Oilfield scale inhibition
This sandbox is in the article namespace. Either move this page into your userspace, or remove the {{User sandbox}} template.
Oil Scale Inhibition
Scale inhibitors are a class of specialty chemicals that are used to slow or prevent scaling in water systems.[1][2] Industrial scaling is the precipitation and accumulation of insoluble salts from a mixture of incompatible aqueous phases of processing systems. Scaling represents a major challenge for flow assurance in the oil and gas industry. ‘Scale’ is a common term in the oil industry used to describe solid deposits that grow over time, blocking and hindering fluid flow through pipelines, valves, pumps etc with significant reduction in production rates and equipment damages. Examples of scales in the oil/gas industry are calcium carbonate, barium sulfate and strontium sulfate.
Background

The rate of oil production has seen a steady growth from 88 million barrels/day(mmbpd) to over 95 mmbpd since 2011. Consequently, chemical consumption in oil production has also increased significantly. Crude oil is basically a mixture of petroleum, water and natural gas extracted from accumulated fluids in oil reservoirs which. The specialty oilfield chemical market has projected[3] a 10-year chemical consumption rate from 86.7 mmbpd to 93.3 mmbpd between 2010 to 2020, valued at $30.3 billion. However, the projected value in 2019 may be slightly lower due to the lower oil prices and drop in chemical consumption rate for 2015 and 2016. There is therefore the need for more effective and greener chemistries to meet the growing demand. The three prevailing water-related problems that upsets oil companies today are corrosion, gas hydrates and scale formation in production systems.[4][5] The reservoir water has a high composition of dissolved minerals equilibrated over millions of years at constant physicochemical conditions. As the reservoir fluids are pumped from the ground, changes in temperature, pressure and chemical composition shifts the equilibria and causes precipitation and deposition of the sparingly soluble salts. Scaling can occur at all stages of oil/gas production systems (upstream, midstream and downstream) and causes blockages of wellbore perforations, casing, pipelines, pumps, valves etc. Severe scaling issues have been reported in Russia and certain North Sea production systems.[6]
Types of Scales
Two main classifications of scales are known; inorganic and organic (mixed scale) and the two types are mutually inclusive. Occurrence of the two processes in one production system may result in highly complexly-structured scales that would require aggressive, severe and highly costly remediation techniques. Paraffin wax, Asphaltenes and gas hydrates are the most often encountered organic scales in the oil industry.
Inorganic scale
Inorganic scales refer to mineral deposits that occur when the formation water mixes with different brines such as injection water. The mixing changes causes reaction between incompatible ions and changes the thermodynamic and equilibrium state of the reservoir fluids. Supersaturation and subsequent deposition of the inorganic salts occur. The most common types of inorganic scales known to the oil/gas industry are carbonates and sulfates; sulfides and chlorites are also present.
Name | Chemical Formula | Mineral |
---|---|---|
Calcium Carbonate | CaCO3 | Calcite, aragonite |
Calcium sulfate | CaSO4 | Anhydrite,gypsum (CaSO4.2H2O) hemihydrate (CaSO4.0.5H2O) |
Calcium oxalate | CaC2O4 | Beerstone |
Barium Sulfate | BaSO4 | Barite |
Magnesium Hydroxide | Mg(OH)2 | Brucite |
Magnesium oxide | MgO | Periclase |
Silicates | Me(SinOx).yH2O | Serpentine, acmite, gyrolite, gehlenite, amorphous silica, quartz, cristobalite, pectolite |
Aluminium oxide hydroxides | AlO(OH) | Boehmite, gibbsite,diaspore, corundum |
Aluminosilicates | AlxSiyOz | Analcite, cancrinite, noselite |
Copper | Cu | Metallic copper, cuprite (Cu2O), tenorite (Cu ) |
Magnetite or Nickel ferrite | NiFe2O4 | Trevorite |
Phosphates | Ca10(PO4)6(OH)2 | Hydroxyapatite |
Calcium carbonate scale
Water, commonly is often referred to as a universal solvent can dissolve certain gases such as carbon(IV)oxide (CO2) to form aqueous CO2(aq). Under the right conditions of temperature and/or pressure a reaction between H2O molecules and CO2(aq) yields carbonic acid (H2CO3(aq)) which is only stable under low temperature and high pressure conditions. H2CO3(aq) dissolves in water according to equation (3) to form hydronium and bicarbonate (HCO3-(aq)) ions. The process can be described by the equilibrium reaction below;
- 2HCO3-(aq) ↔ CO32-(aq) + H2O(l) + CO2(g)
- Ca2+(aq) + CO32-(aq) ↔ CaCO3(s)
The two reactions (1) and (2) describe the equilibrium between bicarbonate ions (HCO3-), which are highly soluble in water and Calcium carbonate (CaCO3) scales. According to Le Chartellier’s principle, drilling operations and extraction of the oil from the well bore decreases the pressure of the formation and the equilibrium shifts to the right (1) to increase the production of CO2 to offset the change. After years of oil production, wells may experience significant pressure drop resulting in large CaCO3 scale problems as the equilibrium shifts to the right. Further reduction in pressure along the pipelines moves the scale formation upstream in the system.[4]
