf= blade passing frequency = #of blades × RPM/60 (Hz)
- CN = efficiency correction (because fans that are operated off their optimum flow conditions get noisier)
For attaining the lowest noise output fans should always be operated at its peak efficiency point. Using of low speed, low pressure fans reduces turbulence which in turn reduces noise. Reinforcing of the fan casing and lining the internal surface of the casing with a sound absorbing material also reduces noise. Lining can also be done on the duct wall along with uniform flow through ducts brings the noise down considerably.
Losses in Centrifugal Fan
[edit]In centrifugal fans losses will be there in both stationary and moving parts of the centrifugal fan stage. We can get the actual performance of the centrifugal fan by taking these stage losses into account.
Various types of losses
Impeller entry losses
[edit]Due to the flow at the eye and it’s turning from axial to radial direction causes losses at the entry. Friction and separation causes impeller blade losses since there is change in incidence. Normally these impeller blade losses are also included in this head.
Leakage loss
[edit]Leakage of some air and disturbance in the main flow field is caused due to the clearance provided between the rotating periphery of the impeller and the casing at the entry.
Impeller losses
[edit]Passage friction and separation causes impeller losses which are dependent on relative velocity, rate of diffusion and blade geometry.
Diffuser and volute losses
[edit]Friction and separation also causes losses in diffuser. Further losses due to incidence occur if the device is working in off-design conditions. Flow from impeller or diffuser expands in the volute which is having larger cross section leading to the formation of Eddy, which in turn reduces head. Friction and flow separation losses also occur due the volute passage.
Disc Friction
[edit]Viscous drag on the back surface of the impeller disc causes Disc friction.