Pellet mill
A pellet mill, also known as a pellet press,[1] is a type of mill or machine press used to create pellets from powdered material. Pellet mills are unlike grinding mills, in that they combine small materials into a larger, homogeneous mass, rather than break large materials into smaller pieces.
Types
There are many types of pellet mills that can be generally grouped into large-scale and small-scale types.
Large-scale mills
There are two common types of large-scale pellet mills: flat die mills and ring die mills. Flat die mills use a flat die with slots. The powder is introduced to the top of the die and as the die rotates a roller presses the powder through the holes in the die. A cutter on the other side of the die cuts the exposed pellet free from the die.[1] In the ring die there are radial slot throughout the die. Powder is fed into the inside of the die and spreaders evenly distribute the powder. Two rollers then compress the powder through the die holes. Two cutters are used to cut the pellets free from the outside of the die.[2]
Large scale pellet mills are usually used to produce animal feed,[1] wood pellets, and fuel pellets for use in a pellet stove.
Small-scale mills
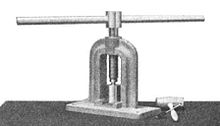
Small-scale mills are usually variations of screw presses or hydraulic presses. The same basic process is used for both types. A die, also known as a mold, holds the uncompressed powder in a shaped pocket. The pocket shape defined the final pellet shape. A platen is attached to the end of the screw (in a screw press) or the ram (in a hydraulic press) which compresses the powder.[3]
Some platens are heated to speed up the time it takes and improve the overall structure of the pellet. They may also have water ports for quick cooling between uses.[citation needed]
Definition of Pellet Plant
- Pellet Plant refers to a technological process of pelletization. Physically, it means a constructed mechanical project to produce pellets which is a kind of granule or column-shape substance and with pellet mill as the main part of a pellet production line. Generally, Pellet plant can be divided into two categories, namely, biomass pellet plant and feed pellet plant.
Biomass Pellet Plant
- Biomass pellet plant, as it name suggests, is mainly put into pelletization with biomass feedstock, namely, biomass raw material.
Raw Material Scope of Biomass Pellet Plant
- As per the classification of raw material, there are two main kinds of raw material used, that is to say, agricultural waste and forest or wood residues, but other kinds of material can be applied as well such as household garbage and wasted rubber and others yet rarely used for pelletization, for the processing techniques and related equipment are still limited. However, the two main types of feedstock for biomass pellet plant include as follows: Agro wastes: rice husks, corn cobs, maize stalks, peanut shells, sunflower seed shells, coconut shuck, coffee grounds, straw stalks, Tobacco waste Mustard Stalk, Jute waste, Bamboo Dust, Tea waste, Wheat Straw, Palm husk, Soybeans husk, Coir Pitch Barks/Straws,;
Wood wastes: Raw material resources: timber industry, sawmills, paper industry, furniture industry, building industry and agricultural by-products The varieties of trees: such as pinewood, birch, spruce, beech, poplar, eucalyptus, maple, tropical trees, subtropical trees and tree species from frigid zone and shrubs. Size of raw material: wood logs, timber, lumber, tree branches and twigs, tree trunks, wood chips, sawdust, saw shavings, wood powder and shrubs.[4]
Demanded Conditions of Pelletization for Biomass Pellet Plant
- ①size of feedstock(too small is as bad as oversized, presumably leading to no forming)
- ②moisture content of feedstock(disqualified moisture content may result in pellet fissures or too much mealy or sticky mixture)
- ③species of feedstock(due to the different cohesiveness and lignin contents of distinguished materials)
- ④Space of storing raw material and bagged pellets
Technological Process of Biomass Pellet Plant
- Theoretically, the pelletizing process covers not only pelletization per se, but also material pretreatment and post-treatment. The whole process can be roughly boiled down to a line;①debarking(if wood logs, timber or lumber will be put into use, this step shall be considered.)②chipping(if forest or wood material will be used, the previous step and this one shall be done.)③pulverizing(also called crushing, it is to reduce the size of material into qualified one, namely about 3mm or 4mm)③sifting(if some small sized material will be applied such as sawdust or rice husk, it shall be purified from metal scraps and other impurities.)④drying(commonly 12%-15% moisture content is needed.)⑤pelletizing⑥cooling⑦sieving⑧packaging.
Feed Pellet Plant
- Feed Pellet Plant is widely applicable to produce forage pellets for livestock, animal husbandry and aquaculture, offering feed for animals such as chicken, cow, pigs, horses, duck, fish and so forth. Feed pellet plant, comparing to biomass pellet plant, strictly demands nutrition, cleaness and sanitation of pellets, Therefore, the production of forage pellets is imperatively strigent than that of biomass pellets.And the processings of the above two are also distinguished as well, not least the pretreating section of raw materials, for example, mixture and addition of nutrients shall be attached more importance to during the pelletization.
Applications
One of the more common applications is to produce KBr pellets which are used in infrared spectroscopy applications.
Animal feed pellets are usually a mixture of dry powdered feedstock, such as flour, sawdust, or grass, and a wet ingredient, such as molasses or steam. Feedstocks for pellet mills can sometimes break down and then re-form, or polymerize, under the extreme heat and pressure of the pellet mill.[citation needed]
References
- ^ a b c Pietsch, Wolfgang (2005), Agglomeration in Industry: Occurrence and Applications, vol. 1, Wiley-VCH, p. 254, ISBN 978-3-527-30582-7.
- ^ Matz, Samuel A. (1991), The chemistry and technology of cereals as food and feed (2nd ed.), Springer, p. 328, ISBN 978-0-442-30830-8.
- ^ Connecticut Agricultural Experiment Station (1898), Tenth Annual Report of the Storrs Agricultural Experiment Station, Storrs, Conn. 1897, Pelton & King, pp. 208–209.
- ^ [1]