Sulfate Scales
Sulfates of Group (II) metal ions, generally decrease in solubility down the group, berylium and magnesium are exceptions.The most difficult scale to remove are Barium sulfate scales because it is highly insoluble and forms a very hard deposit. A general representation of the reaction is summarized in reaction (4)
M2+ + SO42- → MSO4 (s)
Sulfate scale usually forms when formation water and injected seawater mixes together.[5] The relationship between these and the degree of oversaturation is crucial to the amount of sulfate salts that will precipitate in the system.[7] It is the high concentration of sulfate in seawater which reacts with group (II) metal ions in the formation water. This will lead to the formation of sulfate scale. Severe problems with sulfate scale are most common in reservoirs where seawater has been injected to enhance oil recovery.[5]
Calcium sulfate is the easiest sulfate scale to remove chemically. This is due to its relatively high solubility in water compared to strontium and barium sulfate, in water and also its solubility in several chelating solutions. Unlike calcium sulfate, barium sulfate is extremely insoluble and therefore very hard to remove chemically.[5] When scale has started to form in the production piping, it will rapidly build up if it is not treated and can end up with a full blockage. This leads to a high demand for prevention of such scale.
Scale Remediation
Different oilfield scale remediation techniques are known but majority are based on three basic themes:
- Sulfate ion sequestering from sea injection waters
- Chemical or mechanical Scale removal/dissolution
- Application of Scale inhibitors for scale prevention
The first two methods may be used for short-term treatment and may be effective for mild-scaling conditions[5], however, continuous injection or chemical scale squeeze treatment with Scale inhibitors have been proven over the years to be the most efficient and cost-effective preventative technique.[8]
Scale Inhibitors
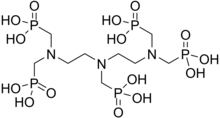
Scale inhibitors are specialty chemicals that are added to oil production systems to delay, reduce and/or prevent scale deposition. Currently, acrylic acid polymers, maleic acid polymers and phosphonates have been used extensively for scale treatment in water systems due to their excellent solubility, thermal stability and dosage efficiency.[9][10] In the oil industry, the major classes of SIs have inorganic phosphate, organophosphorous and organic polymer backbones. Two common oilfield mineral Scale Inhibitors are Poly-Phosphono Carboxylic acid (PPCA) and Diethylenetriamine- penta (methylene phosphonic acid) (DTPMP).[11]
Inhibition of calcium carbonate scale precipitation and crystal studies of its polymorphs have been conducted.[12][13][14] For an efficient scale inhibition, knowledge about the crystal structure of the particular scale and how that could be aligned with the structure of the scale inhibitor. Different scale inhibitors are designed for specific scaling conditions and biodegradability properties.[12] The inhibitor molecules essentially bind ions in produced water that could potentially precipitate and therfore prevents scaling. For instance, to bind positively charged ions in the water, anions must be present in the inhibitor molecular backbone structure and vice versa. Group (II) metal ions are commonly sequestered by scale inhibitors with the following functionalities;
- Phosphonate ions (-PO3H-)
- Phosphate ions (-OPO3H-)
- Phosphonate ions (-PO2H-)
- Sulphonate ions (-SO3-)
- Carboxylate ions (-CO2-)
A scale inhibitor with a combination of two or more of these functional groups is more efficient in managing scale problems. Usually the sodium salts of the carboxylic derivatives are synthesized as the anionic derivatives and are known to be the most effective due to their high solubilities.
Many classes of traditional SI’s, for example acrylate-based polymers or amino-phosphonates, are very poorly biodegradable. In addition, outlet of production water containing inhibitors with nitrogen or phosphorous could add unnatural amounts of nutrients to the ocean environment and thereby create an imbalance in the natural equilibrium. Figure 1.4 illustrates the discharges from an offshore platform to air and sea, were a large part of the discharge to sea is SI’s. From the early 9 ’s, there have been a great effort to create more environmentally-friendly SI’s. An increasing number of such SI’s are becoming commercially available[3]. To get a new SI or similar chemical for offshore use approved, it needs to undergo extensive pretesting. There are several requirements to the chemicals, among them are the strict environmental regulations in the North Sea. This limits the range of chemicals which can be used. The requirements have only become stricter in recent years since Norway is working towards a zero discharge principle[29].
