Oilfield scale inhibition
This sandbox is in the article namespace. Either move this page into your userspace, or remove the {{User sandbox}} template.
Oilfield Scale Inhibition
Scale inhibitors (SIs) are a class of specialty chemicals that are used to slow or prevent scaling in water systems.[1][2] Oilfield scaling is the precipitation and accumulation of insoluble crystals (salts) from a mixture of incompatible aqueous phases in oil processing systems.[2] ‘Scale’ is a common term in the oil industry used to describe solid deposits that grow over time, blocking and hindering fluid flow through pipelines, valves, pumps etc with significant reduction in production rates and equipment damages.[3][2] Scaling represents a major challenge for flow assurance in the oil and gas industry. Examples of oilfield scales are calcium carbonate, iron sulfides, barium sulfate and strontium sulfate. Scale inhibition encompasses the processes or techniques employed to treat scaling problems.[2]
Background

The global economy, over the past century has been characterized by a substantial increase in energy demand per population growth.[4] The world's population currently stands at approximately 7.5 billion[5], representing an over four-fold growth since 1900s with corresponding increase in an order of magnitude in energy growth from 0.9 x 109 tons of oil equivalence (TOE) to 1.02 x 1010 TOE.[4] The growing drift of new oil and gas discoveries towards the deep seas calls for sophisticated, more potent and efficient technologies and chemistries to ensure effective flow assurance and asset integrity in the near future. The rate of oil production has seen a steady growth from 88 million barrels per day(mmbpd) to over 95 mmbpd since 201.[6] Consequently, chemical consumption in oil production has also increased significantly, a trend that is expected to continue in the next decades. Petroleum, a mixture of hydrocarbons, water and natural gas accumulated in the bedrock of the earth, called oil reservoirs is extracted and processed into its constituent products using tons of different specialty oilfield chemicals.[7] The specialty oilfield chemical market has projected[6] a 10-year chemical consumption rate from 86.7 mmbpd to 93.3 mmbpd between 2010 to 2020, valued at $30.3 billion. However, the projected value in 2019 may be slightly lowered due to the drop in oil prices in 2015 and 2016.[6] According to the recent BP Statistical Review of world energy, June 2016, 32.9% of global energy consumption is derived from oil, retaining its position as the world’s leading fuel.[8] The growth in global energy consumption is dominated by emerging economies like China and India, accounting for about 58.1% of the global energy consumption. Growth in these countries (+1.6%) however, fell short of a 10-year average of 3.8%. As compared to China, India recorded another robust growth in energy consumption of +5.2%, the Chinese's growth slowing down by 1.5%.[8] These statistics are a confirmation of the urgent need for more effective and greener chemistries to meet the growing demand and sustaining a cleaner environment.
The three prevailing water-related problems that upset oil companies today are corrosion, gas hydrates and scaling in production systems.[7][2] The reservoir water has a high composition of dissolved minerals equilibrated over millions of years at constant physicochemical conditions. As the reservoir fluids are pumped from the ground, changes in temperature, pressure and chemical composition shift the equilibria and cause precipitation and deposition of sparingly soluble salts that build up over time with the potential of blocking vital assets in the oil production setups.[9] Scaling can occur at all stages of oil/gas production systems (upstream, midstream and downstream) and causes blockages of well-bore perforations, casing, pipelines, pumps, valves etc. Severe scaling issues have been reported in Russia and certain North Sea production systems.[10]
Types of Scales
Two main classifications of scales are known; inorganic and organic scales and the two types are mutually inclusive, occurring simultaneously in the same system, referred to as mixed scale.[7][9] Mixed scales may result in highly complexly-structured scales that are difficult to treat. Such scales require aggressive, severe and sometimes costly remediation techniques.[7] Paraffin wax, Asphaltenes and gas hydrates are the most often encountered organic scales in the oil industry. This article focuses on the simplest and common form of scales encountered; inorganic scales.
Inorganic scale
Inorganic scales refer to mineral deposits that occur when the formation water mixes with different brines such as injection water. The mixing changes causes reaction between incompatible ions and changes the thermodynamic and equilibrium state of the reservoir fluids. Supersaturation and subsequent deposition of the inorganic salts occur. The most common types of inorganic scales known to the oil/gas industry are carbonates and sulfates; sulfides and chlorites are often encountered.
Name | Chemical Formula | Mineral |
---|---|---|
Calcium Carbonate | CaCO3 | Calcite, aragonite |
Calcium sulfate | CaSO4 | Anhydrite,gypsum (CaSO4.2H2O) hemihydrate (CaSO4.0.5H2O) |
Calcium oxalate | CaC2O4 | Beerstone |
Barium Sulfate | BaSO4 | Barite |
Magnesium Hydroxide | Mg(OH)2 | Brucite |
Magnesium oxide | MgO | Periclase |
Silicates | Me(SinOx).yH2O | Serpentine, acmite, gyrolite, gehlenite, amorphous silica, quartz, cristobalite, pectolite |
Aluminium oxide hydroxides | AlO(OH) | Boehmite, gibbsite,diaspore, corundum |
Aluminosilicates | AlxSiyOz | Analcite, cancrinite, noselite |
Copper | Cu | Metallic copper, cuprite (Cu2O), tenorite (Cu ) |
Magnetite or Nickel ferrite | NiFe2O4 | Trevorite |
Phosphates | Ca10(PO4)6(OH)2 | Hydroxyapatite |
Calcium carbonate scale
Water, noted for its high solvation power can dissolve certain gases such as carbon(IV)oxide (CO2) to form aqueous CO2(aq). Under the right conditions of temperature and/or pressure, H2O and CO2(aq) molecules react to yield carbonic acid (H2CO3) which is only stable under low temperature and high pressure conditions. The slightest changes in pressure and temperature dissolves H2CO3(aq) in water according to equation (3) to form hydronium and bicarbonate (HCO3-(aq)) ions.
- CO2(aq) + H2O(l)↔ H2CO3(aq)
- H2CO3(aq) ↔ H+(aq) + HCO3-(aq)
- 2HCO3-(aq) ↔ CO32-(aq)+ H2O(l)+ CO2(g)
- Ca2+(aq) + CO32-(aq) ↔ CaCO3(s)
The two reactions (2) and (4) describe the equilibrium between bicarbonate ions (HCO3-), which are highly soluble in water and Calcium carbonate (CaCO3) salt. According to Le Chatellier’s principle, drilling operations and extraction of the oil from the well bore decreases the pressure of the formation and the equilibrium shifts to the right (3) to increase the production of CO2 to offset the change in pressure. After years of oil production, wells may experience significant pressure drops resulting in large CaCO3 deposits as the equilibrium shifts to the to offset the pressure changes.[7]
Sulfate Scales
Sulfates of Group (II) metal ions (M2+), generally decrease in solubility down the group. The most difficult scales to remove are those of Barium sulfate because of its high insolubility forming very hard scale deposits. A general representation of the reaction is summarized in reaction:
5. M2+(aq) + SO42-(aq) → MSO4(s)
Sulfate scale usually forms when formation water and injected seawater mix together.[2] The relationship between these and the degree of supersaturation is crucial in estimating the amount of sulfate salts that will precipitate in the system.[11] Seawater has a high concentration of sulfate ions and mixing with formation water with lots of Ca2+ and other M2+ ions in the formation water. Severe problems with sulfate scale are common in reservoirs where seawater has been injected to enhance oil recovery.[2]
Due to its relatively high solubility in water, Calcium sulfate is the easiest sulfate scale to remove chemically as compared to strontium and barium sulfate.[2] Scale crystals are initially dispersed in production systems until accumulation of stable crystals of insoluble sulfates and scale growth occur at nucleation centers.[12] Uneven pipeline surfaces and production equipment such as pumps and valves cause rapid scale growth to levels that can block pipelines.[7]
The scaling-tendency of an oil-well can be predicted based on the prevailing conditions such as pH, temperature, pressure, ionic strength and the mole fraction of CO2 in the vapor and aqueous phases.[13] For instance the saturation index for CaCO3 scale is calculated using the formula;
Fs= {[Ca2+][CO3]}/Ksp
Where Fs is the scale saturation ratio, defined as the ratio of the activity product to the solubility product of the salt. Activity is defined as the product of the activity coefficients and the concentrations of Ca2+ and SO42- ions. The ionic strength is a measure of the concentration of the dissociated ions dissolved in water also called as “total dissolved solids” (TDS).[13]
Scale Remediation
Different oilfield scale remediation techniques are known but majority are based on three basic themes:
- Sulfate ion sequestering from sea injection waters
- Chemical or mechanical Scale removal/dissolution
- Application of Scale Inhibitors (SIs) for scale prevention
The first two methods may be used for short-term treatment and effective for mild-scaling conditions[2], however, continuous injection or chemical scale squeeze treatment with SIs have been proven over the years to be the most efficient and cost-effective preventative technique.[14]
Scale Inhibitors
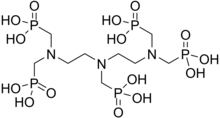
Scale inhibitors are specialty chemicals that are added to oil production systems to delay, reduce and/or prevent scale deposition.[7] acrylic acid polymers, maleic acid polymers and phosphonates have been used extensively for scale treatment in water systems due to their excellent solubility, thermal stability and dosage efficiency.[15][16] In the water treatment industry, the major classes of SIs have inorganic phosphate, organophosphorous and organic polymer backbones and common examples are PBTC (phosphonobutane-1,2,4-tricarboxylic acid), ATMP (amino-trimethylene phosphonic acid) and HEDP (1-hydroxyethylidene-1,1-diphosphonic acid), polyacrylic acid (PAA), phosphinopolyacrylates (such as PPCA), polymaleic acids (PMA), maleic acid terpolymers (MAT), sulfonic acid copolymers, such as SPOCA (sulfonated phosphonocarboxylic acid), polyvinyl sulfonates. Two common oilfield mineral SIs are Poly-Phosphono Carboxylic acid (PPCA) and Diethylenetriamine- penta (methylene phosphonic acid) (DTPMP).[17]
Inhibition of calcium carbonate scale precipitation and crystal studies of its polymorphs have been conducted.[18][19][20] Different SIs are designed for specific scaling conditions and biodegradability properties.[18] The inhibitor molecules essentially bind ions in aqueous phase of production fluids that could potentially precipitate as scales. For instance, to bind positively charged ions in the water, anions must be present in the inhibitor molecular backbone structure and vice versa. Group (II) metal ions are commonly sequestered by SIs with the following functionalities;[7]
- Phosphonate ions (-PO3H-)
- Phosphate ions (-OPO3H-)
- Phosphonate ions (-PO2H-)
- Sulphonate ions (-SO3-)
- Carboxylate ions (-CO2-)
A SI with a combination of two or more of these functional groups is more efficient in managing scale problems. Usually the sodium salts of the carboxylic derivatives are synthesized as the anionic derivatives and are known to be the most effective due to their high solubilities.[7] Interactions of these functional groups tend to prevent the crystal growth sites using dissociated or un-dissociated groups. The dissociation state is determined by the pH of the system, hence knowledge of the pKa values of the chemicals are important for different pH environments.[21] Again, the inhibition efficiency of the SI depends on its compatibility with other production chemicals such as corrosion inhibitors.[22]
Environmental Considerations
A lot of efforts to develop more environmentally-friendly SIs have been made since the late 1990s and an increasing number of such SIs are becoming commercially available.[7] Recent environmental awareness over the past 15 years has resulted in the production and application of more environmentally friendly SIs, otherwise referred to as 'Green Scale Inhibitors' (GSI).[23] These GSIs are specially designed to have reduced bio-accumulating and high biodegradability properties and therefore reduce pollution of the waters around oil platforms and the pipeline systems.[23] As specialty oilfield chemical industries focus on producing efficient and more environmentally safe scale-inhibition products, the most important question that stakeholders try to an answer is which SIs is safe to use. The challenge for these companies is to develop products that have reduced environmental persistence but high scale-inhibition power and questions still remain about whether the new class of “green” products are effective scale inhibitors.[7][23][24] Phosphate ester SIs, commonly employed for treating calcium carbonate scales are known to be environmentally-friendly but poor inhibition efficiency.[24] However, these SIs are not among the most efficient and therefore many more SI chemistries are being developed daily. SIs containing Nitrogen and Phosphorus are unsafe for the environment, especially when large quantities of produced waters are released in into the environment.[24] The Nitrogen and Phosphorus are unnatural nutrients added to distort the natural equilibrium of the immediate water body and may affect aquatic life by enhancing stratification in severe cases.