Reference
- ^ Liang, Bin; Pan, Kai; Li, Li; Giannelis, Emmanuel P.; Cao, Bing (2014-08-15). "High performance hydrophilic pervaporation composite membranes for water desalination". Desalination. 347: 199–206. doi:10.1016/j.desal.2014.05.021.
- ^ Alzahrani, Salem; Mohammad, Abdul Wahab (2014-12-01). "Challenges and trends in membrane technology implementation for produced water treatment: A review". Journal of Water Process Engineering. 4: 107–133. doi:10.1016/j.jwpe.2014.09.007.
- ^ "Global Industry Analysis Inc". Feb 2016. Retrieved 10 Oct 2016.
- ^ a b Kelland,, M. A. (6 Feb 2014). Production chemicals for the oil and gas industry. CRC press. ISBN 9781439873793.
{{cite book}}
:|access-date=
requires|url=
(help)CS1 maint: extra punctuation (link) - ^ a b c d e W. Frenier, Wayne (2008). Formation, removal, and inhibition of inorganic scale in the oilfield environment. http://catdir.loc.gov/catdir/toc/fy12pdf01/2009517707.html: Society of Petroleum Engineers. ISBN 1555631401.
{{cite book}}
: External link in
(help)CS1 maint: location (link)|location=
- ^ Mitchell, R.W; Grist, D.M.; Boyle, M.J. (May 1980). "Chemical Treatments Associated with North Sea Projects". Society of Petroleum Engineers. 32 (05): 904-912. doi:10.2118/7880-PA.
{{cite journal}}
:|access-date=
requires|url=
(help) - ^ Collins, I.R. (2002-01-01). "A New Model for Mineral Scale Adhesion". International Symposium on Oilfield Scale. Society of Petroleum Engineers. doi:10.2118/74655-ms. ISBN 9781555639426.
- ^ Laing, N.; Graham, G.M.; Dyer, S.J. (2003-01-01). "Barium Sulphate Inhibition in Subsea Systems - The Impact of Cold Seabed Temperatures on the Performance of Generically Different Scale Inhibitor Species". International Symposium on Oilfield Chemistry. Society of Petroleum Engineers. doi:10.2118/80229-ms. ISBN 9781555639556.
- ^ Amjad, Zahid; Koutsoukos, Petros G. (2014-02-17). "Evaluation of maleic acid based polymers as scale inhibitors and dispersants for industrial water applications". Desalination. 335 (1): 55–63. doi:10.1016/j.desal.2013.12.012.
- ^ Shakkthivel, P.; Vasudevan, T. (2006-10-02). "Acrylic acid-diphenylamine sulphonic acid copolymer threshold inhibitor for sulphate and carbonate scales in cooling water systems". Desalination. 197 (1): 179–189. doi:10.1016/j.desal.2005.12.023.
- ^ Bezemer, Cornelis; Bauer, Karl A. (1969-04-01). "Prevention of Carbonate Scale Deposition: A Well-Packing Technique with Controlled Solubility Phosphates". Journal of Petroleum Technology. 21 (04): 505–514. doi:10.2118/2176-pa. ISSN 0149-2136.
- ^ a b Shi, Wenyan; Xia, Mingzhu; Lei, Wu; Wang, Fengyun (2013-08-01). "Molecular dynamics study of polyether polyamino methylene phosphonates as an inhibitor of anhydrite crystal". Desalination. 322: 137–143. doi:10.1016/j.desal.2013.05.013.
- ^ Fried, Ruth; Mastai, Yitzhak (2012-01-01). "The effect of sulfated polysaccharides on the crystallization of calcite superstructures". Journal of Crystal Growth. 338 (1): 147–151. doi:10.1016/j.jcrysgro.2011.09.044.
- ^ Shi, Wen-Yan; Ding, Cheng; Yan, Jin-Long; Han, Xiang-Yun; Lv, Zhi-Min; Lei, Wu; Xia, Ming-Zhu; Wang, Feng-Yun (2012-04-02). "Molecular dynamics simulation for interaction of PESA and acrylic copolymers with calcite crystal surfaces". Desalination. 291: 8–14. doi:10.1016/j.desal.2012.01.019.