Polysaccharide SIs have attracted much research interest because they contain no Phosphorus or Nitrogen and are noted for their non-toxic, renewable, and biodegradable properties that meet the requirements for environmentally friendly materials.[25][26] An inherently biodegradable polysaccharide is Carboxymethyl inulin (CMI), which is isolated from the roots of Inula helenium has been used in oil exploration and its very low toxicity[27] and crystal growth inhibition power[28] has been reported as one of the very effective inhibitor of calcite crystal growth.[29] Examples of poorly biodegradable SIs such as the amino-phosphonate and acrylate-based SIs are being faced out by stringent environmental regulations as demonstrated in the North sea. The requirements have only become stricter in recent years since Norway is working towards a zero discharge principle.[30]
Generally, the environmental impacts of SIs are complicated further by combination of other oilfield chemicals in different operations such as exploratory, drilling, well-completion and start-up procedures. Produced fluids, and other wastes from oil and gas operations with high content of different toxic compounds are hazardous and harmful to human health, water supplies, marine and freshwater organisms.[31][32] For instance trails of increased turbidity resulting from oil and gas exploratory activities on the eastern shelf of Sakhalin in Russia have been reported with consequential adverse effects on salmon, cod and littoral amphipods.[33]
Reference
- ^ Alzahrani, Salem; Mohammad, Abdul Wahab (2014-12-01). "Challenges and trends in membrane technology implementation for produced water treatment: A review". Journal of Water Process Engineering. 4: 107–133. doi:10.1016/j.jwpe.2014.09.007.
- ^ a b c d e f g h i W. Frenier, Wayne (2008). Formation, removal, and inhibition of inorganic scale in the oilfield environment. http://catdir.loc.gov/catdir/toc/fy12pdf01/2009517707.html: Society of Petroleum Engineers. ISBN 1555631401.
{{cite book}}
: External link in
(help)CS1 maint: location (link)|location=
- ^ Liang, Bin; Pan, Kai; Li, Li; Giannelis, Emmanuel P.; Cao, Bing (2014-08-15). "High performance hydrophilic pervaporation composite membranes for water desalination". Desalination. 347: 199–206. doi:10.1016/j.desal.2014.05.021.
- ^ a b Makogon, Y. F.; Holditch, S. A.; Makogon, T. Y. (2007-03-01). "Natural gas-hydrates — A potential energy source for the 21st Century". Journal of Petroleum Science and Engineering. Natural Gas Hydrate / ClathrateThe Major Organic Carbon Reserve of the Earth. 56 (1–3): 14–31. doi:10.1016/j.petrol.2005.10.009.
- ^ "World population clock". Worldometers. 2016. Retrieved November 27, 2016.
- ^ a b c "Global Industry Analysis Inc". Feb 2016. Retrieved 10 Oct 2016.
- ^ a b c d e f g h i j k Kelland,, M. A. (6 Feb 2014). Production chemicals for the oil and gas industry. CRC press. ISBN 9781439873793.
{{cite book}}
:|access-date=
requires|url=
(help)CS1 maint: extra punctuation (link) - ^ a b "BP statistical review of world energy, June 2016" (PDF). www.bp.com. US Securities and Exchange Commission. Retrieved November 19, 2016.
- ^ a b Wayne W Frenier, Murtaza Ziauddin, N. Wolf (Editor), Ryan Hartman (Editor) (2008). Formation, removal, and inhibition of inorganic scale in the oilfield environment. Society of Petroleum Engineers. ISBN 1555631401.
{{cite book}}
:|last=
has generic name (help)CS1 maint: multiple names: authors list (link) - ^ Mitchell, R.W; Grist, D.M.; Boyle, M.J. (May 1980). "Chemical Treatments Associated with North Sea Projects". Society of Petroleum Engineers. 32 (05): 904-912. doi:10.2118/7880-PA.
{{cite journal}}
:|access-date=
requires|url=
(help) - ^ Collins, I.R. (2002-01-01). "A New Model for Mineral Scale Adhesion". International Symposium on Oilfield Scale. Society of Petroleum Engineers. doi:10.2118/74655-ms. ISBN 9781555639426.
- ^ Crabtree, M., Eslinger, D., Fletcher, P., Miller, M., Johnson, A., & King, G. (1999). "Fighting Scale- prevention and removal". Oilfield Review. 11(3): 30–45.
{{cite journal}}
: CS1 maint: multiple names: authors list (link) - ^ a b Oddo, J.E.; Tomson, M.B. (1994-02-01). "Why Scale Forms in the Oil Field and Methods To Predict It". SPE Production & Facilities. 9 (01): 47–54. doi:10.2118/21710-pa. ISSN 1064-668X.
- ^ Laing, N.; Graham, G.M.; Dyer, S.J. (2003-01-01). "Barium Sulphate Inhibition in Subsea Systems - The Impact of Cold Seabed Temperatures on the Performance of Generically Different Scale Inhibitor Species". International Symposium on Oilfield Chemistry. Society of Petroleum Engineers. doi:10.2118/80229-ms. ISBN 9781555639556.
- ^ Amjad, Zahid; Koutsoukos, Petros G. (2014-02-17). "Evaluation of maleic acid based polymers as scale inhibitors and dispersants for industrial water applications". Desalination. 335 (1): 55–63. doi:10.1016/j.desal.2013.12.012.
- ^ Shakkthivel, P.; Vasudevan, T. (2006-10-02). "Acrylic acid-diphenylamine sulphonic acid copolymer threshold inhibitor for sulphate and carbonate scales in cooling water systems". Desalination. 197 (1): 179–189. doi:10.1016/j.desal.2005.12.023.
- ^ Bezemer, Cornelis; Bauer, Karl A. (1969-04-01). "Prevention of Carbonate Scale Deposition: A Well-Packing Technique with Controlled Solubility Phosphates". Journal of Petroleum Technology. 21 (04): 505–514. doi:10.2118/2176-pa. ISSN 0149-2136.
- ^ a b Shi, Wenyan; Xia, Mingzhu; Lei, Wu; Wang, Fengyun (2013-08-01). "Molecular dynamics study of polyether polyamino methylene phosphonates as an inhibitor of anhydrite crystal". Desalination. 322: 137–143. doi:10.1016/j.desal.2013.05.013.
- ^ Fried, Ruth; Mastai, Yitzhak (2012-01-01). "The effect of sulfated polysaccharides on the crystallization of calcite superstructures". Journal of Crystal Growth. 338 (1): 147–151. doi:10.1016/j.jcrysgro.2011.09.044.
- ^ Shi, Wen-Yan; Ding, Cheng; Yan, Jin-Long; Han, Xiang-Yun; Lv, Zhi-Min; Lei, Wu; Xia, Ming-Zhu; Wang, Feng-Yun (2012-04-02). "Molecular dynamics simulation for interaction of PESA and acrylic copolymers with calcite crystal surfaces". Desalination. 291: 8–14. doi:10.1016/j.desal.2012.01.019.
- ^ Graham, GM Boak, LS Sorbie, KS (2003). "The influence of formation calcium and magnesium on the effectiveness of generically different barium sulphate oilfield scale inhibitors". SOC PETROLEUM ENG. 18: 28–44 – via Science Citation Index.
{{cite journal}}
: CS1 maint: multiple names: authors list (link) - ^ Lawless, T.A.; Bourne, H.M.; Bolton, J.R. (1993-01-01). "Examining the Potential for Corrosion Inhibitor and Scale Inhibitor Compatibility in a Multifunctional Squeeze Strategy". SPE International Symposium on Oilfield Chemistry. Society of Petroleum Engineers. doi:10.2118/25167-ms. ISBN 9781555634926.
- ^ a b c Boak, Lorraine S.; Sorbie, Ken (2010-11-01). "New Developments in the Analysis of Scale Inhibitors". SPE Production & Operations. 25 (04): 533–544. doi:10.2118/130401-pa. ISSN 1930-1855.
- ^ a b c Jordan, Myles M.; Sorhaug, Eyvind; Marlow, David (2012-11-01). "Red vs. Green Scale Inhibitors for Extending Squeeze life--A Case Study From the North Sea, Norwegian Sector--Part II". SPE Production & Operations. 27 (04): 404–413. doi:10.2118/140752-pa. ISSN 1930-1855.
- ^ Pro, Danièle; Huguet, Samuel; Arkoun, Mustapha; Nugier-Chauvin, Caroline; Garcia-Mina, José Maria; Ourry, Alain; Wolbert, Dominique; Yvin, Jean-Claude; Ferrières, Vincent (2014-11-04). "From algal polysaccharides to cyclodextrins to stabilize a urease inhibitor". Carbohydrate Polymers. 112: 145–151. doi:10.1016/j.carbpol.2014.05.075.
- ^ Liu, Jun; Willför, Stefan; Xu, Chunlin (2015-01-01). "A review of bioactive plant polysaccharides: Biological activities, functionalization, and biomedical applications". Bioactive Carbohydrates and Dietary Fibre. 5 (1): 31–61. doi:10.1016/j.bcdf.2014.12.001.
- ^ Johannsen, F. R (2003-01-01). "Toxicological profile of carboxymethyl inulin". Food and Chemical Toxicology. 41 (1): 49–59. doi:10.1016/S0278-6915(02)00213-2.
- ^ Kirboga, Semra; Öner, Mualla (2013-04-16). "Investigation of calcium carbonate precipitation in the presence of carboxymethyl inulin". CrystEngComm. 15 (18). doi:10.1039/c3ce27022j. ISSN 1466-8033.
- ^ Kırboga, Semra; Öner, Mualla (2012-03-01). "The inhibitory effects of carboxymethyl inulin on the seeded growth of calcium carbonate". Colloids and Surfaces B: Biointerfaces. 91: 18–25. doi:10.1016/j.colsurfb.2011.10.031.
- ^ Knudsen, B.L.; Hjelsvold, M.; Frost, T.K.; Svarstad, M.B.E.; Grini, P.G.; Willumsen, C.F.; Torvik, H. (2004-01-01). "Meeting the Zero Discharge Challenge for Produced Water". SPE International Conference on Health, Safety, and Environment in Oil and Gas Exploration and Production. Society of Petroleum Engineers. doi:10.2118/86671-ms. ISBN 9781555639815.
- ^ "Drilling Waste Streams from Offshore Oil and Gas Installations". www.offshore-environment.com. Retrieved 2016-11-22.
- ^ Davies, Michael ; P. J. B. Scott (2006). Oilfield water technology. NACE International. pp. 523–32. ISBN 978-1-57590-204-3.
{{cite book}}
: CS1 maint: multiple names: authors list (link) - ^ Knudsen, B.L.; Hjelsvold, M.; Frost, T.K.; Svarstad, M.B.E.; Grini, P.G.; Willumsen, C.F.; Torvik, H. (2004-01-01). "Meeting the Zero Discharge Challenge for Produced Water". SPE International Conference on Health, Safety, and Environment in Oil and Gas Exploration and Production. Society of Petroleum Engineers. doi:10.2118/86671-ms. ISBN 9781555639815.